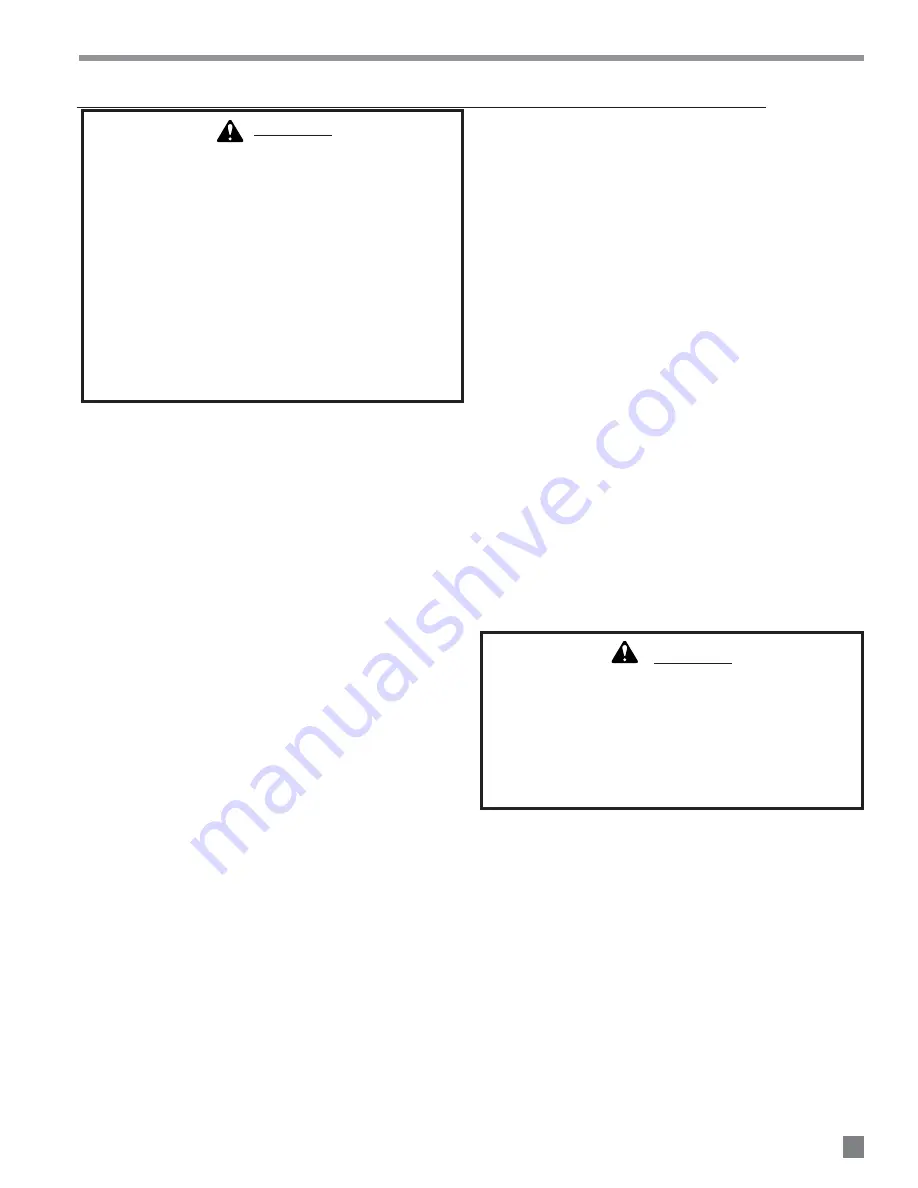
1. Read all safety precautions and follow L. B. White
recommendations when installing this heater. If
during the installation or relocating of heater, you
suspect that a part is damaged or defective, call a
qualified service agency for repair or replacement.
2. Make sure the heater is properly positioned before
use and is hung level. Observe and obey all minimum
safe distances of the heater to the nearest
combustible materials. Minimum safe distances are
given on the heater nameplate and on page 4 of this
manual.
3. For heaters intended for outdoor installation, the
heater is to be installed at least 46 cm above the
ground or to a height that would prevent snow
blockage of heater’s air inlet.
4. The heater may be used either indoors or outdoors.
When the heater is mounted outdoors, use only the
ductwork supplied in the outdoor mounting kit.
5. The heater’s approved gas regulator (with pressure
relief valve) should be installed outside of building.
Any regulators inside the buildings must be properly
vented to the outside. Local, state and national
codes always apply to regulator installation. Natural
gas regulators with vent limiting device may be
mounted indoors without venting to outdoors.
6. Insure that all accessories that ship within the heater
have been removed from inside of heater and
installed.
7. Make certain that a sediment trap is installed at the
gas valve inlet to prevent foreign materials (pipe
compound, pipe chips and scale) from entering the
gas valve. Debris blown into the gas valve may cause
that valve to malfunction resulting in a serious gas
leak that could result in a possible fire or explosion
causing loss of products, building or even life. A
properly installed sediment trap will keep foreign
materials from entering the gas valve and protect the
safe functioning of that important safety component.
8. Any heater or appliance connected to a piping system
must have an accessible, approved manual shut off
valve installed within 1.83 meters of the heater it
serves.
9. Check all connections for gas leaks using approved
gas leak detectors. Gas leak testing is performed as
follows: Check all pipe connections, hose
connections, fittings and adapters upstream of the
gas control with approved gas leak detectors. In the
event a gas leak is detected, check the components
involved for cleanliness and proper application of
pipe compound before further tightening. Further
tighten the gas connections as necessary to stop the
leak. After all connections are checked and any leaks
are stopped, turn on the main burner. Stand clear
while the main burner ignites to prevent injury caused
from hidden leaks that could cause flashback. With
the main burner in operation, check all connections,
hose connections, fittings and joints as well as the
gas control valve inlet and outlet connections with
approved gas leak detectors. If a leak is detected,
check the components involved for cleanliness in the
thread areas and proper application of pipe
compound before further tightening. Further tighten
the gas connection as necessary to stop the leak. If
necessary, replace the parts or components involved
if the leak cannot be stopped. Ensure all gas leaks
have been identified and repaired before proceeding.
10. A qualified service agency must check for proper
operating gas pressure upon installation of the
heater.
11. Light according to instructions on the heater or within
owner’s manual.
12. It is extremely important to use the proper size and
type of gas supply line to assure proper functioning of
the heater. Refer to standard AS5601 Gas
Installations. Contact your fuel gas supplier for proper
line sizing and installation.
13. Make sure the heater is fitted with an approved
regulator. A regulator must be connected to the gas
supply so that gas pressure at the inlet to the gas
valve is regulated within the range specified on the
dataplate at all times. Contact your gas supplier, or
the L. B. White Co., Inc. if you have any questions.
WARNING
Fire or Explosion Hazard.
Can cause property damage, severe injury or death.
■
Disconnect power supply before wiring to prevent
electrical shock or equipment damage.
■
To avoid dangerous accumulation of fuel gas, turn off
gas supply at the appliance service valve before
starting installation, and perform gas leak test after
completion of installation.
■
Do not force the gas control knob. Use only your
hand to turn the gas control knob. Never use any
tools. If the knob will not operate by hand, the
control should be replaced by a qualified service
technician. Force or attempted repair may result in
fire or explosion.
7
Installation Instructions
GENERAL
WARNING
Fire and Explosion Hazard
■
Do not use open flame (matches, torches, candles,
etc.) in checking for gas leaks.
■
Use only approved leak detectors.
■
Failure to follow this warning can lead to fires or
explosions.
■
Fires or explosions can lead to property damage,
personal injury or loss of life.