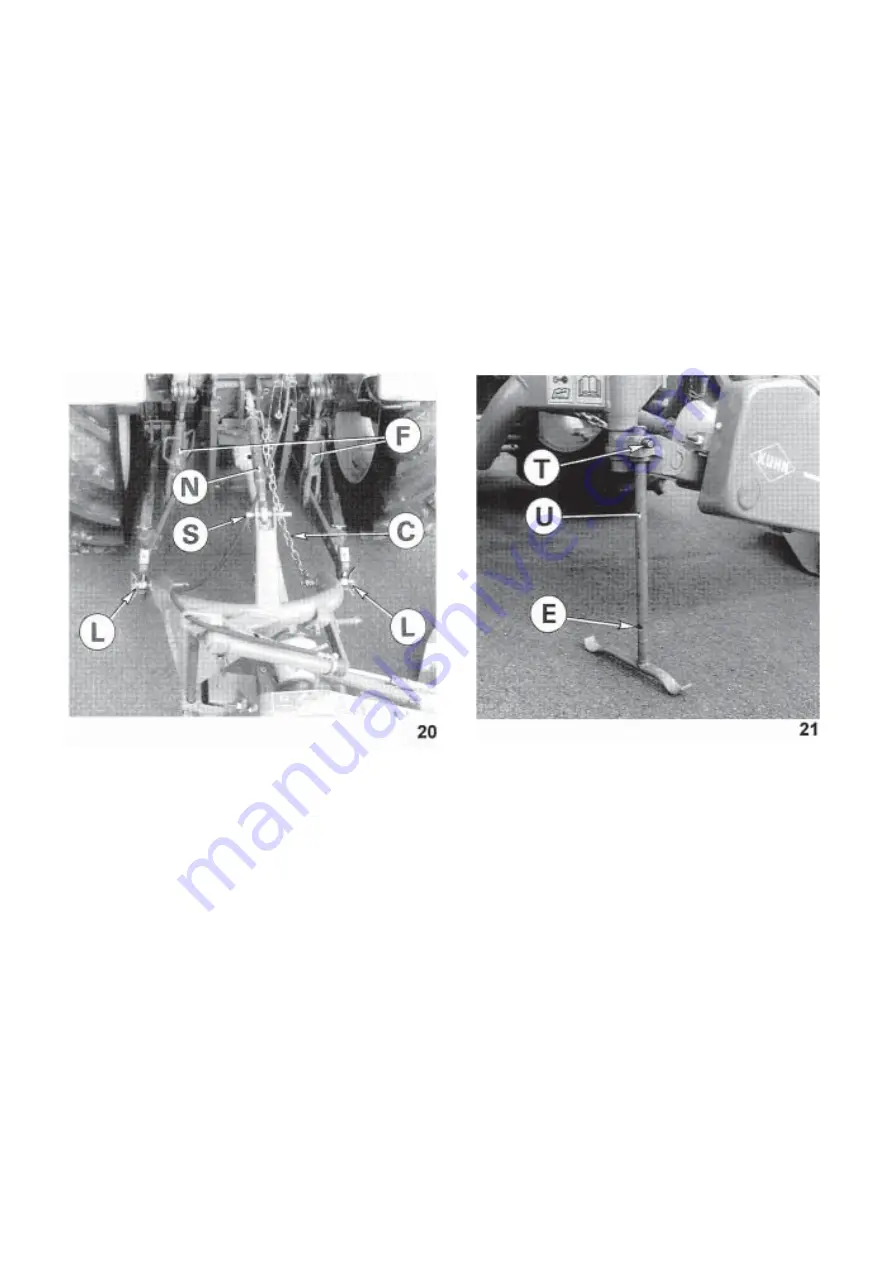
- 19 -
1. Back the tractor to the mower and attach the lower links to the hitch pins. Secure the links with lynch pins
shown at "L" (photo 20).
2. Check that the 2 lift rods (F) are adjusted at the same length.
3. Attach the top link (N) using the pin (S) provided (photo 20). Two positions are available on the pin, depending
on the diameter of the ball joint, to secure the link to the mower.
4. Connect the hydraulic hose to the tractor if the unit is equipped with the hydraulic lift. See optional equipment
for adaptors having different threads.
5. Raise the mower with the tractor hydraulics and depress the pin (T) (photo 21) and raise the parking stand
(U). Lock stand in notch (E) during transport and field operation.
Summary of Contents for GMD 55
Page 1: ...ASSEMBLY OPERATOR S MANUAL GMD 44 55 66 SELECT MULTIDISC MOWER N 95011 A GB 07 98...
Page 12: ...10...
Page 42: ...N O T E S...