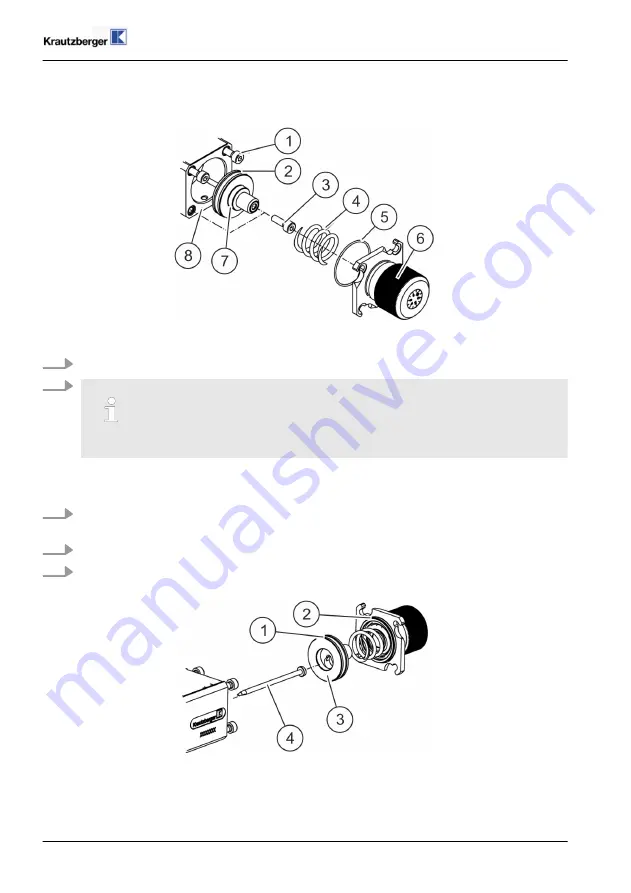
8.5 Changing the fluid needle
Removing the fluid needle
Fig. 13: Removing fluid needle
1.
Loosen the screws ( Fig. 13/1) slightly.
2.
Locking piece ( Fig. 13/6) (optional) is under spring force.
Turn the locking piece ( Fig. 13/6) (or depending on the design of the cover) slightly anti-
clockwise and remove it.
3.
Remove the pressure spring ( Fig. 13/4) and if necessary the seal ( Fig. 13/5) (only for
double controller).
4.
Screw a screw ( Fig. 13/1) into the control piston ( Fig. 13/7).
5.
Pull out the control piston ( Fig. 13/7) from the main element ( Fig. 13/8) using the screw (
Fig. 13/1).
Fig. 14: Removing fluid needle
Operating instructions
T-Dok-449-GB-Rev.7
[email protected], www.krautzberger.com
GB–34
Summary of Contents for RA 5
Page 52: ......