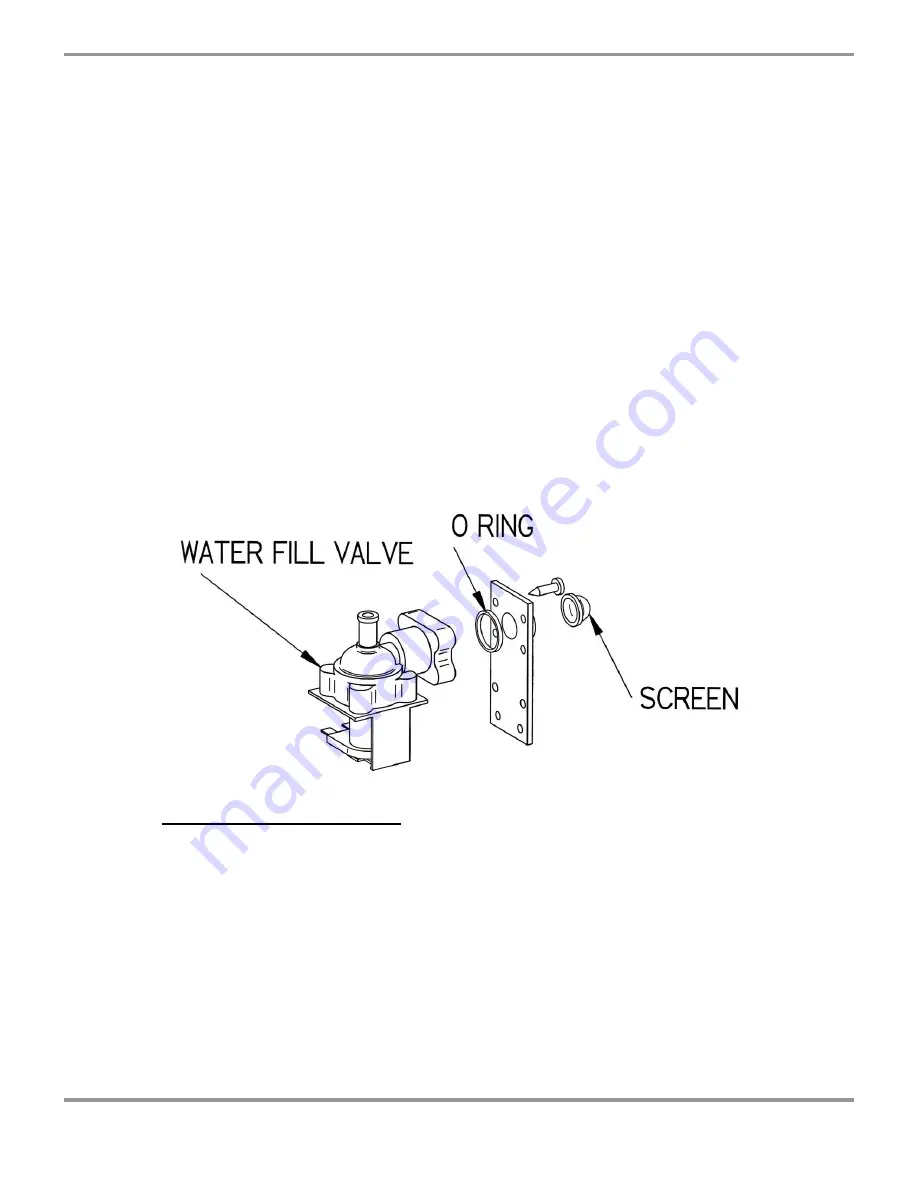
Chapter 5: Maintaining Your Washer
Product Service 1-800-522-7658
36
5.
When the washer fills the second time, open the washer and add two cups of
4-8% acetic acid (or white vinegar) to the bottom of the tank.
6.
Close the washer door and allow the unit to wash and drain without further
interruption.
Maintaining the Air Gap in Drain
If the installation included an air gap (recommended) it requires periodic cleaning.
The air gap is not part of the washer; therefore, it is not covered by the washer
warranty. The air gap protects the washer against water backing up in the event
of a clogged drain. Check the air gap for build-up any time your washer is not
draining well.
Most types of air gaps are easy to clean. Simply follow the manufacturer’s
directions for maintaining your air gap.
Maintaining the Water Fill Valve
The filter screen of the water fill valve, illustrated below, may require periodic
cleaning to remove trapped particles. A low water fill occurs if the blockage is
not removed.
To clean the water fill valve:
1.
Turn off the water and electrical power to the washer.
2.
Remove the rear panel.
3.
Disconnect the water supply tube that is connected to the valve.
4.
Remove the valve from the base.
5.
Remove the four screws from the valve plate and separate the valve from the
inlet connection.
6.
Remove the valve filter screen and clean it under running water.
7.
Replace the screen and reassemble the valve connection. Be certain the O-ring
gasket is positioned in the groove in the fill valve body.