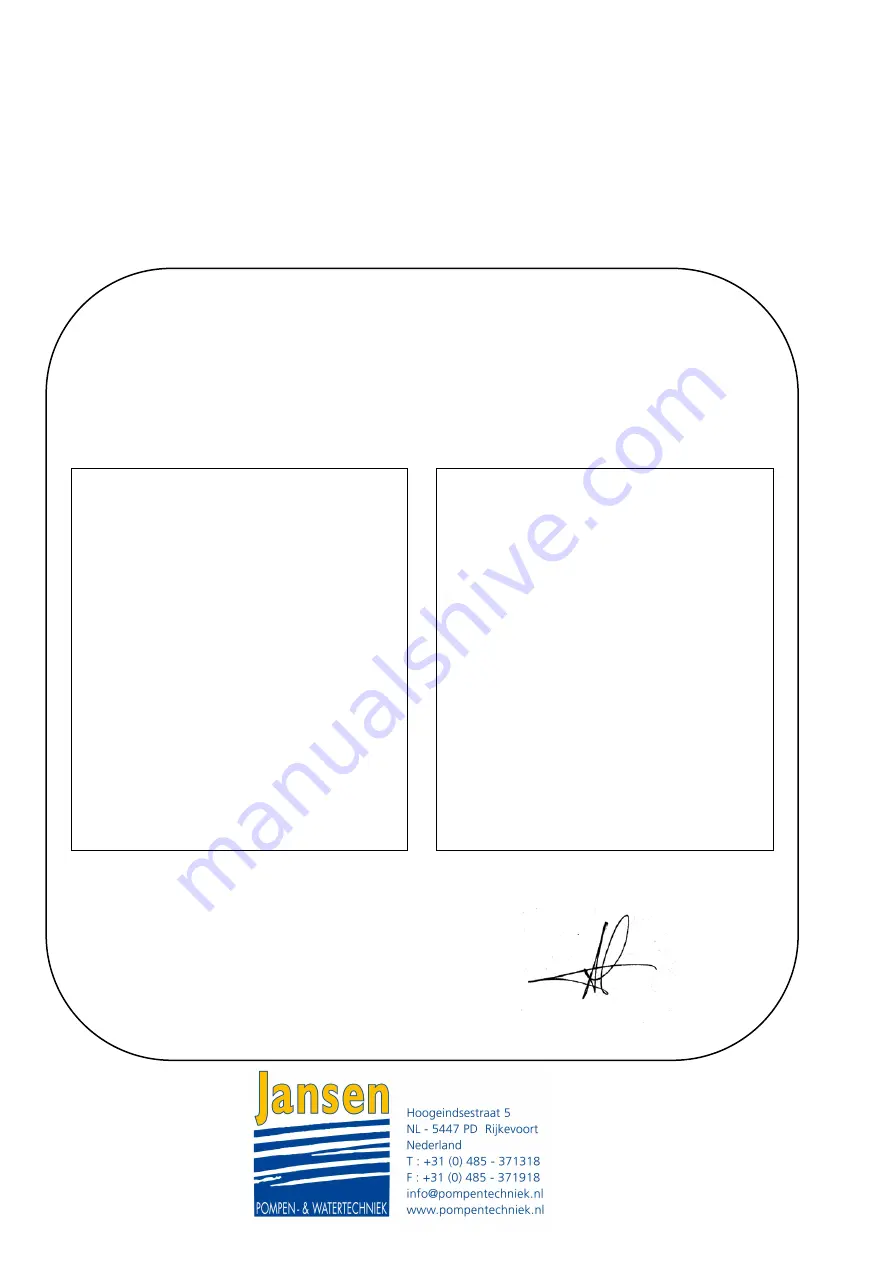
WARRANTY
KSB ITUR Spain, S.A. undertakes:
To repair or replace at any of its ASSOCIATED TECHNICAL SERVICE CENTRES or at its factory in Zarautz, free
of charge and for a period of 12 months as of the date of dispatch from our warehouses, any product which shows
manufacture defects. This warranty will be reduced to 6 months for continuous or permanent service pumps.
KSB ITUR Spain, S.A. shall not be liable for any direct or indirect damage which the product suffers as a result of
defective installation, lack of maintenance, negligent handling, handling by unauthorised personnel, overloading or
deficient functions.
The responsibility of KSB ITUR Spain, S.A. is limited in all cases to the replacement, as speedily as possible, of the
defective part, without it being in any way liable for other responsibilities or compensation.
CERTIFICATE OF COMPLIANCE WITH
EC MACHINERY DIRECTIVE
KSB ITUR
P.O. Box 41 – 20800 ZARAUTZ (Gipuzkoa) Spain
PRODUCT UNDER CERTIFICATION. PUMPS SERIES: IPR, IPRT
EC DECLARATION OF
CONFORMITY
KSB ITUR hereby declares, under its
responsibility, that its aforementioned
products (when supplied with a motor), to
which this Declaration refers, are in line
with European Directive 98/37/EC on the
approximation laws of the Member States
on machinery.
Applied harmonised standards:
EN 292 Part 1, EN 292 Part 2 and EN 809
MANUFACTURER'S
DECLARATION
KSB ITUR hereby declares that its
aforementioned products (when supplied
without a motor) are proposed for
incorporation in machinery or assembled
with other machines to form machinery
covered by Directive 98/37/EC.
Warning is hereby given that the
aforementioned products cannot be started
up until the machinery in which they are to
be incorporated has been declared to
conform to the dispositions of the
aforementioned Directive.
Applied harmonised standards:
EN 292 Part 1, EN 292 Part 2 and EN 809
Zarautz, October 2008
Post
Head of Engineering
Name
Ángel
Fernández
Jansen Pompentechniek T: +31(0)485-371318 E: [email protected]