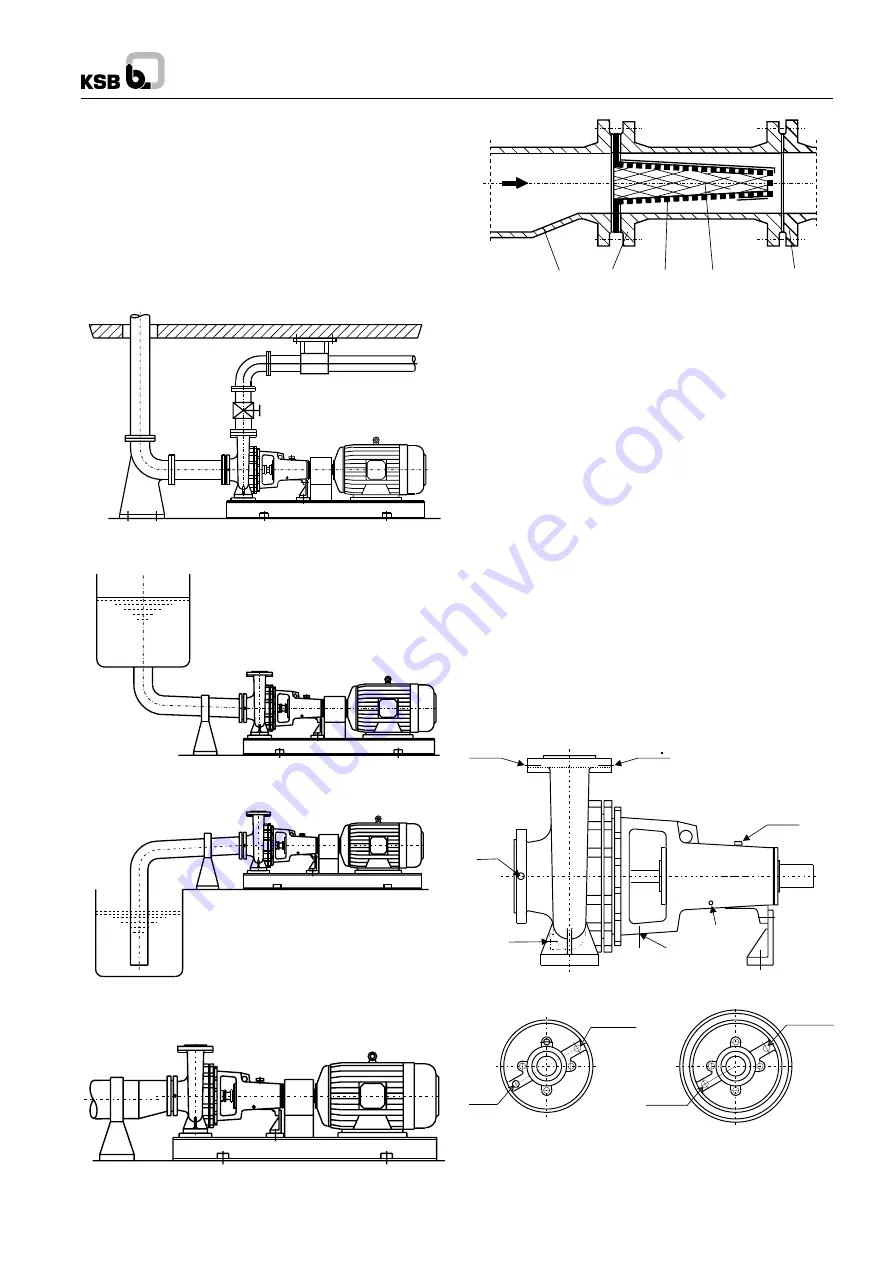
MEGACHEM
1
2
3
4
5
8D
1M2
7S
6D
3M
13D
13E
1M1
7E
Outlet
Inlet
10S
Outlet
10E
Inlet
2
on to the pump. The nominal sizes of the pipelines should be
at least equal to the nominal sizes of the pump nozzles (fig.5a,
5d).
We recommend the incorporation of check valves or non-return
valves and isolating valves in the system, depending on the
type of installation and pump.
Any thermal expansion of the type of piping (due to high
temperatures) must be compensated by suitable means, so
as not to impose any additional load on the pump.
Fig. no. 5a : Piping & supporting of piping
Fig. no. 5b : Suction pit above the pump
Fig. no. 5c: Suction pit below the pump
Fig. no. 5d : Suction pipe connections
1 Suction line
4 Coarse strainer
2 Strainer holder
5 Pump nozzle
3 Fine strainer
Fig. no. 6 : Conical strainer for suction line
Before commissioning a new installation, thoroughly clean,
flush and blow through all vessels, piping & connections.
Welding beads, scale and other impurities frequently only
become dislodged after a certain period of time; it is necessary
to fit a strainer in the suction line to prevent these entering the
pump. The total cross section of the holes in the strainer should
be three times the cross section of the piping in order to avoid
excessive pressure loss across the strainer due to clogging.
The conical strainer consists of a coarse strainer fronted by a
fine strainer with a 2.0 mm mesh and 0.5 mm diameter wire,
made of corrosion resistant material, (i.e. Stainless Steel).
Attention : For recommended suction & discharge pipe
sizes, refer to performance curves.
2.4.1 Auxiliary connections
The size and location of all auxiliary connections for suction /
discharge pressure gauge, cooling and leakage liquid are
shown in the fig. No. 7 & table no.1
Fig. no.7 : Auxiliary connections of pump