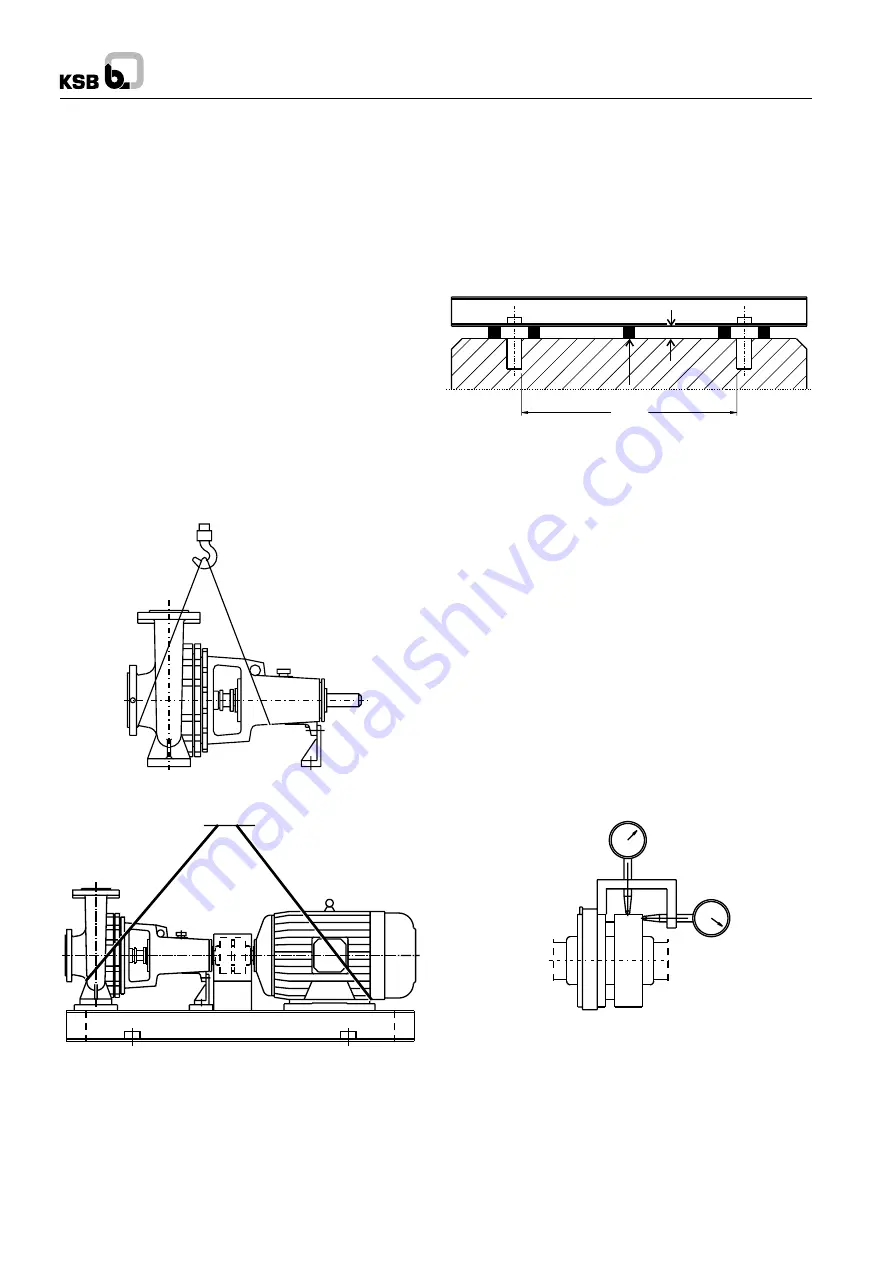
MEGACHEM
>800
min. 50 mm
1
1
General
Your centrifugal pumps will only give you completely
trouble free and satisfactory service on condition that it is
installed with due care and properly maintained. It is
absolutely essential that the instructions contained in this
manual be strictly observed and that the pumps are not
operated under conditions which differ from those specified
under our 'Operating Conditions' This operating instruction
manual does not take any account of any safety regulations
which may apply to the installation site, and the site engineer
& the site operator is responsible for notifying our erection
staff of any such regulations and seeing that they are complied
with.
The type series, pump sizes, main operating data and the
works order number are all stamped on the name plate affixed
to the pump. Please make sure to quote this information every
time you write to us in respect of queries, repeat orders and
more particularly when ordering spare parts.
1.1
Handling
When handling the complete pumpset or bare pump attach
ropes to the pump and motor as shown (not through the motor
eyebolt).
Fig. no.1 : Bare Pump
Fig no.2 : Pump & motor on a common baseframe
2
Installation (on site)
2.1
Foundation
Make sure the concrete foundation has set before mounting
the pumpset. The surface of the foundation must be completely
horizontal and perfectly flat.
2.2
Mounting
Position the pumpset on the foundation and align using a
precision spirit level on the discharge nozzle. Ensure that
the gap between the two coupling halves is as given on the
general arrangement drawing. Always fit shims to the left and
right of the anchor bolts, between the baseplate / foundation
frame and the foundation. If the shims are more than 800 mm
apart, position extra shims equidistant between them. All shims
must seat perfectly flush with the baseplate/frame.
Fig no.3 : Fitting shims
Uniformly tighten up securing means. Baseplate have to be
grouted with non-shrinking mortar up to the upper edge of the
frame after having been fixed in position.
2.3
Aligning pump / motor
After the baseplate has been fixed in position carefully check
the coupling and, if necessary, realign the pumpset (on the
motor). Prior to checking the alignment and / or aligning,
loosen supporting foot (183) and tighten again without
transmitting any strain. The coupling must also be checked
and the pumpset realigned even if the pump and motor are
supplied ready mounted on a common baseplate.
The pumpset to be aligned radially and axially within 0.04 mm
by installing dial indicators and without pipe connection. The
gap between the two coupling halves must be the same at all
points (minimum 3 points) on the circumference; this can be
measured using calipers or a filler gauge.
The alignment should be carried with & without pipe
connections and should be within limits. For liquids handling
more than 105
0
C
cold alignment & hot alignment should be
carried out on pumpset.
Fig. no. 4 : Aligning a coupling
2.4
Connecting the piping
Never use the pump itself as an anchorage for the piping.
Suction lift lines should be laid with a rising slope towards the
pump and suction head line with a downward slope towards
the pump (fig. 5b, 5c)
The pipelines should be anchored in close proximity to the
pump and should be connected to the latter without transmitting
any stress or strain, nor should weight of the piping be loaded