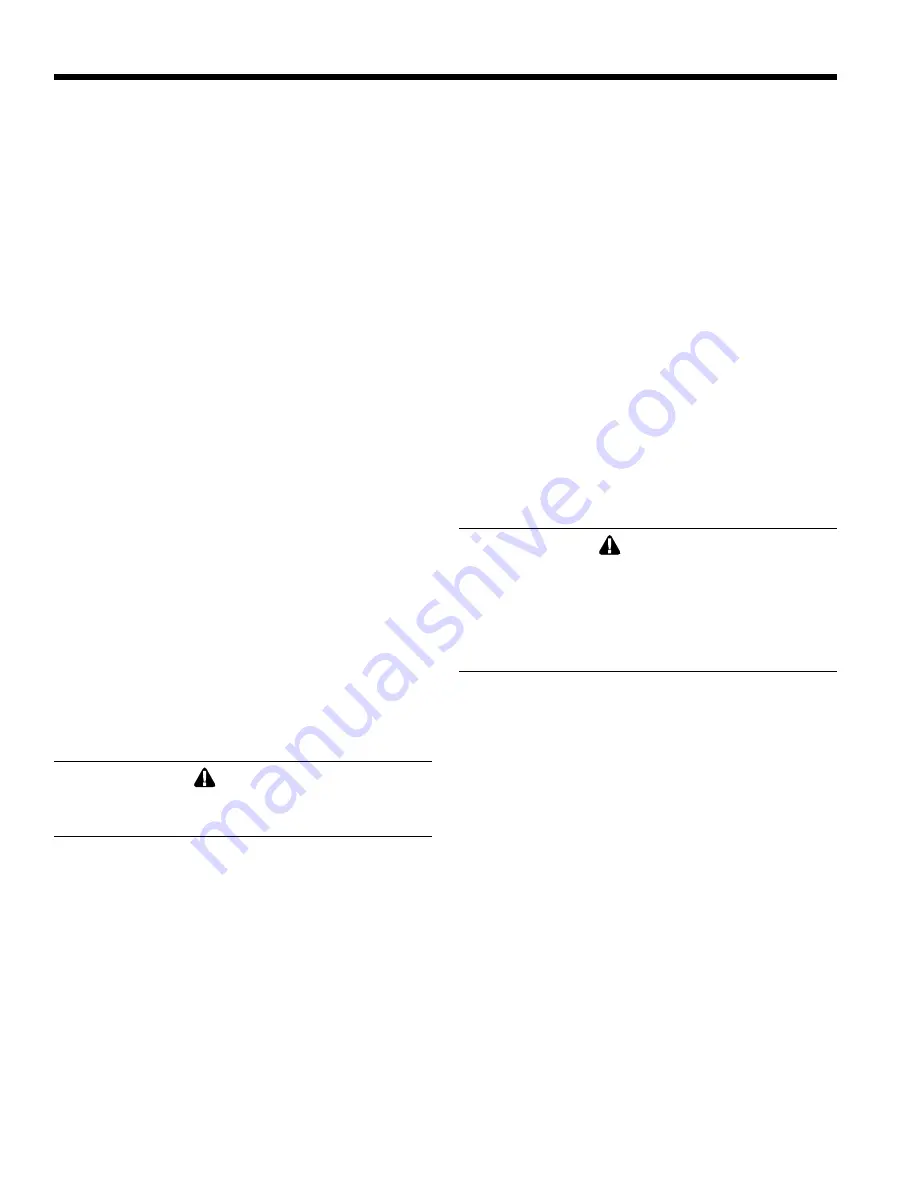
LAARS Heating Systems
Page 4
SECTION 2.
Operating Instructions
2.1 Filling the Boiler System
1.
Ensure the system is fully connected. Close all
bleeding devices and open make-up water valve.
Allow system to fill slowly.
2.
Move manual lever on 3-way valve actuator to
"open" position, allowing air to purge from boiler
loop. Valve is normally in DHW position until
there is a call for Central Heat via "T-T" contacts.
If make-up water pump is employed, adjust
pressure switch on pumping system to provide a
minimum of 12 psi (81.8 kPa) at the highest point
in the heating loop.
3.
If a water pressure regulator is provided on the
make-up water line, adjust the pressure regulator to
provide at least 12 psi (81.8 kPa) at the highest
point in the heating loop.
4.
Open bleeding devices on all radiation units at the
high points in the piping throughout the system,
unless automatic air bleeders are provided at such
points.
Note that there is an air bleed located on the left
side of Mascot II, on top of the jacket.
5.
Cycle the boiler pump on and off 10 times, 10
seconds on and 10 seconds off to remove all air
from the heat exchanger. Then run system and
appliance pump for a minimum of 30 minutes with
the gas shut off.
6.
Using manual lever located on left side of 3-way
valve actuator, move from "open" position back to
closed position repeatedly. This process forces air
out of the internal DHW loop.
WARNING
Failure to remove all air from the heat exchanger could
lead to property damage, severe injury or death.
7.
Recheck all air bleeders as described in Step 4.
8.
Start up boiler according to the procedure in this
manual. Operate the entire system, including the
pump, boiler, and radiation units for one (1) hour.
9.
Shut down the entire system and vent all radiation
units and high points in the system piping, as
described in Step 4.
10.
Close make-up water valve and check strainer in
pressure reducing valve for sediment or debris
from the make-up water line. Reopen make-up
water valve.
11.
Check gauge for correct water pressure and also
check water level in the system. If the height
indicated above the boiler insures that water is at
the highest point in the circulating loop, then the
system is ready for operation.
12.
Refer to local codes and the make-up water valve
manufacturer’s instructions as to whether the
make-up water valve should be left open or closed.
13.
After placing the unit in operation, the ignition
system safety shutoff device must be tested.
First, shut off the manual gas valve, and call the
unit for heat. Main gas terminals will be energized,
attempting to light, for four (4) seconds, and then
will de-energize. The unit will go into lockout after
the required number of trial for ignition periods.
Second, turn the power off, press the manual reset
button on the boiler control, or the user display,
open the manual gas valve and allow the unit to
light. While the unit is operating, close the manual
gas valve and ensure that power to the main gas
valve has been cut.
14.
Within three (3) days of start-up, recheck all air
bleeders and the expansion tank as described in
Steps 4 and 8 above.
Important Note:
The installer is responsible for
identifying to the owner/operator the location of all
emergency shutoff devices.
WARNING
Do not use this appliance if any part has been under
water. Immediately call a qualified service technician
to inspect the appliance
and to replace any part of the control system and any
gas control that may have been
under water.
2.2 Operating the Burner and Set Up
Initial setup must be checked before the unit is put
in operation. Problems such as failure to start, rough
ignition, strong exhaust odors, etc. can be due to
improper setup. Damage to the boiler resulting from
improper setup is not covered by the limited warranty.
2.2.1 Burner Operation
REQUIRED TOOLS:
differential pressure gauge
capable of reading negative 0.01 inches W.C. (0.002kPa),
screw drivers, and combustion analyzer.
1.
Using this manual, make sure the installation is
complete and in full compliance with the
instructions and all local codes.
2.
Determine that the appliance and system are filled
with water and all air has been bled from both.
Open all valves.
3.
Observe all warnings on the Operating Instructions
label and turn on gas and electrical power to
appliance.
4.
Mascot II will enter the start sequence. Blower and
pump will energize for pre-purge, then the ignition
sequence starts. After all safety devices are
verified, the gas valve opens. If ignition doesn’t
occur, turn off the Mascot II, check that there is