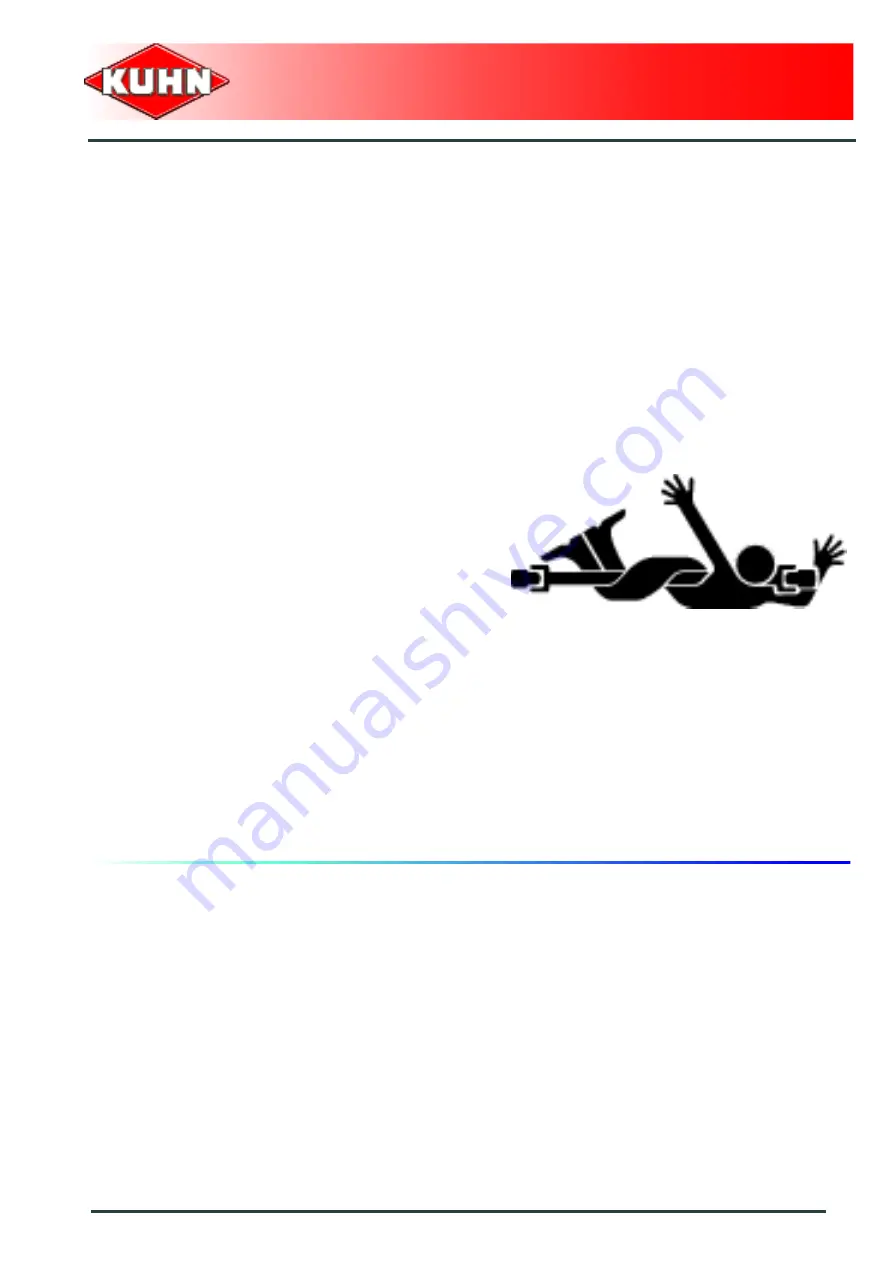
Safety
Gyrotedder
GF17002
11
PTO shaft
Use only PTO shafts supplied with the machine or
recommended by the manufacturer.
The protective shield of the tractor PTO stub, the PTO
shaft guards and the protective covering of the machine
input shaft must always be in place and in good
condition.
Make sure that the PTO shaft guards are secured with
the safety chains provided.
Any worn or damaged guards must be replaced
immediately.A worn guard or an unprotected PTO shaft
can cause a serious or even a lethal accident.
Do not wear loose clothing that could be caught in the
rotating PTO shaft.
Before attaching or removing a PTO shaft, or before
doing any work on the machine, disengage the PTO
drive, turn off the engine, remove ignition key and wait
for all moving parts have come to a complete stop.
If the primary PTO shaft is equipped with a slip clutch or
a free wheel, these must be fitted on the machine side.
Ensure that the PTO shaft is always correctly fitted and
locked into place.
Before connecting the PTO shaft, ensure that the PTO
speed (rotational frequency) and directions of rotation
are in line with manufacturer's recommendations.
Before engaging the PTO drive, make sure all people
and animals are clear from the machine. Never engage
the PTO drive when the tractor engine is stopped.
When uncoupling the machine, rest the PTO shaft on the
support specially provided, and replace protective cover
on the PTO stub of the tractor.
Read and follow the instructions in the operator's manual
provided with the PTO shaft.
Summary of Contents for GF13002
Page 1: ...KN072CGB B OPERATOR S MANUAL Gyrotedder GF17002 KN072CGB B English 12 2009...
Page 2: ......
Page 59: ...Maintenance and storage Gyrotedder GF17002 57 The DIGIDRIVE coupling fingers...
Page 66: ...Gyrotedder 64 GF17002 Limited warranty Limited warranty...
Page 67: ...Limited warranty Gyrotedder GF17002 65...
Page 68: ......
Page 69: ......
Page 70: ......
Page 71: ......
Page 72: ......