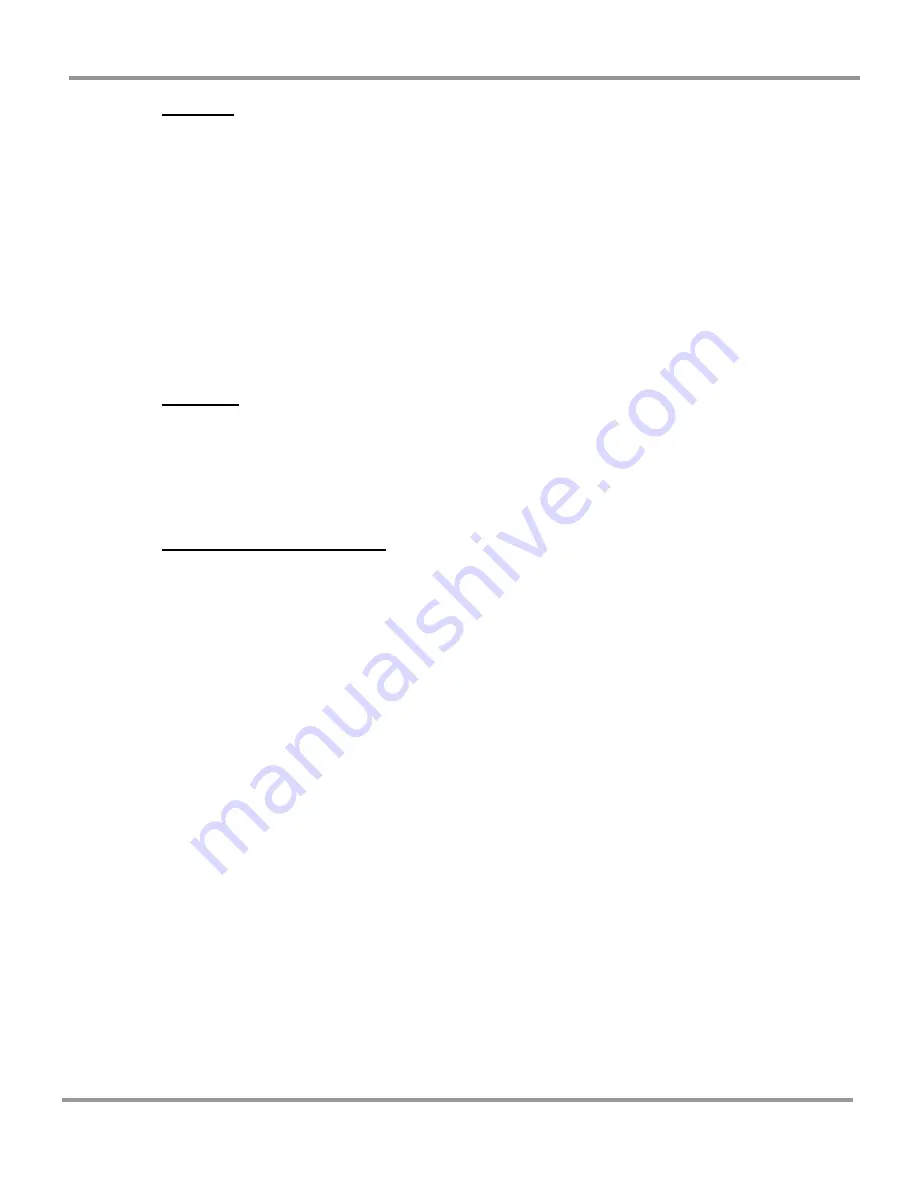
Chapter 5: Maintaining Your Freeze Dryer
Product Service 816-333-8811 or 1-800-522-7658
27
Monthly:
1.
The rubber components on the Freeze Dryer may eventually deteriorate and
require replacement. The effective life of rubber parts depends upon both their
usage and the surrounding environment. Check all rubber hoses and gaskets
and replace any that show signs of hardening, permanent set or deterioration.
2.
Using a soft cloth, sponge or chamois and a mild, non-abrasive soap or
detergent, clean the acrylic chamber lid.
3.
Using a soft cloth, sponge, or chamois and a mild, non-abrasive soap or
detergent, clean the exterior surfaces of the Freeze Dryer. Liquid spray
cleaners and polishes may be used on the exterior surfaces. Do not use
solvents to remove stains from the exterior surfaces as they may damage the
finish.
Annually:
1.
Every 12 months, or more often if the Freeze Dryer is operated in a dusty
environment, the refrigeration system condenser should be cleaned. Using a
vacuum cleaner with brush attachment, clean the condenser to ensure proper
airflow for peak performance.
Front Access Panel Removal (Console Models)
The front stainless steel panel can be removed by placing a flat blade screwdriver
in the rectangular hole in the center of the kick panel. Pivot the handle downward
to disengage the latch and simultaneously pull the bottom edge of the lower panel
forward. The lower panel is installed by first sliding the top edge under the lip on
the plastic control panel. Pivot the bottom inward and push until the latch is
secure.
Summary of Contents for FreeZone 74200 Series
Page 5: ......
Page 53: ...Product Service 1 800 522 7658 48 APPENDIX B FREEZE DRYER DIMENSIONS Model 76705xx ...
Page 62: ...Appendix D Freeze Dryer Accessories Product Service 816 333 8811 or 1 800 522 7658 57 ...
Page 63: ...Appendix D Freeze Dryer Accessories Product Service 816 333 8811 or 1 800 522 7658 58 ...
Page 64: ...Appendix D Freeze Dryer Accessories Product Service 816 333 8811 or 1 800 522 7658 59 ...
Page 65: ...Appendix D Freeze Dryer Accessories Product Service 816 333 8811 or 1 800 522 7658 60 Ampules ...