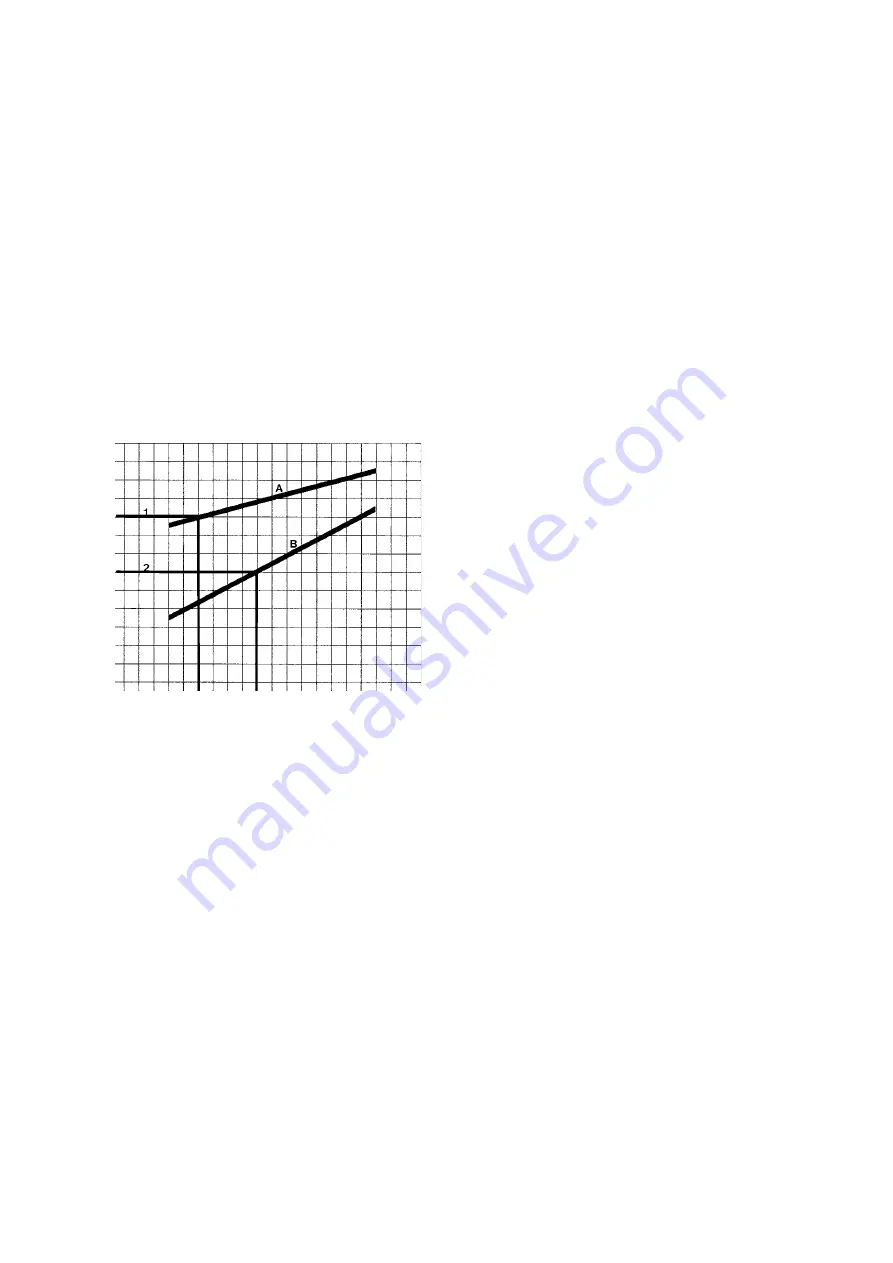
14
Before starting the grading of the malting barley, it
is advantageous to know the grading of the starting
material (the unsorted grain). This may be deter-
mined manually by means of test screens, or you
can ask a feedstuff dealer to test one or more sam-
ples.
Based on the grading of the sample and the outer
screen, use the diagram overleaf to indicate the
capacity required to obtain a final grading result of
90 % grains exceeding 2,5 mm.
Recommended capacities for malting barley
grading
(A) Screen 2,5 x 16,5 mm
(B) Screen 2,65 x 16,5 mm
The recommended capacities are subject to the
following conditions
Final sorting result: ................................
90 % grains
exceeding 2,5 mm
Moisture content: .....................................
Max. 14 %
(well threshed malting barley)
Inclination of cleaner:.............................................
9°
Examples:
1. Starting material sorting: ...........
82 %
Desired final sorting:
..................
90 %
Outer screen slots: ....................
2,5 x 16,5 mm
Recommended capacity
according to graph: ........................... 7 t/hour
2. Starting material sorting: ...........
76 %
Desired final sorting:
..................
90 %
Outer screen slots: ....................
2,65 x 16,5 mm
Recommended capacity
according to graph: ....................13,5 t/hour
If the starting material sorting is lower than the
curve of the outer screen used, this means that two
cycles will be required to reach a final sorting result
of 90 %.
Initial adjustment for malting barley grading
Declination: ...................
9°
Inner screen (mm): ........
Ø9 / Ø9 / Ø7,4/Ø7,4/Ø7,4
Outer screen (mm): .......
2,5 x 16,5 or 2,65 x 16,5
Selection of inner screen
The selection of the inner screen depends to a
high degree on the quality of the threshing and the
expected capacity. If the crop is reasonably well
threshed, it will sometimes be advantageous to
replace the 2nd section of the inner screen of Ø9
mm by an Ø7,4 mm screen and thereby obtain a
cleaner crop.
Selection of outer screen
The selection of the outer screen depends on the
desired capacity.
Where a high capacity is desired, the 2,65 x 16,5
mm screen should be selected. You risk, on the
other hand, a separation of good grains of 3 - 12 %
depending on the starting material grading.
The 2,5 x 16,5 mm screen should be selected
where a lower capacity and perhaps two cycles can
be accepted to achieve a final grading result of 90 %.
Control of grading
After the initial adjustment of the KDC 8000 and
operation at the capacity stated for two or three
minutes, samples should be taken to check if the
desired final result has been achieved.
When taking samples at the cleaner outlet, it is
recommended to collect the entire grain flow for a
short moment before selecting the desired quantity
from the collected grain.
The grading rate of the sample is found by means
of test screens. If the percentage is too low, reduce
the capacity, and if it is too high, increase the ca-
pacity. As crops will vary, however, it will be wise to
allow for a minor safety margin.
If the capacity is changed, new samples will have
to be taken. Continue this way until the desired
grading result of the finished product has been
obtained. When the correct capacity setting has
been reached, it is recommended to deliver a sam-
ple of the finished product to the feedstuff dealer for
testing, as the test screens are intended as a guide
only.
Starting material sorting %
Capacity (t/h)
90
88
86
84
82
80
78
76
74
72
70
68
66
64
0 2 4 6 8 10 12 14 16 18 20
Summary of Contents for KDC 8000
Page 1: ...KDC 8000 Combi cleaner Manual Brugsanvisning...
Page 35: ...35...