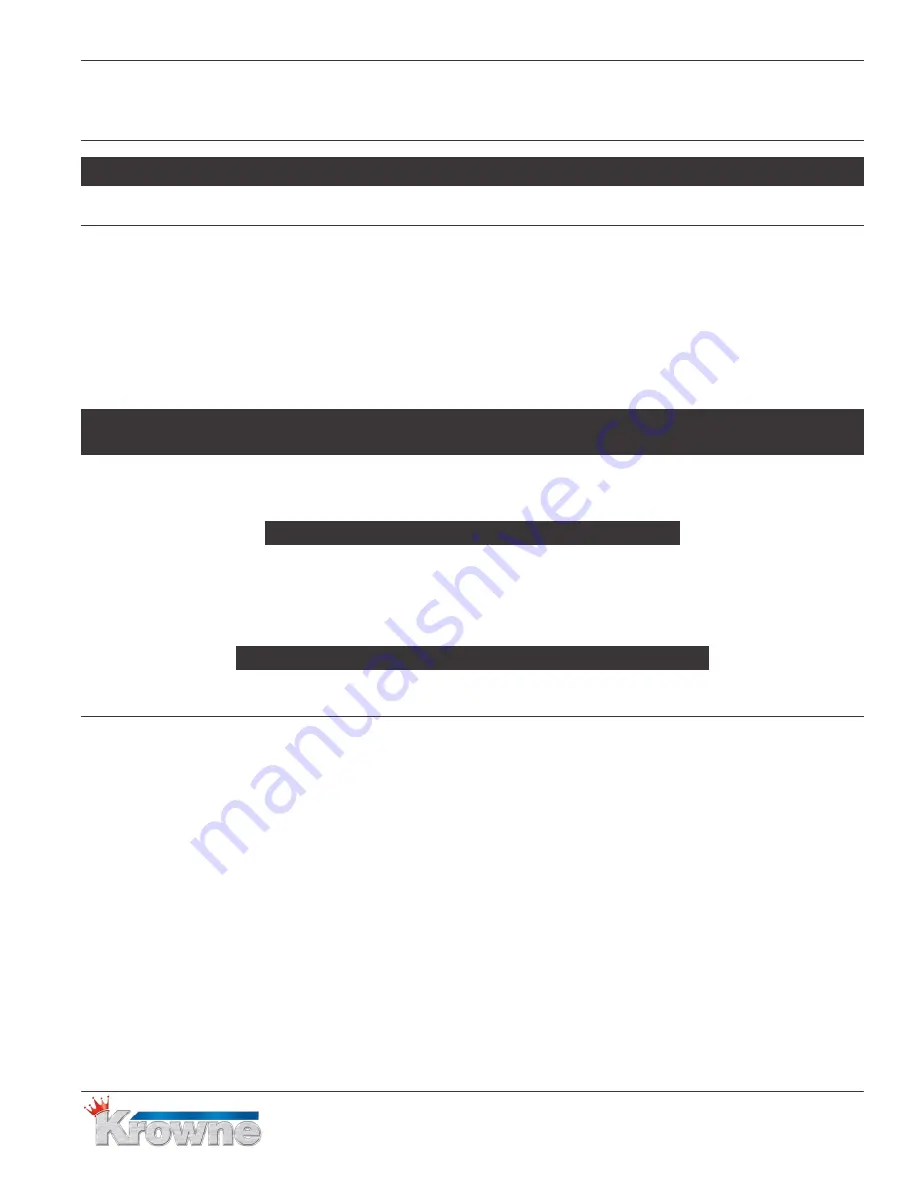
15
Krowne Metal Corporation
|
100 Haul Road
|
Wayne, NJ 07470
Phone: (800) 631-0442
|
Fax: (973) 872-1129
|
www.krowne.com
Daily Cleaning or After 8 Hours of Operation:
1.
Make sure that any glasses on the conveyor are clean, then remove them from the conveyor.
2.
Push the On/Off/Flush switch on the right-hand side of the glasswasher control box to the Off position.
3.
Remove the splash curtain from the curtain hooks located at each end of the splash curtain rod.
4.
Remove the (2) stainless steel conveyor guards located at each corner of the glasswasher and the plexiglass stop assembly.
5.
Remove the cylindrical stainless steel conveyor guard located in the center of the glasswasher.
6.
Remove the conveyor by lifting the rear of the conveyor while pulling it forward to disengage the conveyor drive gear located at the right front
corner of the wash chamber.
7.
Take these parts to a sink, and wash in hot soapy water using a soft brush and cloth, then rinse with fresh water and set aside to air dry.
8.
Clean the wash chamber interior with hot soapy water, then rinse with fresh water. Wipe the interior with a soft cloth. Allow the wash chamber
to air dry overnight.
9.
Remove the upper scrap screen, remove large debris in a trash can, take screen to a sink and flush screen with fresh water.
10.
Remove the lower scrap screen, remove large debris in a trash can, take screen to a sink and flush clean with fresh water.
11.
Remove the stainless steel wash tank cover; clean with hot soapy water at a the wash sink. Wipe clean and dry.
12.
Remove the detergent wash tank drain/overflow to drain the tank, then flush the tank with fresh water and wipe with a clean cloth.
13.
Reassemble the glasswasher in reverse order for continued operation, or leave disassembled overnight to aid drying.
Cleaning Instructions
The cleaning instructions are attached to the inside of the glasswasher front door.
DO NOT CLEAN WITH HARSH DETERGENTS OR ABRASIVE SCOURING PADS.
DO NOT STRIKE THE CONVEYOR ON THE FLOOR OR ANY HARD SURFACE.
DO NOT STRIKE SCREENS ON HARD SURFACES.
DO NOT LEAVE WATER IN THE GLASSWASHER OVERNIGHT.
Cleaning
Weekly Cleaning, After 7 Days or 56 Hours of Operation:
1.
Complete 1-12 in the Daily Cleaning above.
2.
Remove chemical supply containers if they are stowed inside the glasswasher, wipe any chemical spills with a damp cloth.
Detergent and sanitizer (Chlorine) are corrosive on metal and must be removed as much as possible.
3.
Check the inlet chute on the right-side of the detergent tank and flush with fresh warm water to clean any chemical residue.
4.
Check chemical supply lines. If a line(s) are restricted, remove the pick-up tube(s) from the container(s), then insert each pick-up tube
in separate container(s) filled with fresh warm water.
5.
PUSH and HOLD the PRIME BUTTON labeled for the matching chemical tube until the water moves freely through the supply
tubing. Repeat for each chemical making sure that the warm water is fresh and free of any other chemical.
6.
Return the the pick-up tube(s) to the chemical container matching the label on the supply tube(s), then PUSH and HOLD the
PRIME BUTTON for the matching chemical(s) until the chemical moves freely through the supply tube(s).
7.
Inspect the chemical dispensing pumps visible behind the plexiglass window located on the front of the control box. PUSH and HOLD
each PRIME BUTTON. One white wheel behind the window for each PRIME BUTTON pushed and held.
8.
Find the spray tube assemblies, (3 spray tubes each) located in the wash chamber. There are (2) assemblies in the top and (2)
assemblies in the bottom. Pull (1) assembly at a time. Check the black O-ring on the spray tube hub for damage, replace if missing.
9.
Insert and twist the small brass drill bit (reamer) in the each spray tube hole to clean. Insert and twist the large drill on the wood
handle. Push the large reamer down the length of the spray tubes. Insert and twist the long brush in each spray tube to remove
loose debris. Flush the spray tube assembly, then reinstall in the glasswasher. Repeat for each spray tube assembly.
10.
Reassemble the glasswasher in reverse order for continued operation, or leave disassembled overnight to aid drying.