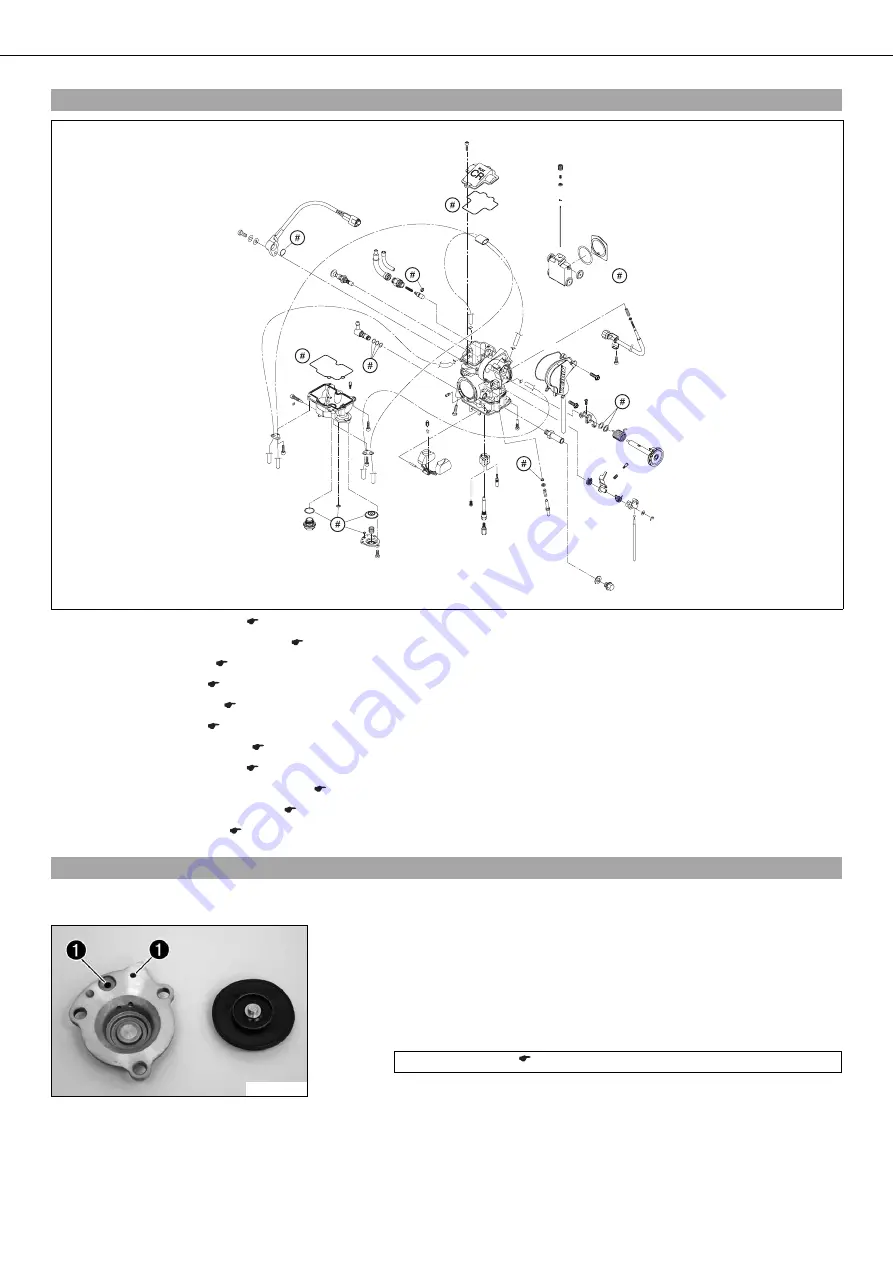
31/CARBURETOR
170
21.9
Checking/adjusting the carburetor components
301703-01
–
Disassemble the carburetor. (
–
Check/adjust the accelerator pump. (
–
Check the choke slide. (
–
Check the jet needle. (
–
Check the throttle slide. (
–
Check the needle jet. (
–
Check the float needle valve. (
–
Check/adjust the float level. (
–
Check/adjust the throttle slide opening. (
–
Check the throttle position sensor. (
–
Assemble the carburetor. (
21.10
Checking/adjusting the accelerator pump
Condition
The carburetor and accelerator pump have been removed.
700051-10
–
Check the membrane of damage or brittleness.
» If the membrane is damaged or brittle:
–
Change the membrane.
–
Check holes
to ensure that they are free.
» If the holes are not free:
–
Clean the holes.
Carburetor cleaner (
PartShark.com
877-999-5686