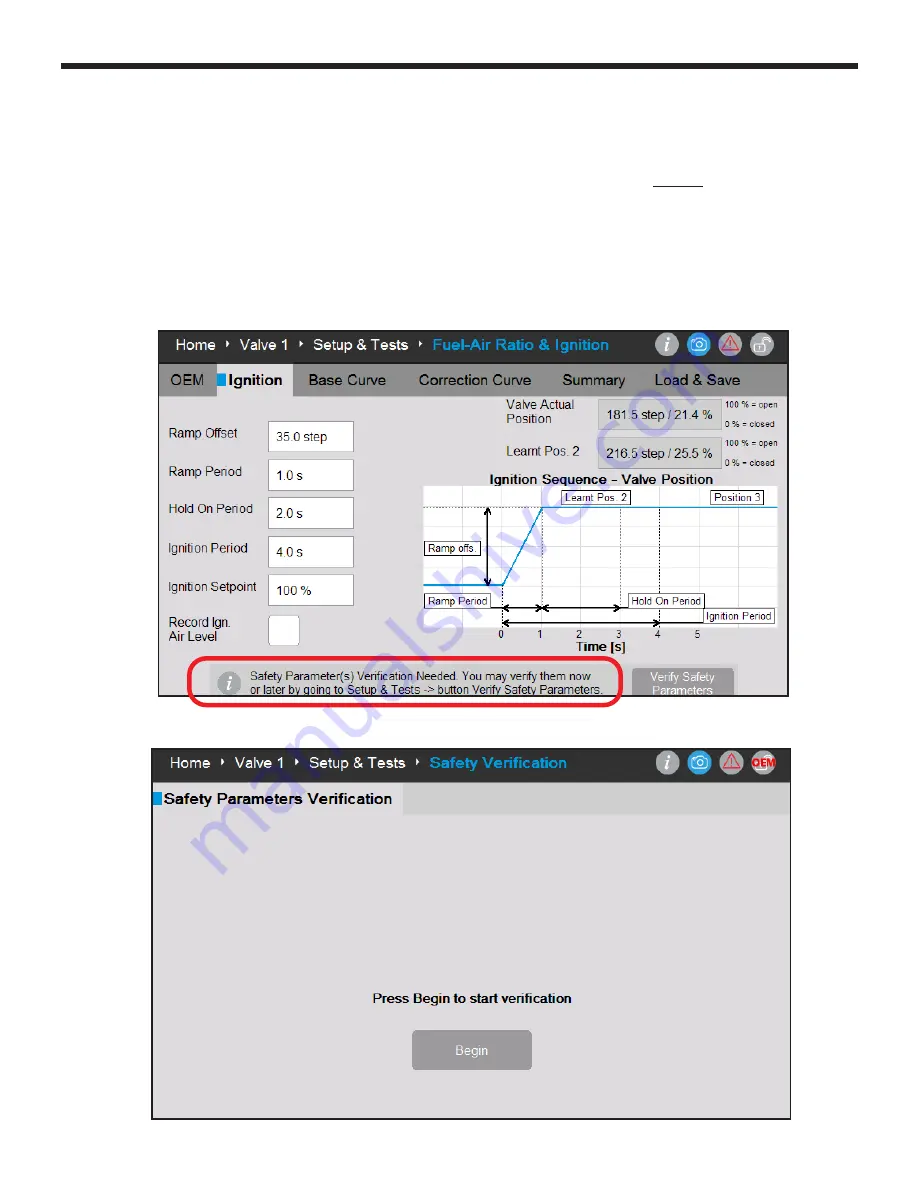
Page 98
Verification is a required process when changes to safety parameters are made. Verification forces a review of the
changes made and allows those changes to be accepted.
1. When a setting is changed that requires verification a notification will appear at the
bottom of the screen.
Press the Verify Safety Parameters button to proceed to the verification process.
2. Select begin to start the verification process.
3.
Select yes if the parameter change is correct. Select No if the parameter change is incorrect. If No is selected
the parameter must be changed to the correct setting and the verification process started again.
4. If yes is selected, press the reset button on the gas valve face when prompted to complete the verification
process.
9.F Verification Menu
LAARS Heating Systems