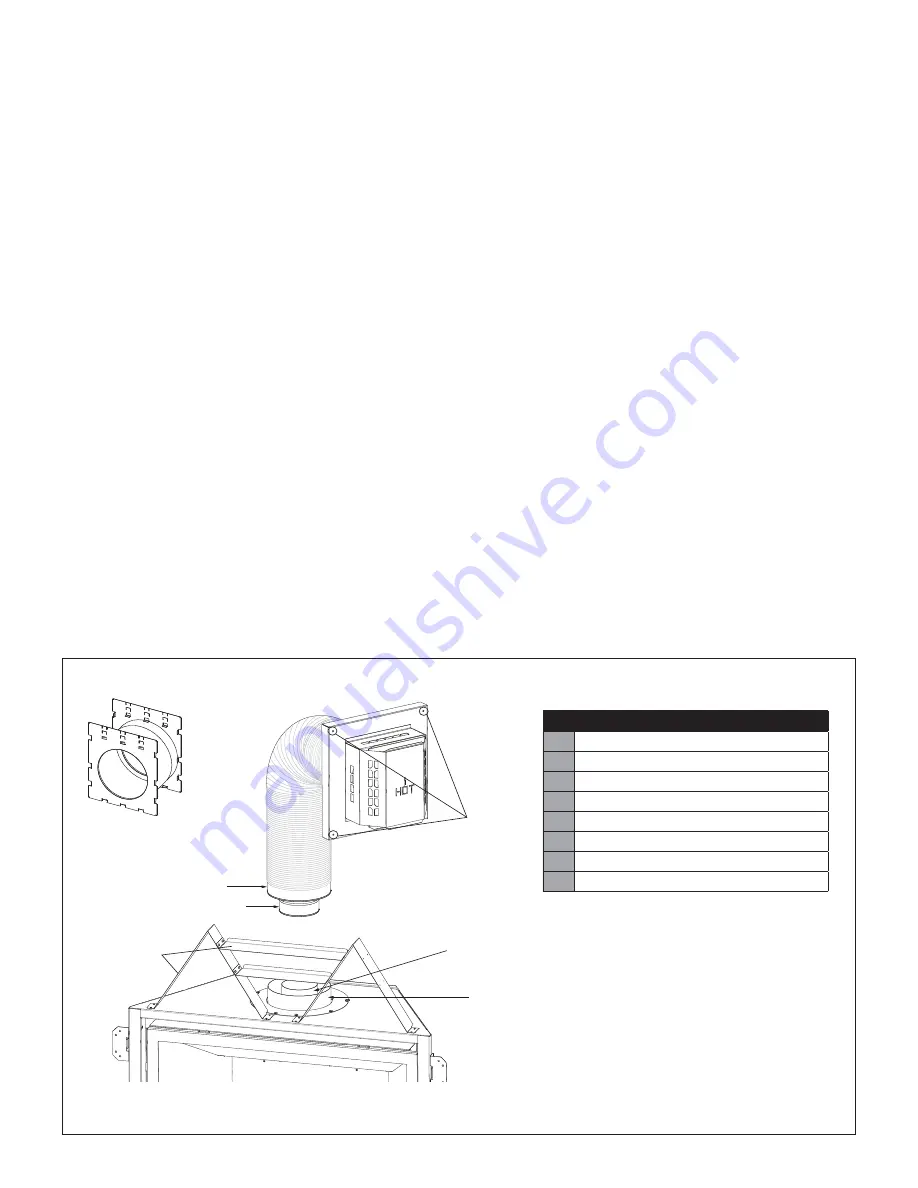
VENTING
29
7.9 #700-2 Series Direct Vent
Termination Kit(s)
IMPORTANT: The vertical vent heat shield included with
this fireplace must be installed for every type of top venting
application. The horizontal vent heat shield must be installed
when incorporating minimum horizontal venting off the top.
IMPORTANT: The flex pipe is permanently attached to the
exterior plate. DO NOT ATTACH either #745-2 or #718-2
termination kit to fireplace (or extension kit) until it has passed
through the wall. Install termination plates to the outside wall
exterior.
IMPORTANT: The minimum bend radius to center is 6 in (152
mm) required for installation of the flexible vent pipe. Care
should be taken when installing to avoid a tight bend that may
cause abrasion or damage to the flexible pipe.
• If terminating against vinyl siding, a vinyl siding protector
must be used (included with the #745-2 and #718-2 direct
vent kits). Follow instructions included.
• Each #746-2 extension kit contains enough 4” & 7” flexible
aluminum pipe to extend chimney an additional 6 ft (1.83 m).
7.9.1 Assembly and Installation
1. Attach vinyl siding protector (G) (not shown).
2. Mount the required wall thimble (H) with 1 in (25 mm) top
clearance and 1 in (25 mm) side clearance to the exterior
wall, and seal.
(OPTIONAL) insulate the wall thimble with any unfaced
insulation products listed as non-combustible per ASTM E
136.
3. Apply a liberal bead of exterior sealant around outer edge of
termination box (A), placing assembly through the wall-pass
through in exterior wall. Place screws through the four holes
(B), securing it in place.
4. Form the 4” & 7” flexible aluminum pipes on termination kit
(#745-2 or #718-2), and if applicable, on each extension kit.
5. Gently pull 4” & 7” pipes down to the top of the fireplace, or if
applicable, the extension kit.
IMPORTANT: DO NOT stretch extension kit beyond 6 ft.
(1.83 m); DO NOT stretch beyond what is required. It is
very difficult to decompress flex pipes once stretched.
6. Place a bead of sealant outside 4” flex pipe collar (C) (end
with EXTERNAL LIP) and sliding it into 4” pipe on extension
kit or top of fireplace (D). Secure with 3 evenly spaced
screws.
7. Place a bead of sealant inside 7” flex pipe collar (E) (end
with the INTERNAL lip), sliding it over 7” pipe on top of
fireplace (F). Secure with 3 evenly spaced screws.
8. If additional extension kits are required, repeat Steps 4 and
5, placing 4” & 7” pipes onto previous extension kit.
LEGEND
A
Termination box
B
Holes in exterior wall plate (only 3 shown)
C
4” flex pipe collar
D
4” pipe on fireplace or extension kit
E
7” flex pipe collar
F
7” pipe on fireplace or extension kit
G
Vinyl firestop (not shown)
H
Wall Thimble with 1 in (25 mm) top clearance
Figure 7.8, Installation and Assembly of #700-2 Series (Vent Heat Shield Assembly not shown for clarity purposes only)
C
E
H
F
D
STAND-OFFS
A
B
#700-WPT