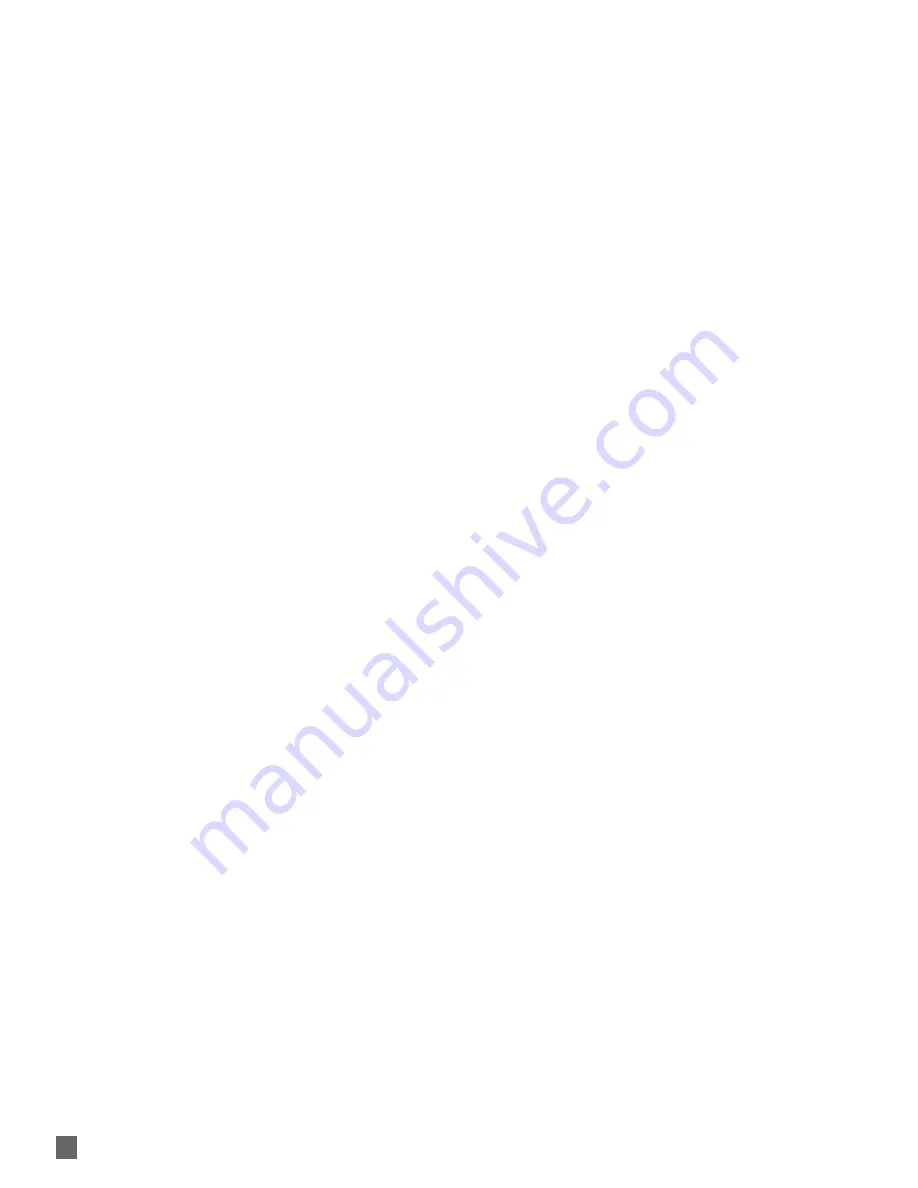
SPARK IGNITION OPERATION SEQUENCE:
— A call for heat occurs from the building’s environment
control.
— 1-15 VDC is sent from the SmartBox
™
variable rate heat
controller to the variable rate solenoid on gas control
valve.
— Line voltage is sent to transformer and to ignition control
— 24 V.A.C. is sent from transformer to the ignition control.
— A call for heat occurs
— Red light on ignition control is illuminated
— Ignition control module performs an internal safe start
check
-- Internal components are tested
-- Amperage is sent to flame sensor from ignition
control to start flame proving process.
-- Ignition control terminal PS1 sends 24 volts to air
proving switch.
— Ignition control module begins safety lockout timing
— Ignition control module sends 115 volts from terminal
IND to the fan motor.
-- fan motor starts
-- Air proving switch closes and 24 volts is returned
to ignition control terminal PS2.
— Ignition control powers the igniter and igniter sparks.
— Ignition control sends 24 volts from terminal MV to gas
control through high limit switch.
— Ignition occurs
-- Igniter continues to spark until flame proving
occurs.
-- Igniter spark is discontinued
-- Gas valve stays open
— Room warms to desired temperature
-- Room sensor is satisfied
-- Heater shuts down
— Process begins again on call for heat
MULTIPLE IGNITION TRIAL SEQUENCE
— First trial for ignition takes approximately 10 seconds
— Two more trials for ignition willoccur
-- Second and third trial follow immediately if first
trial fails
— M o d u l e s t a r t s a 15 m i n u te wa i t p e r i o d to a l l ow
ignition interruption to pass
— Ignition control repeats 3 ignition attempts after 15
minute wait period
— If ignition control module does not prove flame after third
trial, the module goes into safety lockout (3 flash pattern)
-- Igniter shuts down
-- Fan motor svtops
-- Gas valve closes
— Ignition control must be reset
-- Unplug the heater and plug it back in
-- OR --
-- Turn building controller off and then back on to call
for heat
20
Summary of Contents for GUARDIAN Smart Sense AD250
Page 31: ......