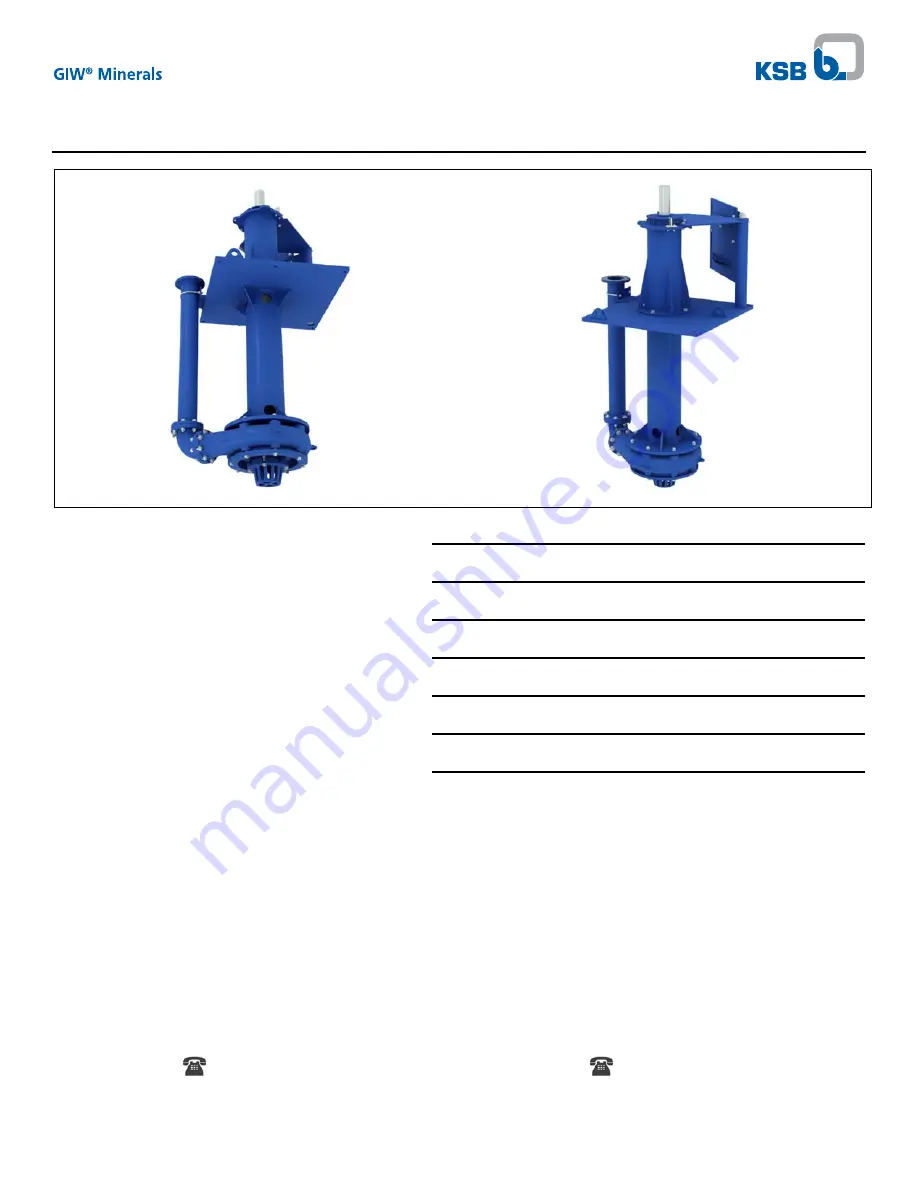
Installation/Operating Manual
2017.01
LCV
[en-US]
Pump Type:
Pump Serial Number:
Date:
Purchaser:
Purchaser’s Order Number:
GIW / KSB Work Order Number:
Shipped To:
Include the pump’s serial number when ordering replacement parts
This is a standard maintenance manual provided for your convenience
This manual may include additional documentation not applicable to your specific pump
GIW INDUSTRIES, INC.
5000 Wrightsboro Road
Grovetown, GA 30813 USA
+1 (888) 832-4449
FAX +1 (706) 855-5151
www.giwindustries.com
KSB AG
Johann-Klein-Str. 9
D-67227 Frankenthal, Germany
+49 6233 86-0 .
FAX +49 6233 86-3289
www.ksb.com
Summary of Contents for LCV
Page 40: ...LCV en US 40 14 Notes ...