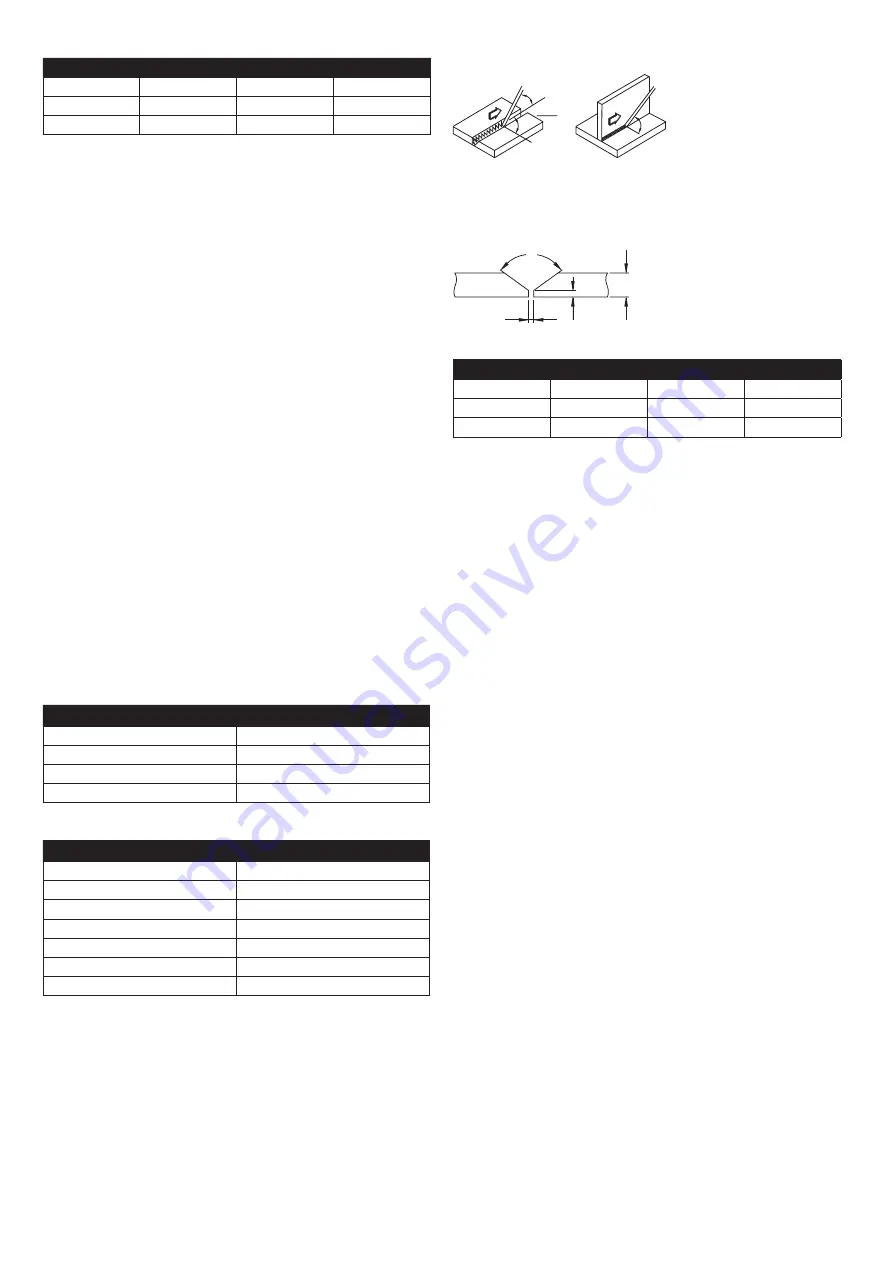
30
|
EN
Table 4
s (mm)
a (mm)
d (mm)
α (°)
0 - 3
0
0
0
3
0
0.5 (max)
0
4 - 6
1 - 1.5
1 - 2
60
Basic rules during welding by TIG method:
1.
Purity - grease, oil and other impurities must be removed from the weld
during welding. It is also necessary to mind purity of additional material
and clean gloves of the welder during welding.
2.
Leading additional material - oxidation must be prevented. To do so,
flashing end of additional ma-terial must be always under the protection
of gas flowing from the hose.
3.
Type and diameter of tungsten electrodes - it is necessary to choose them
according to the values of the current, polarity, type of basic material and
composition of protective gas.
4.
Sharpening of tungsten electrodes - sharpening the tip of the electrode
should be done in trav-erse/horizontal direction. The tinier the roughness
of the surface of the tip is, the calmer the burning of the el. arc is as well
as the greater durability of the electrode is.
5.
The amount of protective gas - it has to be adjust-ed according to the type
of welding or according to the size of gas hose. After finishing the welding
gas must flow sufficiently long to protect material and tungsten electrode
against oxidation.
Typical TIG welding errors and their impact on weld quality:
The welding current is too -
Low:
unstable welding arc
High:
Tungsten electrode tip breaks lead to turbulent arcing.
Further, mistakes may be caused by poor welding torch guidance and poor
addition of additive material.
Welding in method MMA
Switch the machine to MMA mode - coated electrode. Table 5 lists the ge-
neral values for the choice of the electrode, depending on its diameter and
the thickness of the base material. These data are not absolute and are in-
formative only. For exact selection, follow the instructions provided by the
manufacturer of the electrodes. The current used depends on the position
of the welding and the joint type and increases according to the thickness
and dimensions of the part.
Table 5
Thickness of welded material (mm)
Diameter of the Electrode
1.5 - 3
2
3 - 5
2.5
5 - 12
3.25
> 12
4
Table 6: Setting the welding current for the given electrode diameter
Diameter of the Electrode (mm)
Welding Current (A)
1.6
30 - 60
2
40 - 75
2.5
60 - 110
3.25
95 - 140
4
140 - 190
5
190 - 240
6
220 - 330
The approximate indication of the average current used for welding with
ordinary steel electrodes is given by the following formula:
I = 50 x (Øe – 1)
where: I = the intensity of the welding current e = the diameter of the
electrode
Example for an electrode with a diameter of 4 mm:
I = 50 x (4 - 1) = 50 x 3 = 150 A
Correct electrode holding during welding
45°
β
45° +70°
Picture 7
Preparation of basic material:
Table 7 lists the material preparation values. Specify the dimensions as
shown in Figure 8.
a
s
α
d
Picture 8
Table 7
s (mm)
a (mm)
d (mm)
α (°)
0 - 3
0
0
0
3 - 6
0
s/2 (max)
0
3 - 12
0 - 1.5
0 - 2
60
Warning about possible problems and their remedy
The extension cord and welding cables are considered the most common
cause of the problem.
If you have any problems, follow these steps:
• Check the value of the supplied mains voltage.
• Make sure that the power cord is fully connected to the power outlet and
the main power switch.
• Make sure the fuses or the circuit breakers are OK.
If you are using the extension cable, check its length, cross-section and
connection.
Make sure the following parts are not defective:
• Main switch of the grid
• Power socket and main power switch
Routine maintenance and inspection
Check according to EN 60974-4. Always before Use the machine to check the
condition of the welding and supply lines cable. Do not use damaged cables.
Perform a visual check:
• welding cables
• power grid
• welding circuit
• covers
• control and indicator elements
• general status