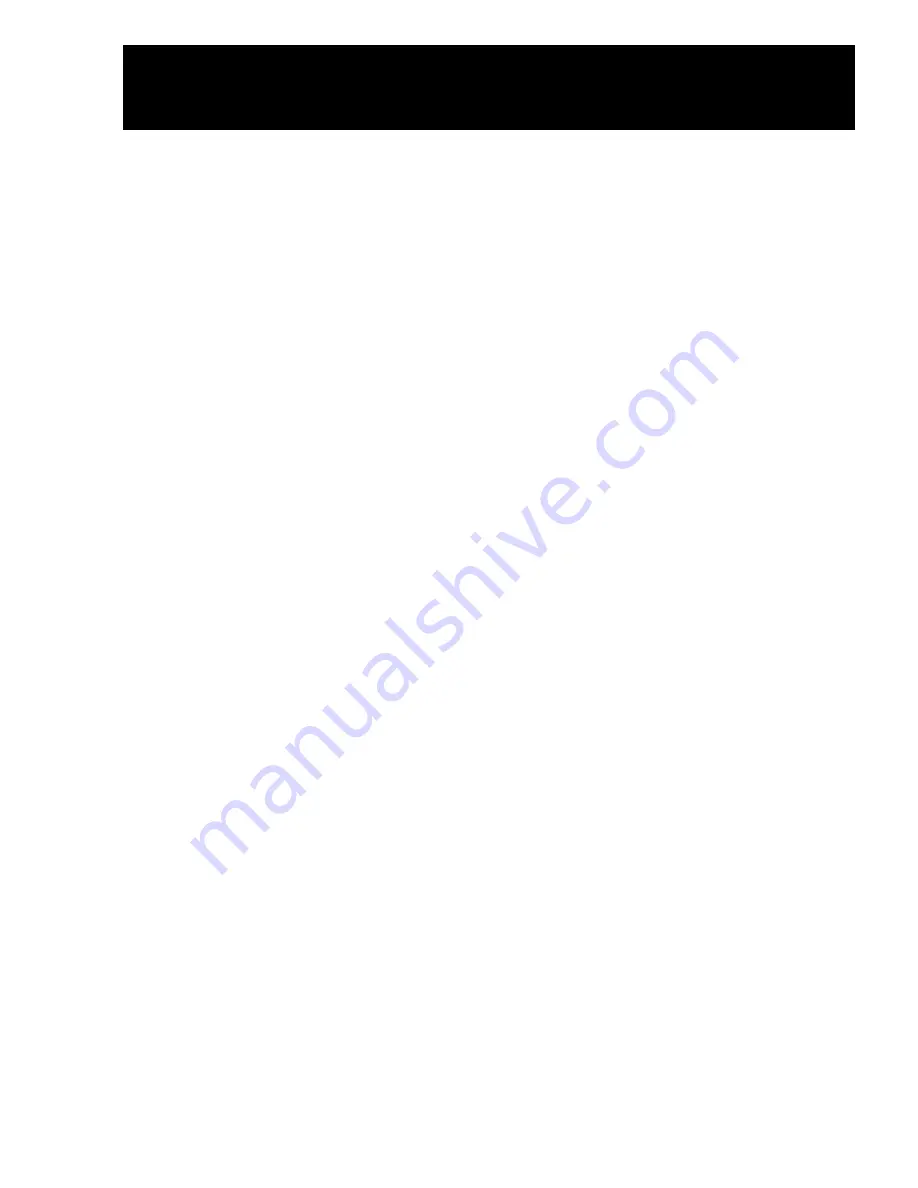
CONTENTS
MECHANISM
1. HYDRAULIC CIRCUIT .................................................................................. 7-M1
2. HYDRAULIC PUMP ...................................................................................... 7-M2
3. FLOW PRIORITY VALVE ............................................................................ 7-M3
4. RELIEF VALVE ............................................................................................. 7-M4
5. IMPLEMENT CONTROL VALVE ................................................................. 7-M5
6. FEEDBACK LINKAGE .................................................................................. 7-M6
7. HYDRAULIC CYLINDER .............................................................................. 7-M7
KiSC issued 04, 2006 A
Summary of Contents for WSM F2880
Page 1: ...WORKSHOP MANUAL F2880 F3680 RCK72 F36 RCK72R F36 RCK60 F36 RCK60R F36 KiSC issued 04 2006 A ...
Page 12: ...G GENERAL KiSC issued 04 2006 A ...
Page 58: ...1 ENGINE KiSC issued 04 2006 A ...
Page 120: ...2 TRANSMISSION KiSC issued 04 2006 A ...
Page 176: ...3 FRONT AXLE KiSC issued 04 2006 A ...
Page 177: ...CONTENTS MECHANISM 1 STRUCTURE 3 M1 KiSC issued 04 2006 A ...
Page 184: ...4 BRAKES KiSC issued 04 2006 A ...
Page 185: ...CONTENTS MECHANISM 1 FEATURES 4 M1 2 OPERATION 4 M2 KiSC issued 04 2006 A ...
Page 198: ...5 REAR AXLE KiSC issued 04 2006 A ...
Page 199: ...CONTENTS MECHANISM 1 STRUCTURE 5 M1 KiSC issued 04 2006 A ...
Page 217: ...6 STEERING KiSC issued 04 2006 A ...
Page 218: ...CONTENTS MECHANISM 1 STRUCTURE 6 M1 2 STEERING CONTROLLER 6 M2 KiSC issued 04 2006 A ...
Page 230: ...7 HYDRAULIC SYSTEM KiSC issued 04 2006 A ...
Page 252: ...8 ELECTRICAL SYSTEM KiSC issued 04 2006 A ...
Page 284: ...9 MOWER KiSC issued 04 2006 A ...
Page 290: ...CONTENTS MECHANISM 1 POWER TRANSMISSION 9 M1 KiSC issued 04 2006 A ...