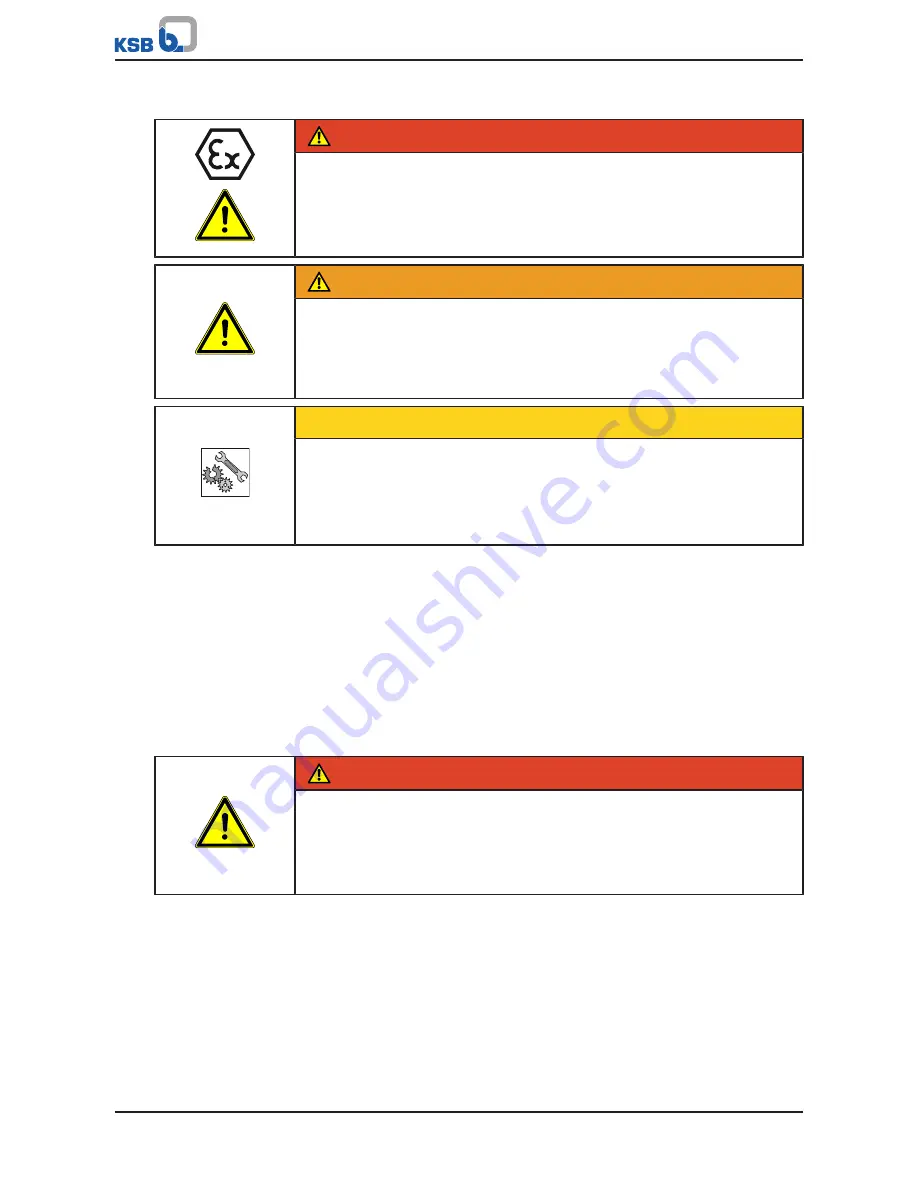
5 Installation at Site
26 of 60
Sewabloc
5.8 Checking the direction of rotation
DANGER
Temperature increases resulting from contact between rotating and stationary
components
Explosion hazard!
Damage to the pump set!
▷
Never check the direction of rotation by starting up the unfilled pump.
WARNING
Hands inside the pump casing
Risk of injuries, damage to the pump!
▷
Always disconnect the pump set from the power supply and secure it against
unintentional start-up before inserting your hands or other objects into the
pump.
CAUTION
Drive and pump running in the wrong direction of rotation
Damage to the pump!
▷
Refer to the arrow indicating the direction of rotation on the pump.
▷
Check the direction of rotation. If required, check the electrical connection and
correct the direction of rotation.
The correct direction of rotation of motor and pump is in clock-wise direction (seen
from the motor end).
1. Start the pump set and stop it again immediately to determine the motor's
direction of rotation.
2. Check the direction of rotation.
The motor's direction of rotation must match the arrow indicating the direction
of rotation on the pump.
3. If the pump runs in the wrong direction of rotation, check the connection of the
motor and switchgear, if any.
5.9 Priming and venting the pump
DANGER
Shaft seal failure caused by insufficient lubrication
Hot or toxic fluid could escape!
Damage to the pump!
▷
Before starting up the pump set, vent the pump and suction line and prime
both with the fluid to be handled.
1. Vent the pump and suction line and prime both with the fluid to be handled.
2. Fully open the shut-off valve in the suction line.
3. Fully open all auxiliary connections (barrier fluid, flushing liquid, etc).
Summary of Contents for Sewabloc Series
Page 59: ......