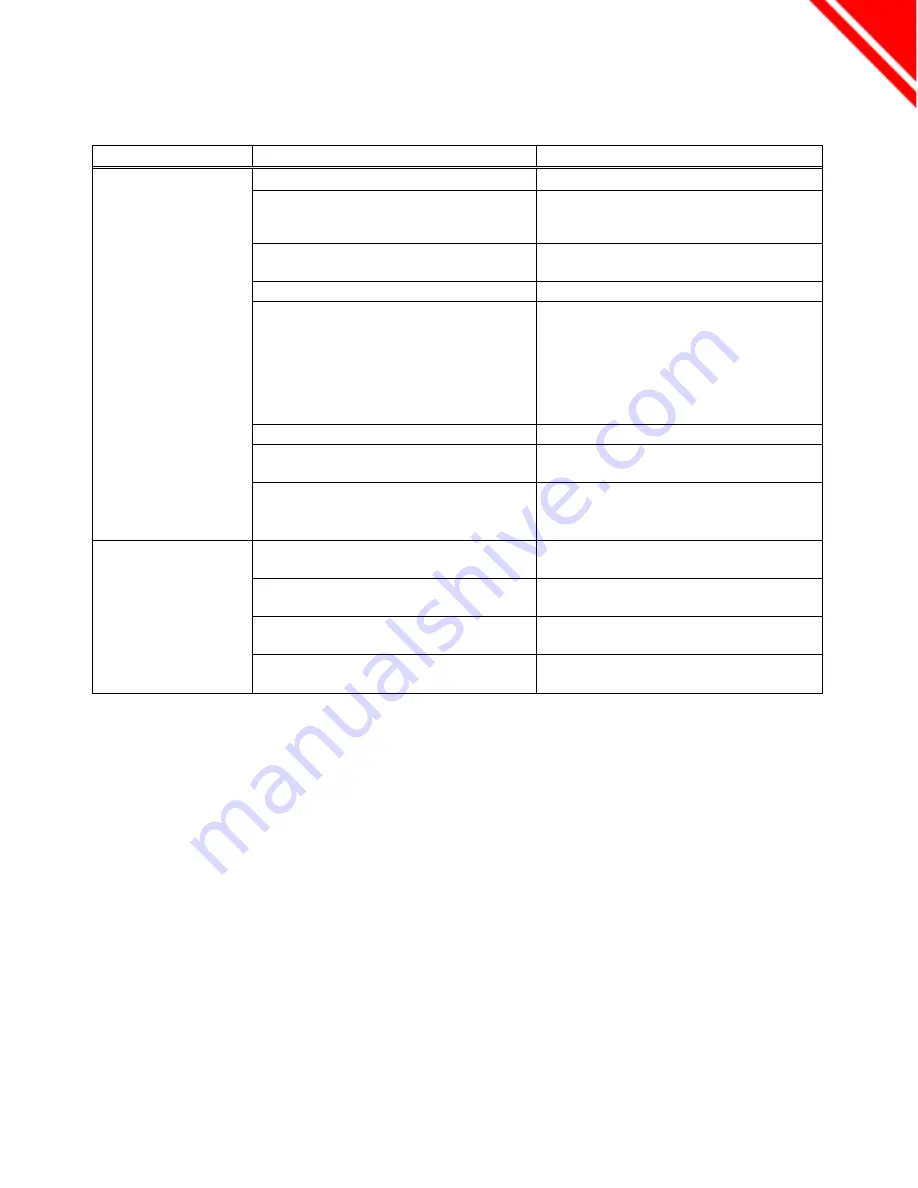
I
MO-D52/R52
14
9/21 Rev. 0
Troubleshooting and Remedies
Symptom
Cause
Remedy
No or slow operation
•
Decrease of supply air-pressure
•
Supply the specified air-pressure.
•
Clogging or leakage from the air
piping
•
Clean the piping, retighten the
connecting portion or re-arrange the
piping.
•
Air leakage from the clamping parts of
diaphragm
•
Retightening, disassemble and repair
(replacement)
•
Air leakage from the actuator rod unit
•
Disassemble it to replace the O-ring.
•
Issue with the accessories such as
positioner, booster relay, solenoid
valve and lock valve
•
Apply the specified air-pressure
directly to the instrument air
connecting port of the actuator, not
through the accessories. If no
anomaly is found with it, re-adjust the
booster relay and positioner or check
the accessories and replace them.
•
Issue with the actuator
•
Disassemble and repair the actuator.
•
The manual operation handle is set in
the manual operation position.
•
Set the handle to the position shown
in Fig. 5 or 6 in “Operation” section.
•
Sensitivity of the positioner is
insufficient.
•
Follow the instructions in the operation
manual for the positioner and replace
the capacitor spring.
Instable operation
(hunting)
•
Load change by the control fluid
(Insufficient output of the actuator)
•
Enlarge the size of the actuator.
•
Signal perturbation of the controller
•
Change the respective setting of the
controller.
•
Fluctuation of supply air pressure
•
Re-check the diameter of supply air
piping. Replace it.
•
Malfunction of the pressure reducing
valve
•
Repair the pressure reducing valve or
replace it.