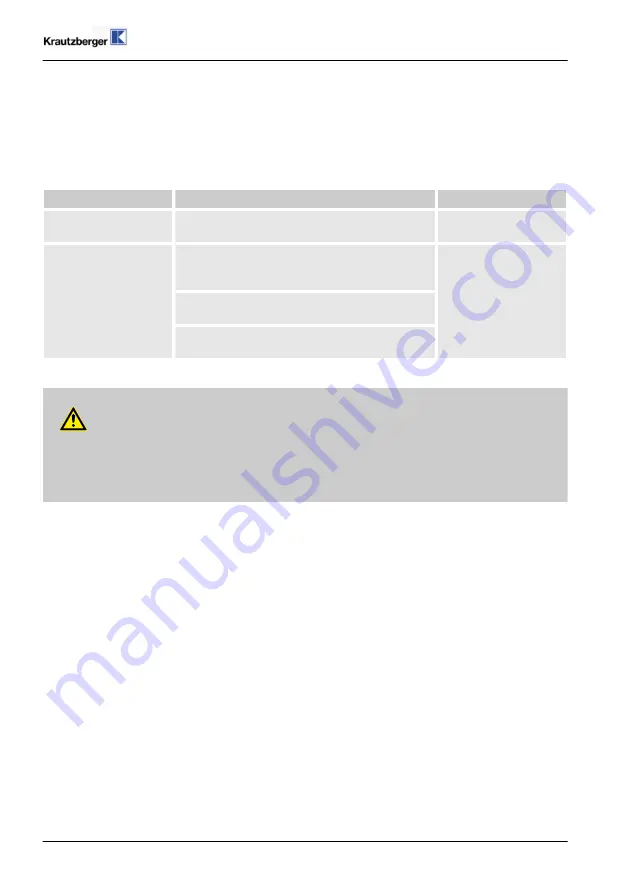
8.2 Maintenance schedule
The following sections describe the maintenance work that is required for optimal and defect-free
operation of the device. Check wearing parts such as seals and nozzles at regular intervals. The
level of wear depends on the abrasiveness of the spray medium used. Escaping air and spray
medium as well as the deterioration of the spray pattern are signs that parts are worn. Contact
Krautzberger Customer Care with any questions on maintenance work and maintenance intervals.
Interval
Maintenance work
Personnel
before performing any
maintenance work
Specialised personnel
if needed
Change material nozzle and air nozzle (
Chapter 8.4 ‘Changing the material nozzle
and the air nozzle’ on page 29
)
Specialised personnel
‘Changing the material needle’ on page 30
Change needle seals (
‘Changing the needle seals’ on page 32
8.3 Cleaning
WARNING!
Risk of injury due to improper cleaning!
–
Adhere to the safety data sheets of the cleaning product manufacturer.
–
Do not immerse the mini spray gun entirely in cleaning product.
Operating instructions
T-Dok-015-GB-Rev.0
[email protected], www.krautzberger.com
GB–28
Summary of Contents for 1050-090-1127
Page 44: ......