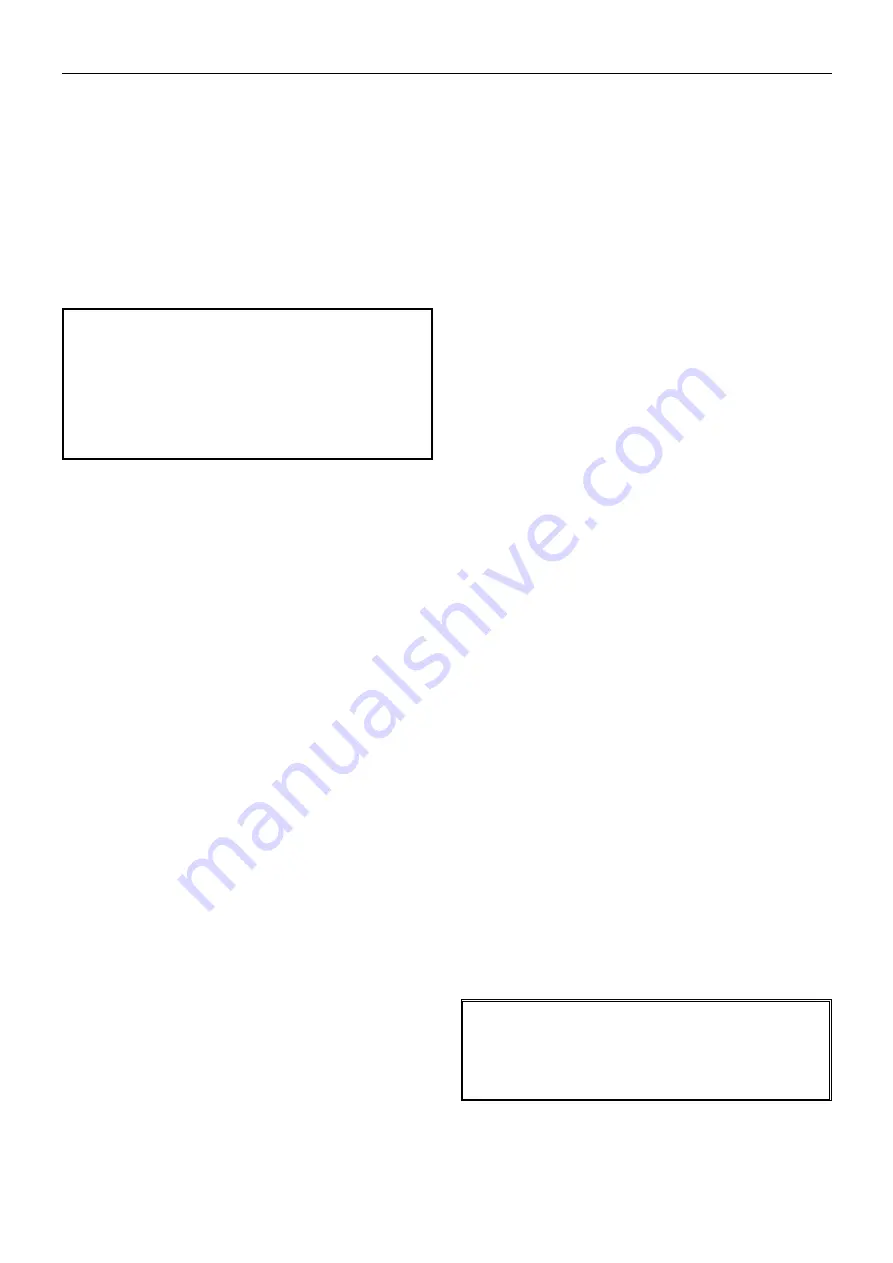
___________________________________________________________________________________________
4
EA341
SECTION 4 : ADJUSTMENT OF AVR
CONTROLS
4.1
Voltage Adjustment
4.1.1 The generator output voltage is set at the factory,
but can be altered by careful adjustment of the
VOLT control on the AVR board, or by the
external hand trimmer if fitted.
Terminals J1 and J2 on the AVR will be fitted with
a shorting link if no hand trimmer is required.
WARNING
Do not increase the voltage above the rated
generator voltage. If in doubt, refer to the rating
plate mounted on the generator case.
Do not ground any of the hand trimmer terminals,
as these could be above earth potential. Failure
to observe this could cause equipment damage.
4.1.2 If a replacement AVR has been fitted or re-setting
of the VOLT adjustment is required, proceed as
follows :
(1) Before running generator, turn the VOLT
control fully anti-clockwise.
(2) Turn remote VOLT trimmer (if fitted) to
midway position.
(3) Turn STABILITY control to midway position.
(4) Connect a suitable voltmeter (0
300 Vac)
across line to neutral of the generator.
(5) Start generator set, and run on no load at
nominal frequency e.g. 50
53 Hz or 60
63
Hz.
(6) If the red Light Emitting Diode (LED) is
illuminated, refer to the Under Frequency Roll
Off (UFRO) adjustment.
(7) Carefully turn VOLT control clockwise until
rated voltage is reached.
(8) If instability is present at rated voltage, refer to
stability adjustment, then re-adjust voltage if
necessary.
(9) Voltage adjustment is now completed.
4.2
Stability Adjustment
4.2.1 The AVR includes stability or damping circuit to
provide good steady state and transient
performance of the generator.
4.2.2 A jumper link selector is provided to optimize the
response of the stability circuit to various size
generators.
4.2.3 The link should be positioned as shown in the
diagram according to the kw rating of the
generator. The correct setting of the Stability
adjustment can be found by running the
generator at no load and slowly turning the
stability control anti-clockwise until the generator
voltage starts to become unstable. The optimum
or critically damped position is slightly clockwise
from this point (i.e. where the machine VOLT are
stable but close to the unstable region).
4.3
Under Frequency Roll Off (UFRO) Adjustment
4.3.1 The AVR incorporates an under-speed protection
circuit which gives a VOLT / Hz characteristic
when the generator speed falls below a
presentable threshold known as the
“knee” point.
The red Light Emitting Diode (LED) gives
indication that the UFRO circuit is operating.
4.3.2 The UFRO adjustment is preset and sealed and
only requires the selection of 50 or 60 Hz and 4
pole or 6 pole, using the jumper link as shown in
the diagram. For optimum setting, the LED
should illuminate as the frequency falls just below
nominal, i.e. 45 Hz on a 50 Hz system or 55 Hz
on a 60 Hz system.
4.4
DROOP Adjustment
Generators intended for parallel operation are fitted
with a quadrature droop C.T. which provides a power
factor dependent signal for the AVR. The C.T. is
connected to S1, S2 on the AVR, (see generator wiring
diagram for details). The DROOP adjustment is
normally preset in the works to give 5% voltage droop
at full load zero power factors. Clockwise increases the
amount of C.T. signal injected into the AVR and
increases the droop with lagging power factor (cos Ø ).
With the control fully anti-clockwise there is no droop.
4.5
Trim Adjustment
4.5.1 An analogue input (A1, A2) is provided to connect
to the controller or other devices. It is designed to
accept dc signals up to +/- 5 VOLT.
4.5.2 The dc signal applied to this input adds to the
AVR sensing circuit. A1 is connected to the AVR 0
VOLT. Positive on A2 increases excitation.
Negative on A2 decreases excitation.
4.5.3 The TRIM control allows the user to adjust the
sensitivity of the input. With TRIM fully
anti-clockwise the externally applied signal has
no effect. Clockwise it has maximum effect.
4.5.4 Normal setting is fully clockwise when used with a
controller.
WARNING
Any devices connected to this input must be fully
floating and galvanically isolated from ground,
with an insulation capability of 500 Vac. Failure to
observe this could result in equipment damage.