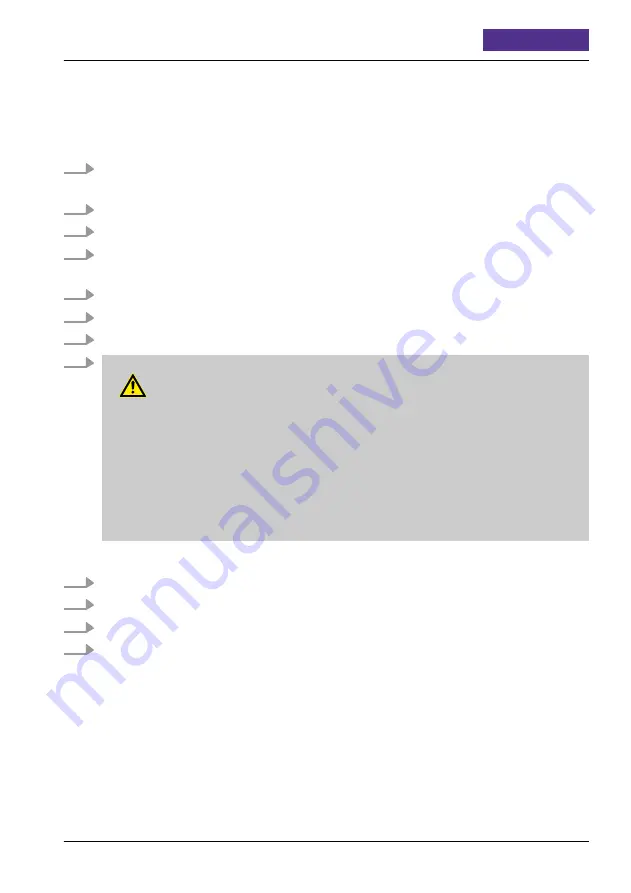
n
Never point the compressed air at living beings.
n
Adhere to the operating manuals for the respective components.
7.3 Shutting down
7.3.1 Temporary shut-down
End the spray process by switching off the control air (connection "St").
7.3.2 Long-term shut-down
1.
End the spray process by switching off the control air (connection "St").
2.
Close the material supply and switch off the pump if necessary.
3.
If necessary, clean the mini spray gun (
Chapter 8.3 ‘Cleaning’ on page 28
).
7.4 Start-up
1.
Switch on the compressed air supply.
2.
Where applicable, switch on pump or pressurised container for spray medium.
3.
Point the mini spray gun at a test surface.
4.
WARNING!
Vibrations caused by pulsation-generating compressor units!
Vibrations caused by pulsation-generating compressor units (pumps, compressors)
can be transferred to the spray gun via hose lines and lead to neurological or vascular
disorders.
Note:
–
Take breaks between spray processes.
–
Use pulsation-dampening devices (pressure compensation container, etc.).
Begin the spray process by switching on the control air.
5.
Chapter 7.5 ‘Adjusting the spray pattern’ on page 25
6.
End the spray process by switching off the control air.
7.
Direct the mini spray gun towards the work piece.
8.
Begin the spray process by switching on the control air.
7.5 Adjusting the spray pattern
Air and material nozzles are available in various sizes. There are 4 different families:
n
Round jet
– cone-shaped jet in front of the nozzle.
n
Flat jet
– width-adjustable jet for flat-shaped application.
n
Rotary jet
– a rotary pulse produces a highly "swirled" spray jet; for difficult work piece geo-
metries (angular sections etc.).
n
Full-cone rotary jet
– a rotary pulse produces a highly "swirled" spray jet; for difficult work
piece geometries (back cuts, etc.).
The spray pattern can be adjusted with the following measures:
Mini spray gun MA-1
ENGLISH
■
200-0345
GB–25
Summary of Contents for 1050-090-1127
Page 44: ......