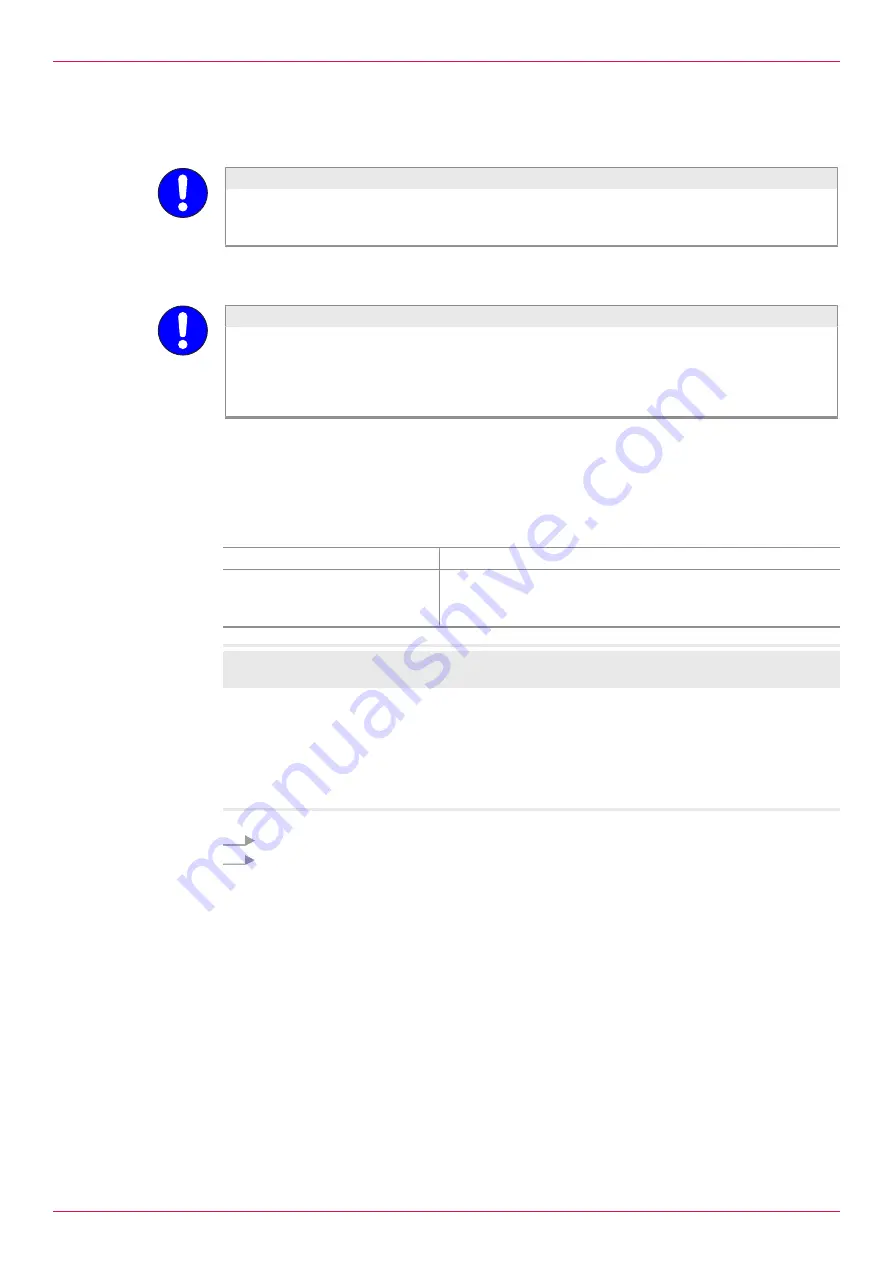
8 Installation, removal
8.1 Dangers during installation
8 Installation, removal
8.1 Dangers during installation
The following safety instructions must be observed strictly:
o
Have all work only carried out by authorized qualified personnel.
o
Do not take apart the flowmeter.
o
Do not remove the protective caps from the dry sleeves.
8.2 Dangers during removal
The following safety instructions must be observed strictly:
o
Have all work only carried out by authorized qualified personnel.
o
Ensure that the collection tank for emitted liquids is sufficiently large.
o
Collect any discharging pumped liquid safely and dispose of it in an environmentally compatible
manner in accordance with the applicable local regulations.
o
Place the protective caps onto dry sleeves.
8.3 Installing the flowmeter
8.3.1
Protecting the flowmeter against soiling
Notice
Soiling in the pipe system impairs the service life of the flowmeter. In order to protect the flowmeter
against soiling the manufacturer generally recommends the installation of an operating filter.
Personnel qualification:
o
Fitter
Personal protective equipment:
o
Work clothing
o
Protective gloves
o
Safety boots
ATTENTION
Damage to device through solid particles in the pipe system.
► During welding work attach protective covers in front of the connecting flanges.
► Ensure when welding that welding beads and abrasive dust cannot get into the pipe system and
the flowmeter.
► Ensure that an operating filter is installed when the pipe system is flushed and cleaned using the
flowmeter.
1.
Install the operating filter in front of the flowmeter, mesh width
2.
After the connecting work clean the pipe system thoroughly
8.3.2
Installation types
Flowmeters can be operated in different installation positions.
Both flow directions are possible. The preferred flow direction is indicated on the rating plate by means
of a bright arrow
Ä
Operating instructions
OIO 08en-GB Edition 2020-01
23