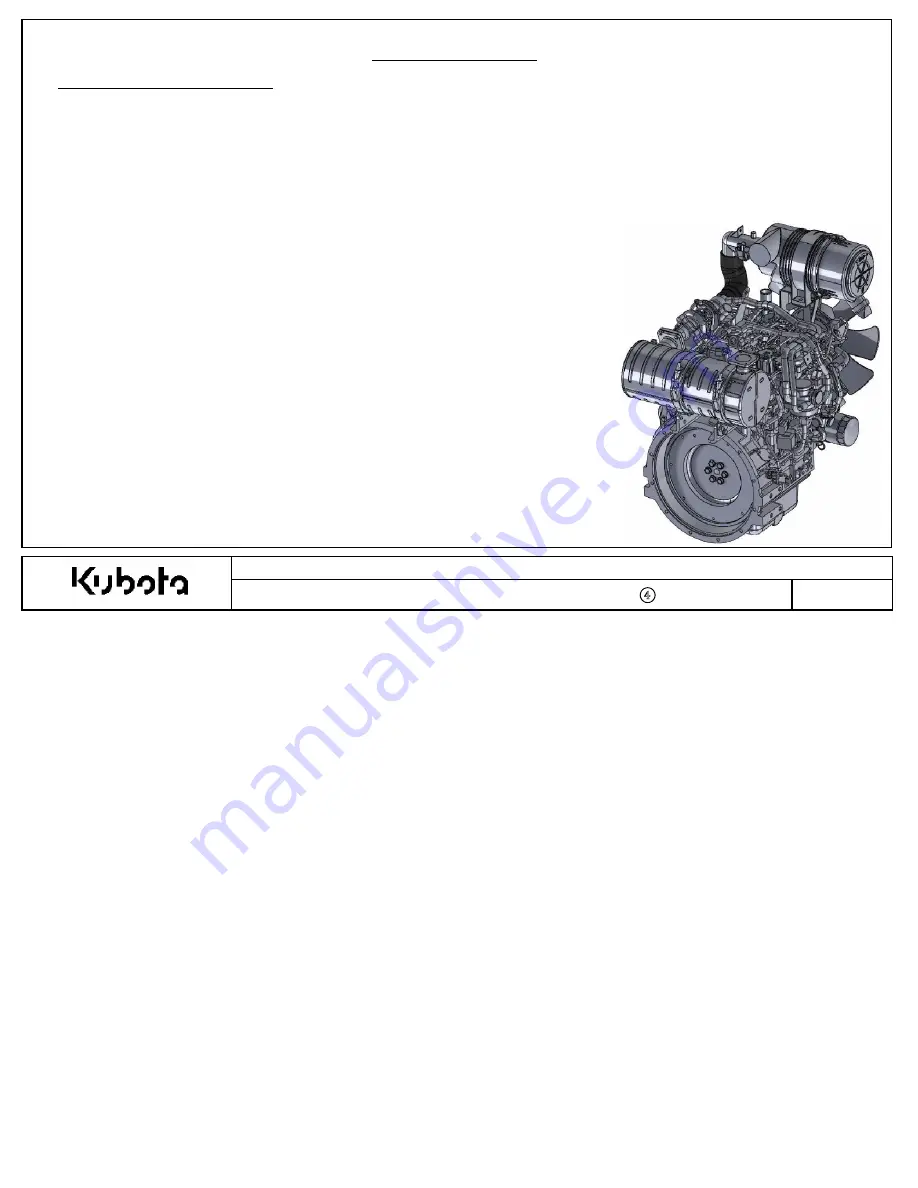
Page No. 34
Kubota Emission-Related Installation Instructions
Document Number : KEA-STD-03-CRS-DOC-001-
④
Appendix 5
2-6 Intake System Installation
1. Air cleaner vibration:
- Acceleration/Displacement must not exceed the limits prescribed in the application review form.
- Vibration must be checked during the application review.
2. Air intake temperature should be checked during the application review:
- The air inlet temperature should not be more than 5 deg. C higher than ambient temperature, otherwise engine
performance will be reduced.
- If the temperature is high a pre-cleaner hose can be added to the air cleaner to
help reduce inlet temperature.
3. Environment:
- It is critical that water does not enter the intake system.
- Add a pre-cleaner hose and/or rain cap as necessary.
-The dust evacuation valve must point downward to prevent water from entering
the air cleaner.
4. Pre-Cleaner Hose Requirements:
- FEA supplied pre-cleaner hose:
- Thickness ≥ 6 mm (for rubber molded hoses)
- The inner surface of the pipe should be smooth.
5. Air Cleaner Bracket:
- The OEM is responsible to prepare the air cleaner mounting bracket if the
air cleaner is moved from the standard position (intake system flexibility).
2. Intake System