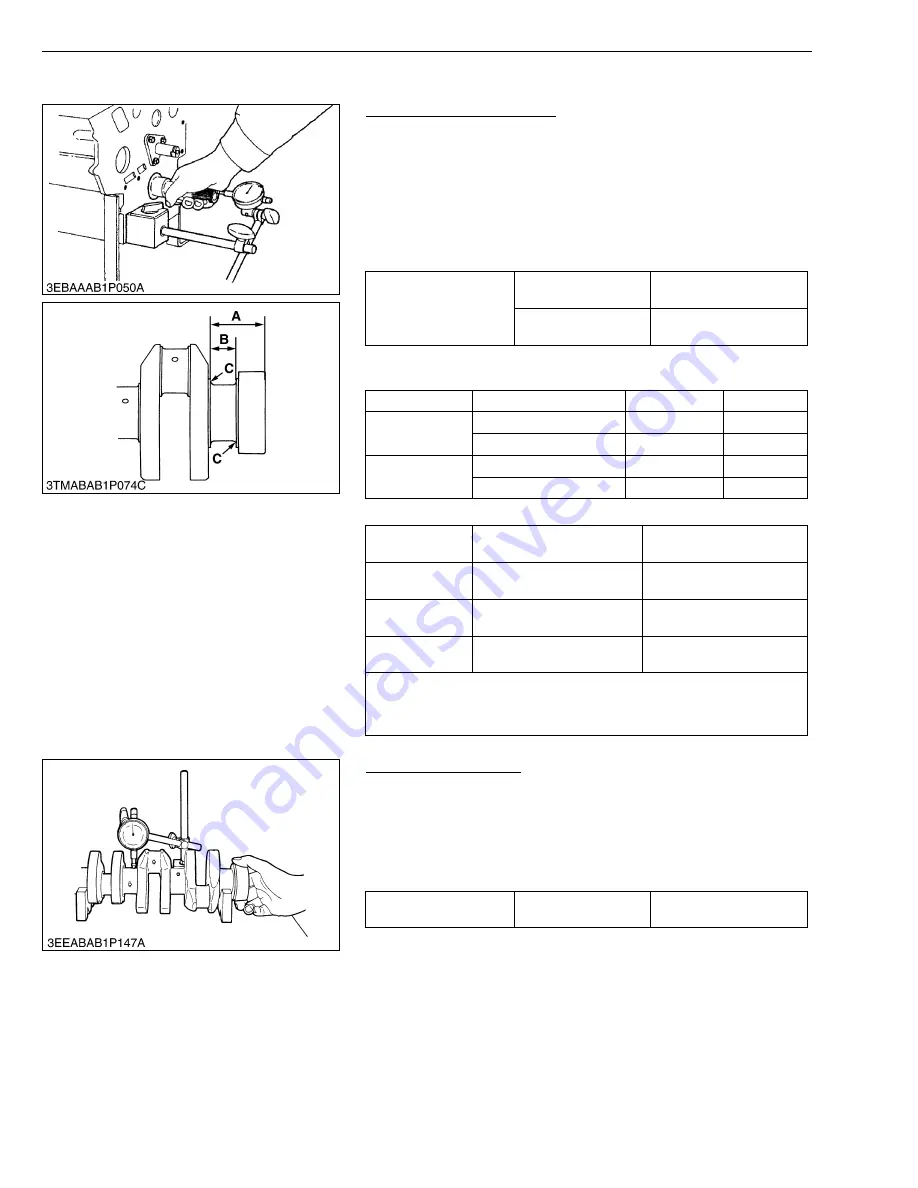
S-60
WG972-E2, DF972-E2, WSM
GASOLINE / LPG ENGINE
(4) Crankshaft
Crankshaft Side Clearance
1. Set a dial indicator with its tip on the end of the crankshaft.
2. Measure the side clearance by moving the crankshaft to the front
and rear.
3. If the measurement exceeds the allowable limit, replace the
thrust bearings.
4. If the same size bearing is useless because of the crankshaft
journal wear, replace it with an oversize one referring to the table
and figure.
(Reference)
• Oversize thrust bearing
• Oversize dimensions of crankshaft journal
W1066738
Crankshaft Alignment
1. Support the crankshaft with V blocks on the surface plate at both
end journals.
2. Set a dial indicator with its tip on the intermediate journal.
3. Measure the crankshaft alignment.
4. If the measurement exceeds the allowable limit, replace the
crankshaft.
W1067285
Crankshaft side
clearance
Factory spec.
0.15 to 0.31 mm
0.0059 to 0.0122 in.
Allowable limit
0.50 mm
0.0197 in.
Oversize
Bearing
Code Number
Marking
0.2 mm
0.008 in.
Thrust bearing 1 02
15261-23950
020 OS
Thrust bearing 2 02
15261-23970
020 OS
0.4 mm
0.016 in.
Thrust bearing 1 04
15261-23960
040 OS
Thrust bearing 2 04
15261-23980
040 OS
Oversize
0.2 mm
0.008 in.
0.4 mm
0.016 in.
Dimension
A
46.1 to 46.3 mm
1.815 to 1.823 in.
46.3 to 46.5 mm
1.823 to 1.831 in.
Dimension
B
23.40 to 23.45 mm
0.9134 to 0.9154 in.
23.80 to 23.85 mm
0.9213 to 0.9232 in.
Dimension
C
1.8 to 2.2 mm radius
0.071 to 0.087 in. radius
1.8 to 2.2 mm radius
0.071 to 0.087 in. radius
(0.8S)
The crankshaft journal must be fine-finished to higher than
∇∇∇∇
.
*Holes to be de-burred and edges rounded with 1.0 to 1.5 mm
(0.0394 to 0.0591 in.) relief.
Crankshaft alignment
Allowable limit
0.02 mm
0.0008 in.
KiSC issued 01, 2006 A