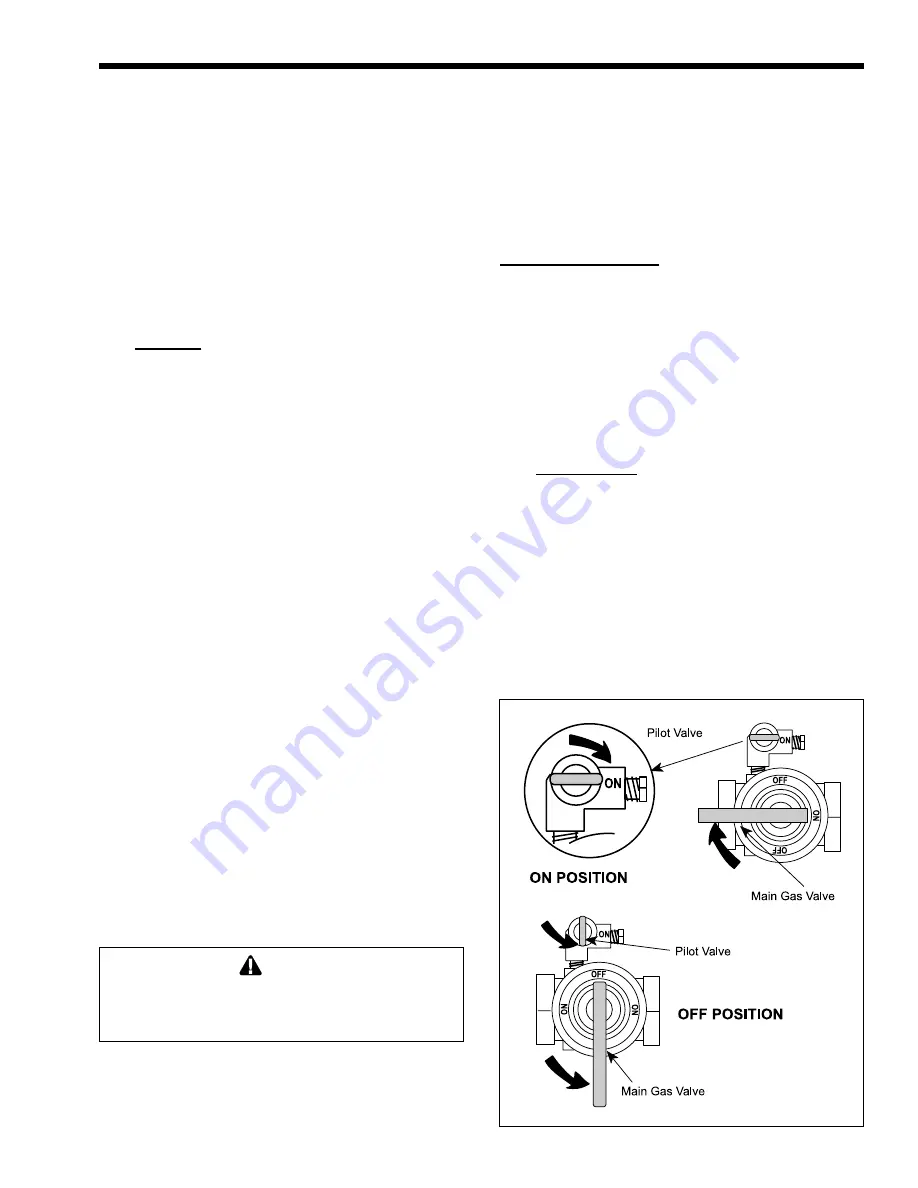
Mighty Therm Hydronic Boiler
Page 13
4.
Flow Switch:
Standard on all models: Models HH and
PH, the switch is mounted in the outlet
“tee” connection. The flow switch shuts
down all burners in case of pump failure.
5.
Low Water Cut Off (Optional):
The low water cut off automatically shuts
off boiler whenever water level drops
below probe. Located at boiler inlet (model
PH) and at return header (model HH).
3B. Initial Start-Up
Lighting:
Safe lighting and other performance
criteria were met with the gas manifold and control
assembly provided on the boiler when it underwent
tests specified in the ANSI Z21.13 standard.
Before placing the boiler in operation, be certain
that the boiler is filled with water and all air is purged
from the system. Once the boiler is connected to the
gas supply, the automatic safety shutoff devices must
be checked.
1.
Before beginning the tests, make sure the main
manual gas valve, and any other boiler firing
valves are in the “OFF” position.
2.
Make sure the boiler’s power switch is in the
“ON” position. After placing the manual pilot
gas valve in the open position and resetting all
safety devices, (high limit, pressure switch, low-
water cutoff, etc.) pilot(s) can be lit following
the procedure located on the boiler rating plate.
3.
Once the pilot(s) is lit and has been established
for five minutes, the flame failure response time
should be checked as follows:
Systems 9 and 4
- (Intermittent ignition), natural
gas only: With this system pilots are automatically lit
when the operating controls call for heat. If the pilot
flame fails for any reason, the main valve is shut off
within one second and the pilot spark ignition is
initiated until the pilot flame has been reestablished.
On propane systems, unit locks out for safety. This
sequence should be checked by turning off the manual
pilot gas valve, and, at the same time, monitoring the
audible sparking at the pilot burner and signal
interruption to the main valve.
Caution
Propane gas is heavier than air and sinks to
the ground. Exercise extreme care in lighting
the boiler when so equipped.
System 16
- (Electronically supervised standing
pilot system): Extinguish the pilot flame by placing
the manual pilot valve in the closed position, and at
the same time, begin recording the time it takes for the
output signal from the electronic ignition control to be
Figure 14. Gas Manual Valves.
interrupted. The signal interruption can be detected
either with a test light or a voltmeter. The response
time should never exceed one second.
4.
With the pilots lit, initial activation of the main
burners can be achieved by slowly opening the
main valve. The result should be a smooth
lighting of the main burners.
Hi-Limit Checkout :
After running the boiler for a long enough
period, bring the water temperature within the range
of the hi-limit and slowly back off the high limit
setting until the boiler shuts off. The main burners
should reignite when the hi-limit is reset and turned
back up to its original setting. The boiler should now
run until it shuts off automatically on operating
aquastat.
3C. To Start Up System:
1.
Start Up Boiler
Be certain system pump is running, then proceed
as follows:
a.
Turn off main electrical switch.
b.
Turn off all manual gas valves and wait
five minutes (see Figure 14).
c.
Set operating control to lowest setting.
d.
Slowly turn manual gas valve to “ON”.
e.
Reset all safety valve switches (manual
reset high limit and low water cut off).