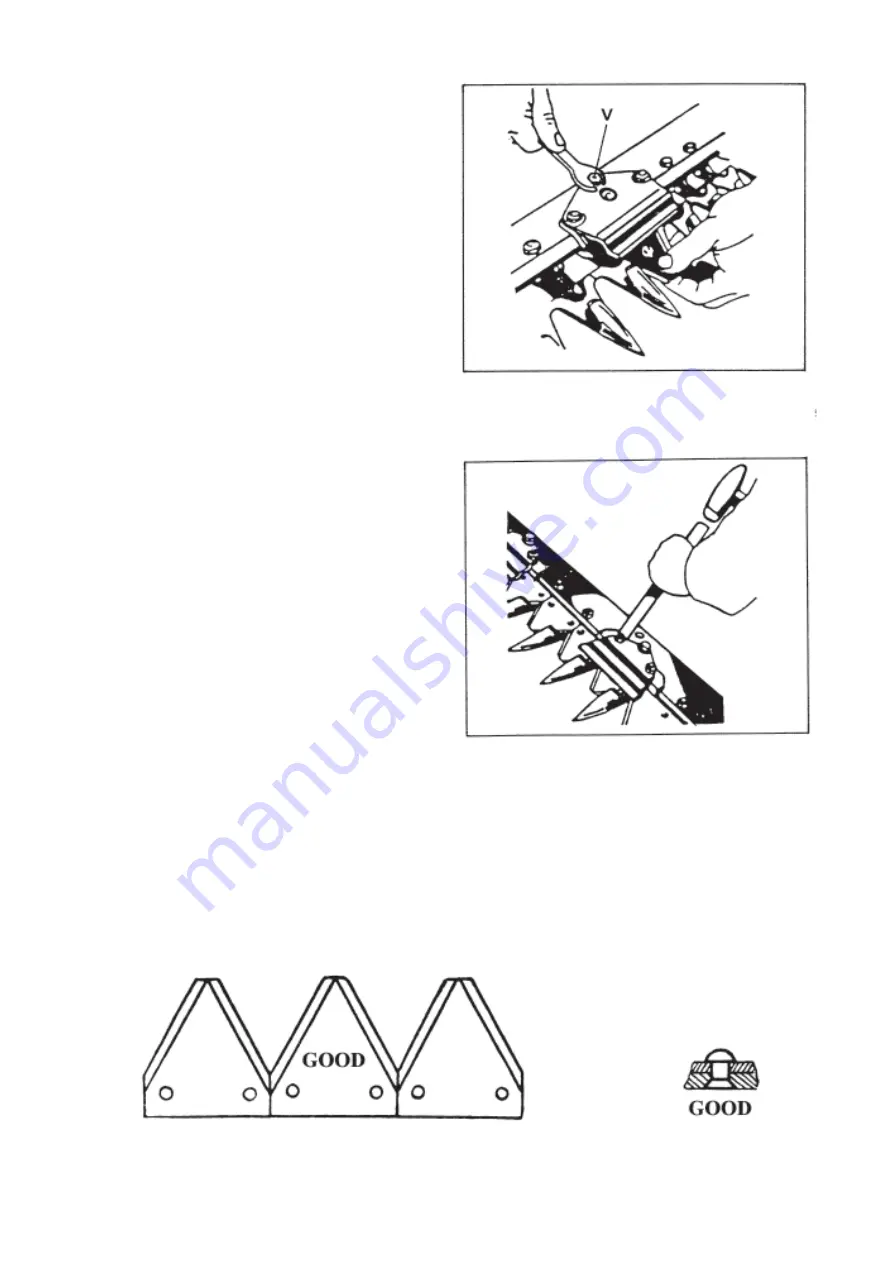
- 18 -
3) KNIFE CLIPS (3) must be correctly fitted over the
top of the raised section. Ensure they are not set at the
back or at the front only, for that would increase the
wear. Screw (V) can be adjusted to lower the knife
clip and give good support to the knife on the surface
of the finger (1). Carefully regulate screw (V) :
- to set all knive clips evenly,
- to avoid clamping the knife.
4) WINGS (4) guide the side of the knife and must contact each other without slack. They are used to line up the fingers
on their top side and back edge.
5) WEAR PLATES (6) under the knife clips have ob-
long holes to adjust the side play on the blade. It is
advisable to set the play between the knife back and
the wear plates between 1 and 1.5 mm and to set all
the wear plates at the same level.
6) KNIFE HEAD GUIDE : Excessive play is counteracted by removing shims located underneath the knife head guide.
7) THE KNIFE must always have well sharpened sections with an angle as near as possible to the original one. An angle
smaller than 20° gives a better cut, but makes the sections more easily jagged. An angle larger than 25° gives a bad cut.
The sections have been tempered to a width of 10 mm from the edge, so they should not be ground beyond this width
as the bevelling would not hold. When replacing a section, do not crush the rivets, for should they get compressed on
their whole length, they might distort or burst the edge. Ensure the knife is always straight and the sections well in line
with each other.
When replacing sections, study illustrations below :
When sharpening blades, always maintain the original angle.
Never rivet a section while the blade is in the cutterbar.
Summary of Contents for FA 392
Page 1: ...ASSEMBLY OPERATOR S MANUAL FA 392 REAR MOUNTED MOWER N 95007 A GB 12 95...
Page 11: ...9...
Page 12: ...10...
Page 13: ...11...
Page 26: ...N O T E S...