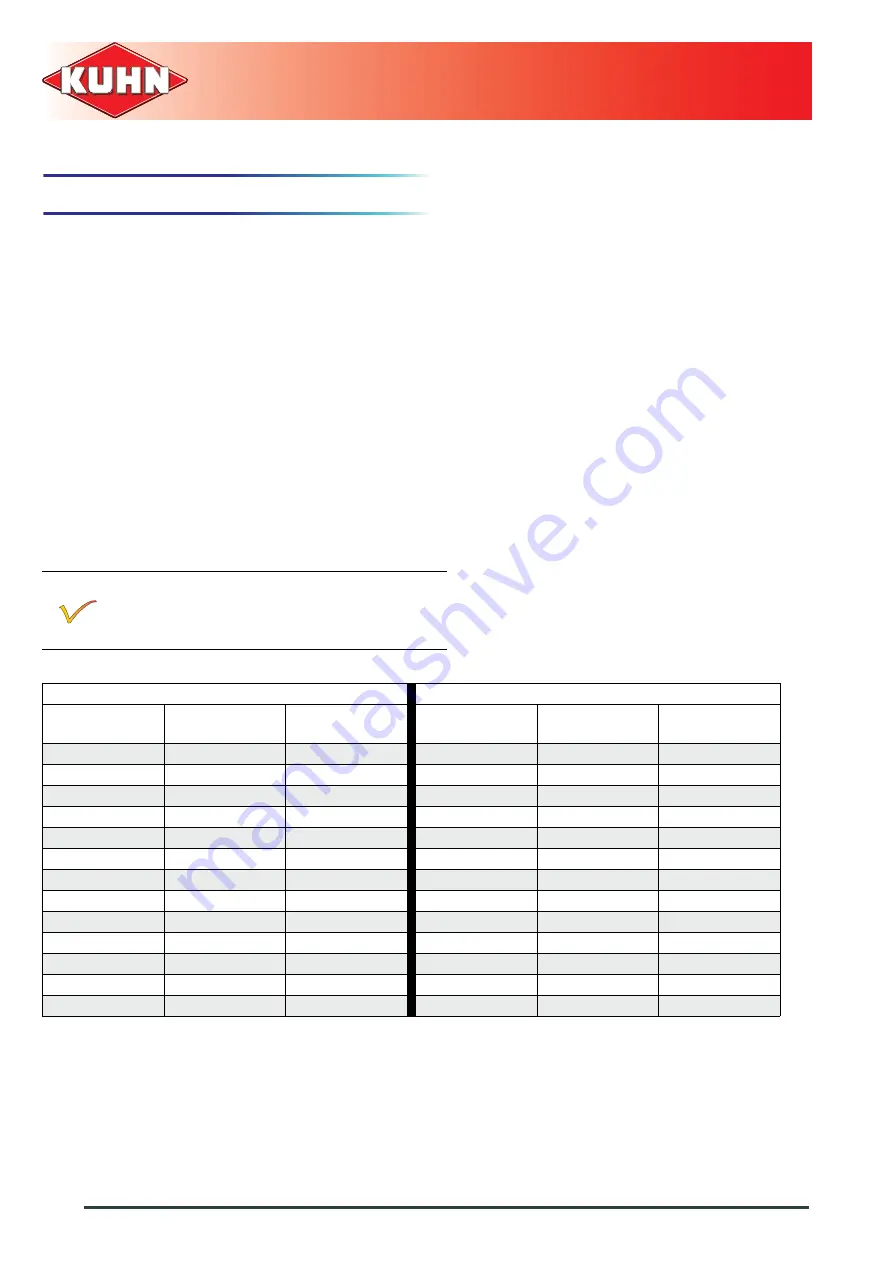
SR600 GII
50
10. - Maintenance and storage
7N037CUS_B
Wheel Rake
10.2 Maintenance
After the first 10 hours of use
- Check tightness of all bolts and nuts on rake
assembly, particularly on rake wheels.
-
Check the center retaining clips on the rake wheels
for tightness and adjust as necessary.
- Check wheel bolts for tightness. Tightening torque:
120 ft lbs (163 daNm).
- Check all hydraulic fittings and re-torque as needed;
using the chart for reference. Be sure to lubricate
any o-ring gaskets.
If welding is required on this unit, do not allow the
electrical current to flow through the bearings.
Ground the welder directly to the part being
welded.
37° TUBE FITTINGS AND ADAPTERS
ADJUSTABLE O-RING PORT FITTINGS
Tube Size
O.D. Thread
Torque - ft lbs
(daNm)
Tube Size
O.D. Thread
Torque - ft lbs
(daNm)
2
5/16
7 (0.9)
2
5/16
7 (0.9)
3
3/8
9 (1.2)
3
3/8
9 (1.2)
4
7/16
12 (1.6)
4
7/16
15 (2.0)
5
1/2
15 (2.0)
5
1/2
19 (2.6)
6
9/16
20 (2.7)
6
9/16
24 (3.3)
8
3/4
39 (5.3)
8
3/4
43 (5.8)
10
7/8
63 (8.5)
10
7/8
48 (6.5)
12
1-1/16
88 (11.9)
12
1-1/16
75 (10.2)
14
1-3/16
103 (13.9)
14
1-3/16
99 (13.4)
16
1-5/16
113 (15.3)
16
1-5/16
123 (16.8)
20
1-5/8
133 (18.0)
20
1-5/8
161 (21.8)
24
1-7/8
167 (22.6)
24
1-7/8
170 (23.0)
32
2-1/2
258 (35.0)
32
2-1/2
240 (27.6)