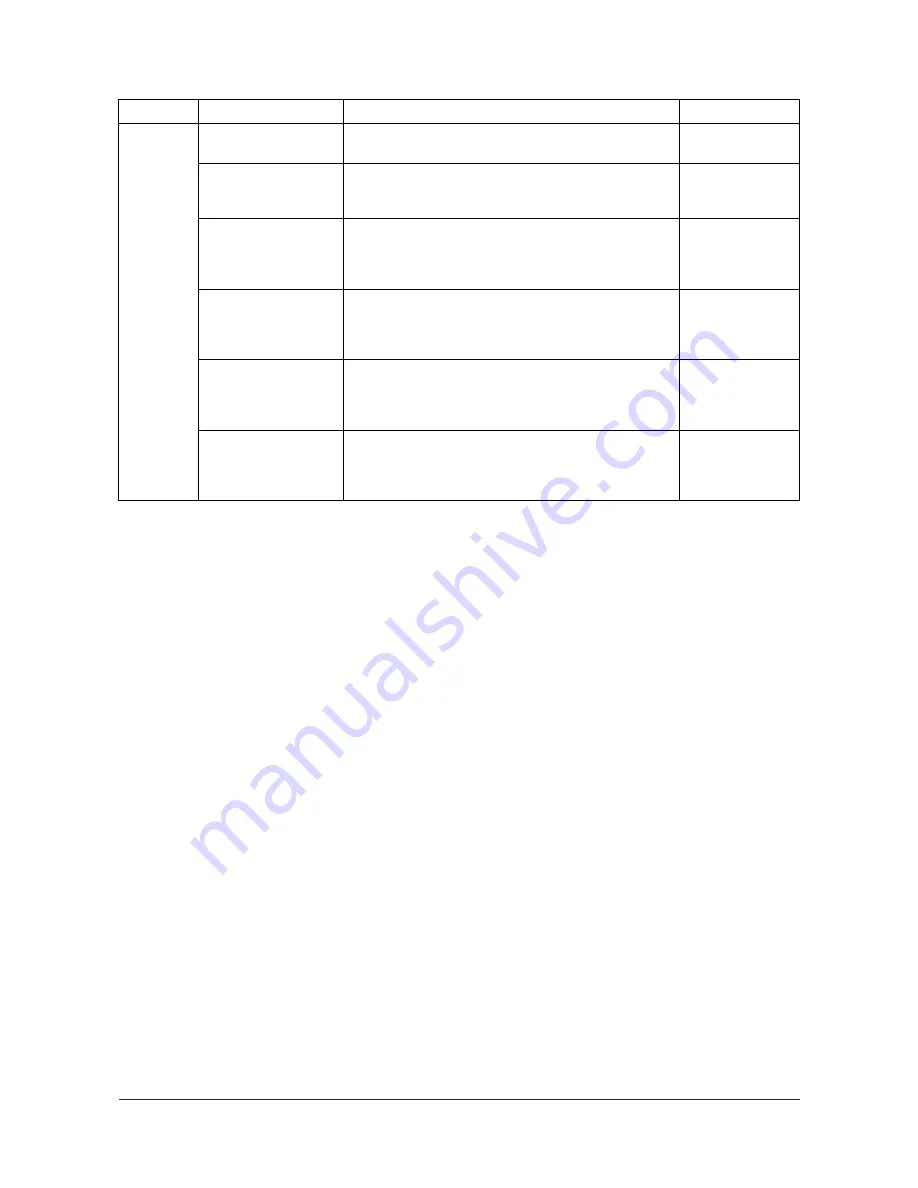
5H8
1-4-2
Section
Jam code
Conditions
Specified time
Paper feed
section
09
Sequence error JAM
Sequence error is occurred between the machine and
3000-sheet paper feeder.
-
12
No paper feed from
cassette 3
Feed switch 3 (FSW3) does not turn on within the speci-
fied time of PF paper feed clutch 1 (PFPFCL1) turning on.
670 ms
15
Misfeed in paper feeder
horizontal paper con-
veying section 1
Paper path sensor 3 (PPS3) does not turn on within spec-
ified time of PF paper feed clutch 2 (PFCL2) turning on.
360 ms
16
Misfeed in paper feeder
horizontal paper con-
veying section 2
Paper path sensor 2 (PPS2) does not turn on within spec-
ified time of the paper path sensor 3 (PPS3) turning on.
380 ms
17
Misfeed in paper feeder
horizontal paper con-
veying section 3
Paper path sensor 1 (PPS1) does not turn on within spec-
ified time of the paper path sensor 2 (PPS2) turning on.
250 ms
24
Multiple sheets in cas-
sette 3 paper feed sec-
tion
Feed switch 3 (FSW3) does not turn off within specified
time of its turning on.
2140 ms
Service Manual Y11
2030
-
5
Summary of Contents for PF-760
Page 1: ...PF 760 Option Copier SERVICE MANUAL Code Y112030 5...
Page 3: ...This page is intentionally left blank...
Page 9: ...This page is intentionally left blank...
Page 11: ...5H8 This page is intentionally left blank...
Page 15: ...5H8 1 1 4 This page is intentionally left blank Service Manual Y112030 5...
Page 47: ...5H8 2 1 6 This page is intentionally left blank Service Manual Y112030 5...
Page 51: ...5H8 2 2 4 This page is intentionally left blank Service Manual Y112030 5...
Page 57: ...5H8 2 4 2 This page is intentionally left blank Service Manual Y112030 5...
Page 59: ...UPDATINGSTATUS DATE UPDATEDPAGES PAGES CODE 04 2010 1ST EDITION 59 Y112030 5...