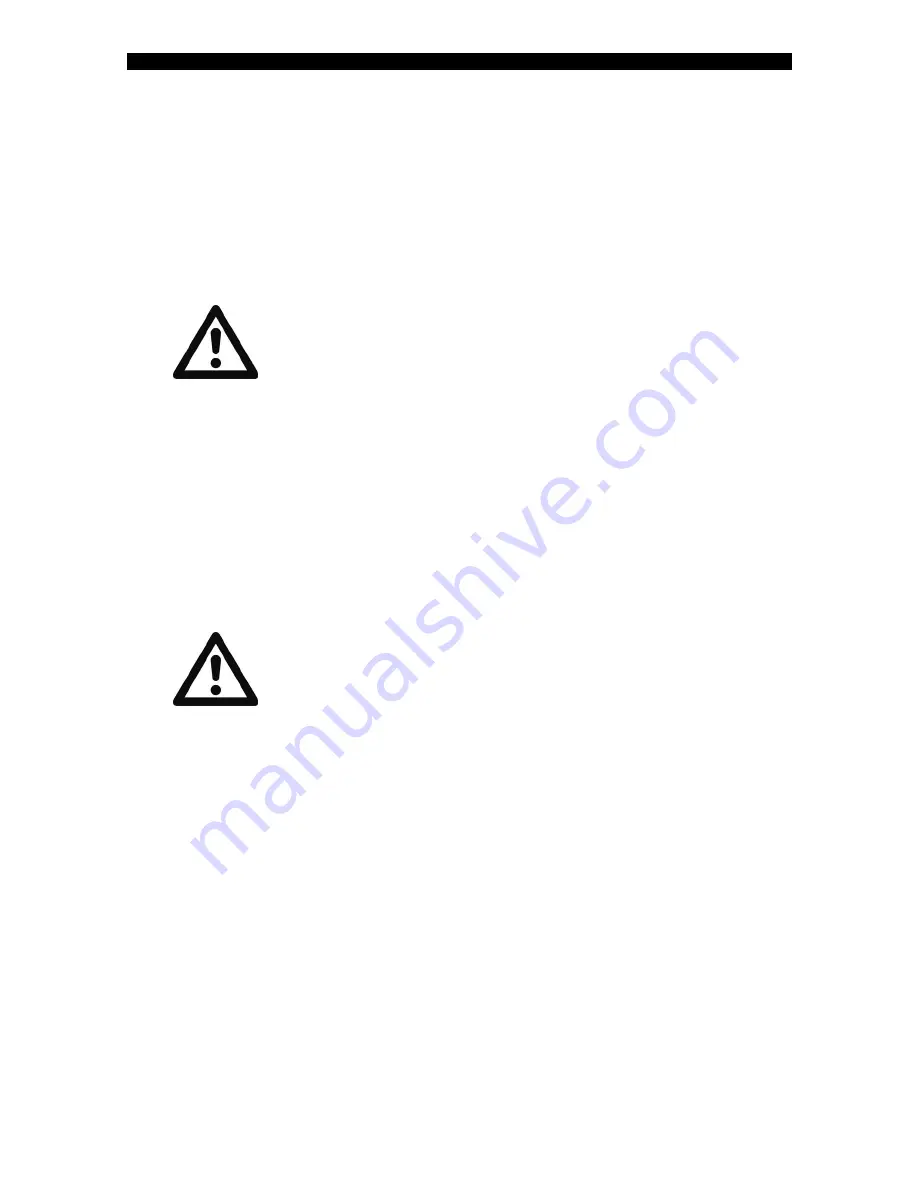
4. OPERATION AND MAINTENANCE
©2014 Kraus Global Ltd.
Retail CNG Dispenser Manual
37
4.3.3 Leak monitoring
Leaks in dispenser equipment may develop within the first few
weeks of operation and, therefore, must be closely monitored
throughout this time. Thereafter, routinely scheduled maintenance
must be carried out to correct and prevent further leaks.
The following steps are guidelines for detecting and repairing leaks.
CAUTION
NEVER TIGHTEN, LOOSEN, OR ATTEMPT TO REMOVE A PRESSURIZED
FITTING.
Leak-testing procedure
1.
Remove the bottom panels of the dispenser to access the lower
cabinet.
2.
Apply a leak detector to all fitting connections—we recommend
using Snoop® Liquid Leak Detector.
3.
Thoroughly inspect all fitting connections for bubbles, which
indicate a leak. Be sure to note or mark the locations where leaks
are found.
4.
If leaks are found, vent gas from the dispenser—see
Dispenser-
venting procedure
—and proceed with repairing the leak.
CAUTION
If a leak appears downstream of a sequencing valve, you must authorize a
fill to vent the trapped gas. Continue authorizing a fill until the pressure
gauge reads 0 psi and all venting sounds have ceased.
Leak repairing procedure
1.
Ensure the dispenser is completely vented.
2.
Loosen and retighten the fittings where leaks are found; most
fittings can be repaired simply by tightening it.
3.
Pressurize the dispenser to 100 psi and reassess all fitting
connections with a leak detector.
4.
Continue pressurizing the dispenser and testing for leaks at 500
psi intervals until the dispenser reaches regular operating
pressures.
NOTE: Repeat steps 1 – 3 if leaks are discovered. If leaks persist,
contact our Technical Support Department at 204-663-3601,
ext.212.