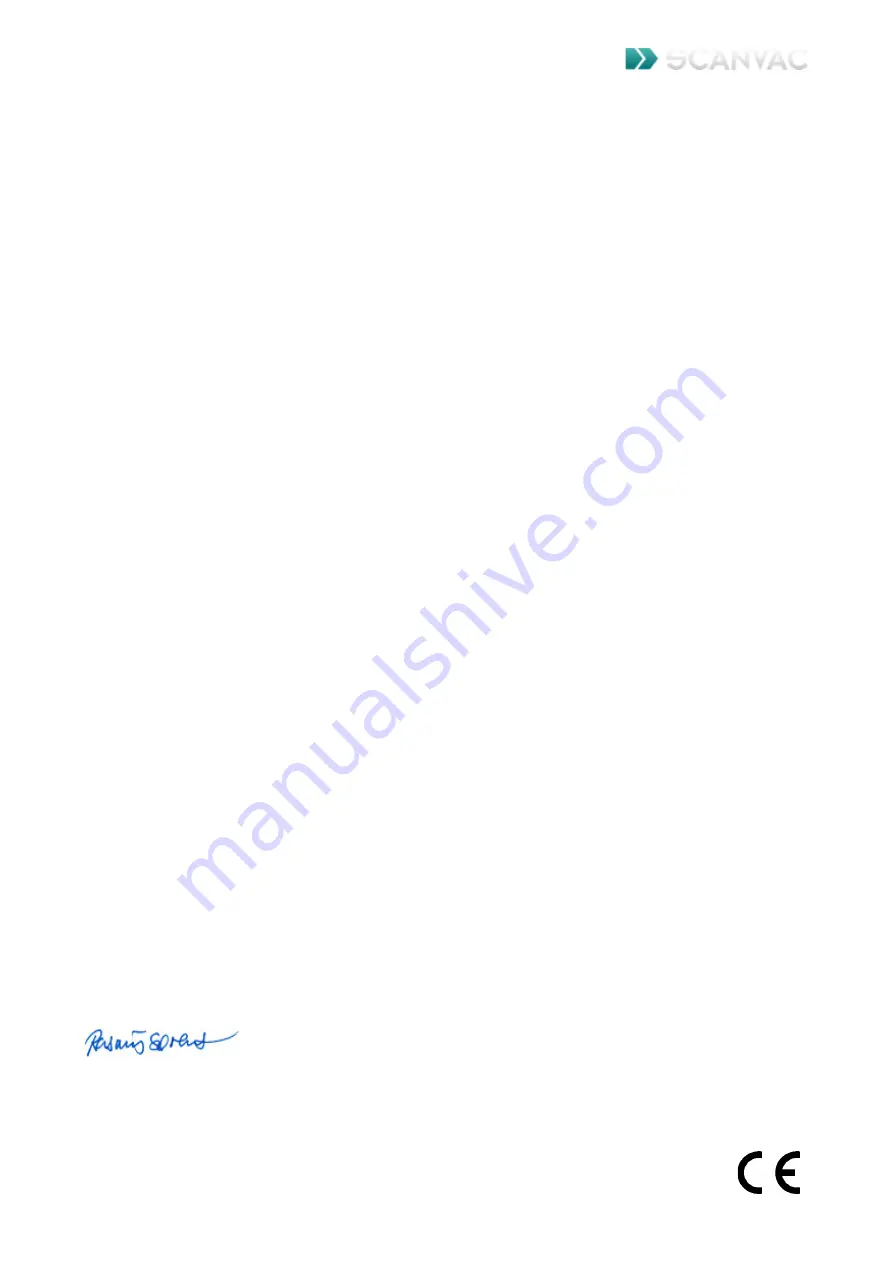
Declaration of conformity
08012013QA
We declare under our responsibility, that the following product:
Model:
ScanVac CoolSafe 90-80 Pro Freeze Dryer
to which this declaration relates is in conformity with the following standard(s), directives or other
normative document(s):
In compliance with:
EN 61010-1
- Safety requirements for electrical equipment for measurement, control and
laboratory use - General requirements
EN 61326-1
- Electrical equipment for measurement, control and laboratory use - EMC
requirement - General requirements.
EN 378-1
- Refrigerating system and heat pumps - Safety and environmental requirements -
Basic requirements, definitions, classification and selection criteria.
EN 378-2
- Refrigerating systems and heat pumps - Safety and environmental requirements -
Design, construction, testing, marking and documentation.
Following the provisions of:
2006/42/EC
- Machinery Directive, as amended
2006/95/EC
- Low Voltage Directive, as amended
2004/108/EC
- EMC Directive, as amended
97/23/EC
- Pressure equipment, as amended
2011/65/EU
- RoHS Directive
2012/19/EU
- WEEE Directive
Lynge, January 2013
Rasmus Sørensen
QA Manager
LaboGene ApS, Industrivej 6-8, Vassingerød, 3540 Lynge, Denmark