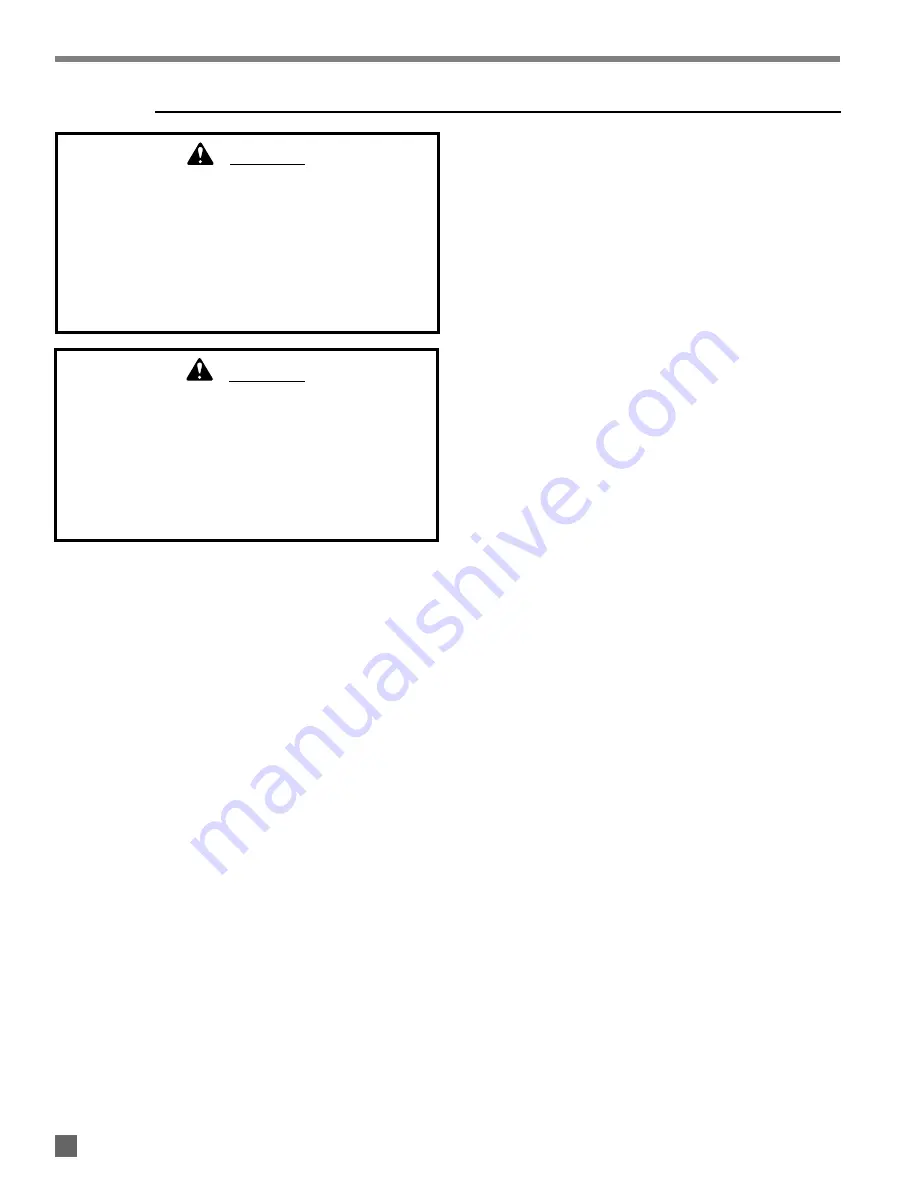
1. Read all safety precautions and follow L. B. White
recommendations when installing this heater. If
during the installation or relocating of heater, you
suspect that a part is damaged or defective, call a
qualified service agency for repair or replacement.
2. Insure that all accessories that ship within the heater
have been removed from inside of heater and
installed. This pertains to gas hose, regulators, etc.
3. Make sure the heater is properly positioned before
use. Observe and obey all minimum safe distances of
the heater to the nearest combustible materials.
Minimum safe distances are given on the heater
dataplate and on page 4 of this manual.
4. The heater is designed for either indoor or outdoor
use. For outdoor application, the heater is approved
for use with a .3 meter diameter by 4 meter long
flexible duct and air diffuser as supplied by the L.B.
White Co. The heater shall not be used with any other
ducting or ductwork.
5. Heaters used in the vicinity of combustible tarpaulins,
canvas, plastic wind barriers, or similar coverings and
materials shall be located at least 3 m from the
coverings. The coverings shall be securely fastened
to prevent ignition or upsetting of the heater due to
wind action on the covering or other materials.
6. The heater shall be located so that rain, ice, or snow
drainage from the structure does not affect heater
operation. If the heater is installed outside, it must
be installed above any pooled or standing water. If
the heater is located on the ground, a surrounding
trench is recommended to drain any rain, ice or snow
away from the heater.
7. The heater must be installed on a flat, horizontal
surface.
8. Locate the heater so as to protect it from tipover or
accidental movement.
9. The heater must be installed so as not to interfere
with or obstruct normal exits, emergency exits, doors
and walkways.
10. Railing, fencing or suitable substitute materials
should be used as needed to isolate the heater from
people using and visiting the temporary structure.
11. Do not use the heater equipment area for storage of
any other materials.
12. The ground and surrounding terrain must be cleared
of any combustible vegetation and other combustible
materials.
13. Protect any electrical wiring and gas hoses with a
shield device of suitable nature to protect both from
equipment and people traffic.
14. This heater is supplied with a gas pressure regulator.
Make sure that gas regulator is appropriate for the
fuel source; LP-Gas or natural gas. The regulator
must be properly connected to the LP-Gas cylinder or
natural gas supply to assure that gas pressure at the
inlet to the gas valve is regulated within the range
specified on the dataplate. The heater’s gas
regulator (with pressure relief valve) should be
installed outside of the tent. Any regulators within the
tent must be properly vented to the outside. Local,
regional and national codes always apply to regulator
installation. Contact your gas supplier or local L. B.
White agent if there are any questions.
15. Check all connections for gas leaks using approved
gas leak detectors. Gas leak testing is performed as
follows: Check all pipe connections, hose
connections, fittings and adapters upstream of the
gas control with approved gas leak detectors. In the
event a gas leak is detected, check the components
involved for cleanliness and proper application of pipe
compound before further tightening. Further tighten
the gas connections as necessary to stop the leak.
After all connections are checked and any leaks are
stopped, turn on the main burner. Stand clear while
the main burner ignites to prevent injury caused from
hidden leaks that could cause flashback. With the
Installation Instructions
GENERAL
WARNING
Fire and Explosion Hazard
Can cause proper damage, severe injury or death.
■
Disconnect power supply before wiring to prevent
electrical shock or equipment damage.
■
To avoid dangerous accumulation of fuel gas, turn off
gas supply at the appliance service valve before
starting installation, and perform gas leak test after
completion of installation.
8
WARNING
Fire and Explosion Hazard
■
Do not use open flame (matches, torches, candles,
etc.) in checking for gas leaks.
■
Use only approved leak detectors.
■
Failure to follow this warning can lead to fires or
explosions.
■
Fires or explosions can lead to property damage,
personal injury or loss of life.