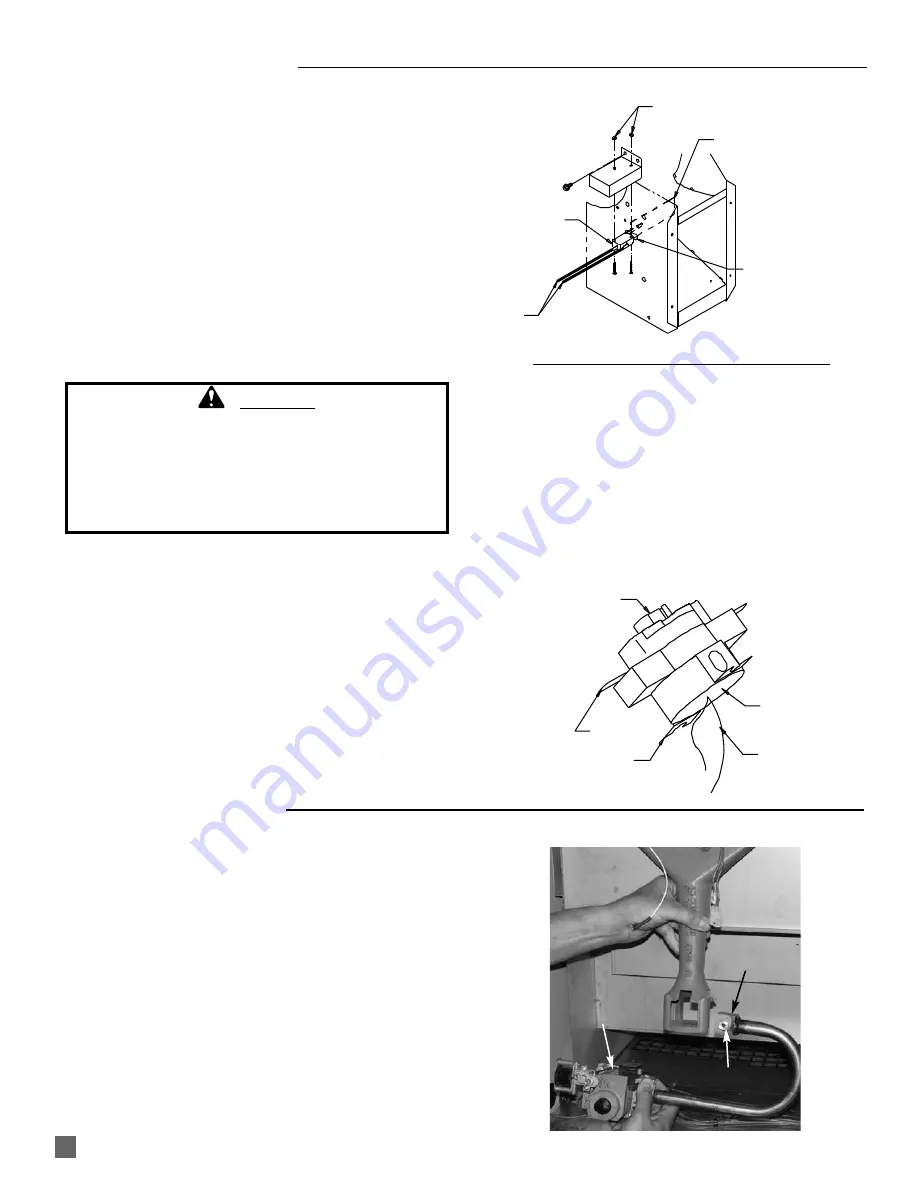
17
AIR PROVING SWITCH
SWITCH W/ PADDLE
LEADS
NUTS
PADDLE
OBLONG HOLE
HOUSING SIDE
PANEL
1.
Remove two sheet metal screws holding air proving
switch blower housing. Remove assembly by turning
switch assembly 90 degrees so the switch paddle
can be pulled through oblong hole on side of fan
housing. See Fig. 13.
3.
Disconnect the leads from the air proving switch.
4.
When installing replacement switch, use care in not
bending the switch arm, otherwise ignition problems
may occur.
FIG. 13
The high limit switch should be tested a minimum of once
per year when the heater is given a thorough cleaning.
1.
Re m ove t h e h i g h l i m i t s w i t c h f ro m t h e h e a t
chamber.
2.
Holding the switch by one of its mounting legs or
electrical terminals, apply a small flame only to the
sensing surface on the back of the switch. Be
careful not to melt the plastic housing of the switch
when conducting this test.
3.
Within a minute, you should hear a pop coming
from the switch, which indicates the contacts of the
switch have opened.
4.
Allow the switch cool down for about a minute
before firmly pressing the red reset button on the
switch.
5.
Check for electrical continuity across the switch
terminals to make sure the contacts have closed.
6.
Reinstall the switch back into the heater.
FIG. 14
TESTING THE MANUAL RESET HIGH LIMIT SWITCH
RESET BUTTON
SENSING
SURFACE
TERMINAL
FLAME
MOUNTING
LEG
WARNING
Fire Hazard
■
Do not operate the heater with the high limit switch
bypassed.
■
Operating the heater with a bypassed high limit switch
may lead to overheating, possibly resulting in a fire,
with subsequent damage to the heater, building
damage, or loss of livestock.
GAS CONTROL VALVE
1.
Remove the following
-- Hose and sediment trap from inlet of gas valve
-- Screws securing valve bracket to heater base.
-- Burner bolt from underside of base.
-- Screws and spacers securing burner casting to
heat chamber.
2.
Remove control valve with burner from heater. Pivot
the valve/manifold assembly as necessary so orifice
block on manifold clears the burner casting venturi
port..
3.
Replace components as needed.
FIG. 15
ORIFICE
BLOCK
GAS CONTROL
VALVE
BURNER
ORIFICE