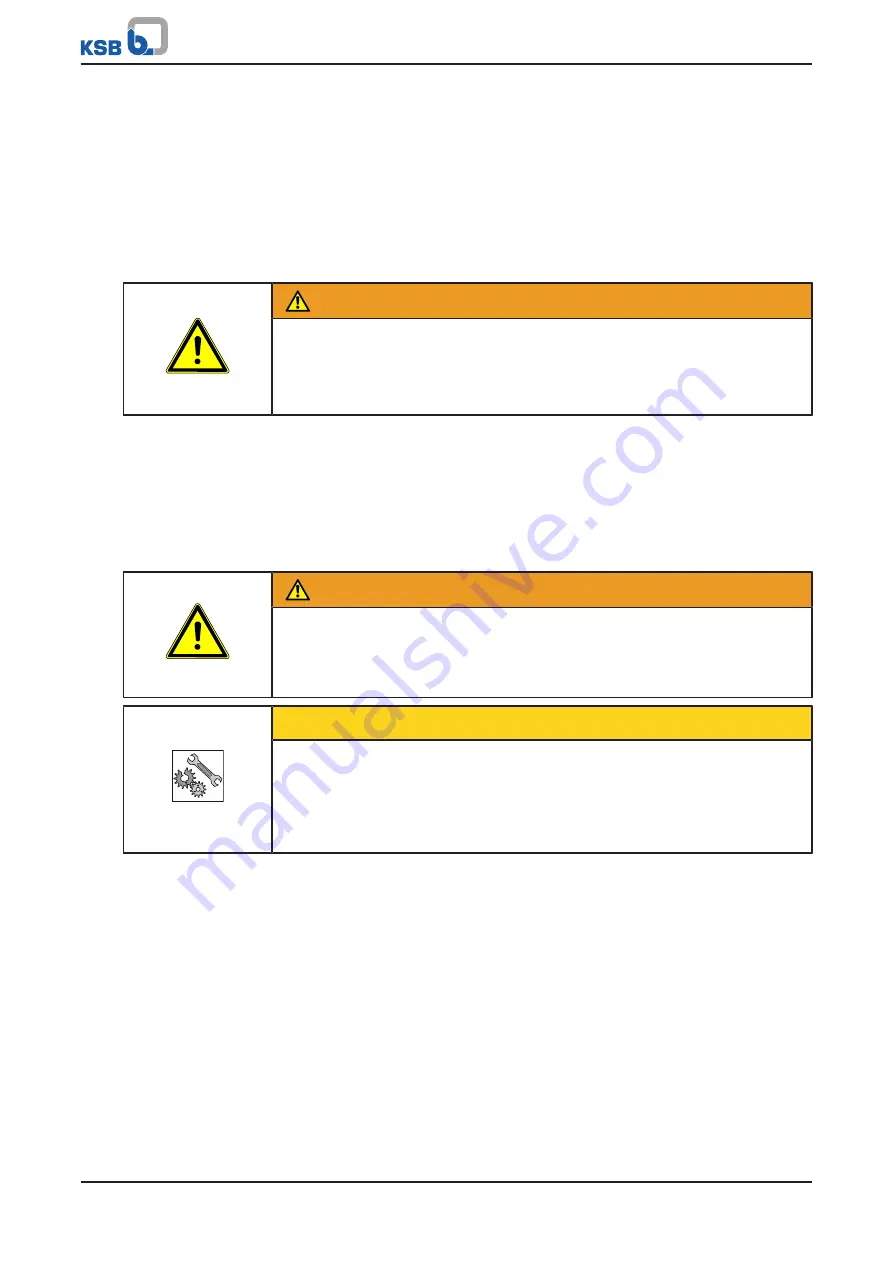
7 Servicing/Maintenance
59 of 80
HPK
1121.8/06-EN
8. Carefully drive shaft 210 together with angular contact ball bearing 320.02 and
the inner race of cylindrical roller bearing 322.01 out of the bearing bracket
towards the drive end.
9. Remove support disc 550.23 of angular contact ball bearing 320.02 from bearing
bracket 330.
10. Remove cylindrical roller bearing 322.01 (roller cage) from bearing bracket 330.
11. Bend open lock washer 931.01 behind slotted round nut 920.21 on shaft 210.
12. Unscrew slotted round nut 920.21 (right-hand thread) and remove lock washer
931.01.
WARNING
Hot surfaces due to heating of components for assembly/dismantling
Risk of burns!
▷
Wear heat-resistant protective gloves.
▷
Remove flammable substances from the danger zone.
13. Heat up angular contact ball bearing 320.02 and the inner ring of cylindrical
roller bearing 322.01 to 80 °C, and pull them off shaft 210.
14. Dispose of joint rings 400.01/.02.
7.5 Reassembling the pump set
7.5.1 General information/Safety regulations
WARNING
Improper lifting/moving of heavy assemblies or components
Personal injury and damage to property!
▷
Use suitable transport devices, lifting equipment and lifting tackle to move
heavy assemblies or components.
CAUTION
Improper reassembly
Damage to the pump!
▷
Reassemble the pump (set) in accordance with the general rules of sound
engineering practice.
▷
Use original spare parts only.
Sequence
Always reassemble the pump in accordance with the corresponding general assembly
drawing.
Sealing elements
▪
Gaskets
– Always use new gaskets, making sure that they have the same thickness as
the old ones.
– Always fit gaskets of asbestos-free materials or graphite without using
lubricants (e.g. copper grease, graphite paste).
▪
O-rings
– Never use O-rings that have been made by cutting an O-ring cord to size and
gluing the ends together.
▪
Packing rings
– Always use pre-compressed packing rings.
Summary of Contents for HPK Series
Page 1: ...Thermal Oil Hot Water Pump HPK Bearing Assemblies P02as to P08s Installation Operating Manual...
Page 78: ......
Page 79: ......