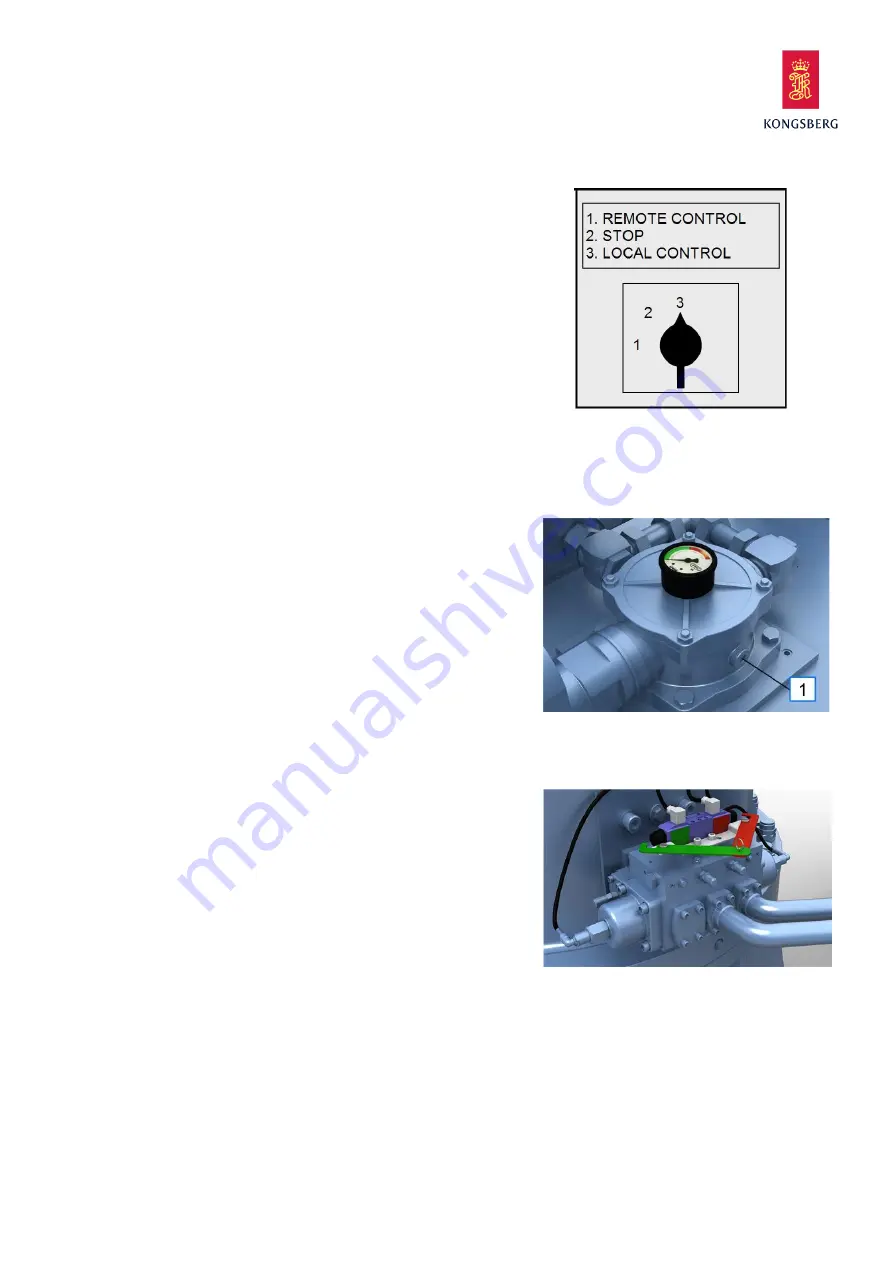
Maintenance manual
KONGSBERG PROPRIETARY.
This document and its accompanying elements contain KONGSBERG
information which is proprietary and confidential. Any disclosure, copying, distribution or use is prohibited if not
otherwise explicitly agreed with KONGSBERG in writing. Any authorized reproduction, in whole or in part, must
include this legend. ©2022 KONGSBERG - All rights reserved.
P a g e
24 |
66
11.1
Oil Sampling
1.
Start one of the pump units by turning the selector switch on
the corresponding motor controller to position 3 “
LOCAL
CONTROL
”.
2.
Let the pump unit run for at least five minutes.
3.
Turn the selector switch on the motor controller to position
2 “
STOP
”.
4.
Unscrew an unused plug [1] in the return filter.
5.
Connect a measuring hose (preferable with a valve mounted
on it) and make sure the other end is secured in a bucket.
6.
Again, start the same pump unit by turning the selector switch on the relevant motor controller
to position 3 “
LOCAL CONTROL
”.
7.
Make sure the hose valve (if mounted) is completely
open, and let the pump run until you are completely
sure that the hose is flushed thoroughly.
8.
Fill a new and chemically pure sample bottle with oil,
min 200ml.
9.
Close the sample bottle
10.
Turn the selector switch on the motor controller to
position 2 “S
TOP
”.
11.
Disconnect the sampling equipment and mount the plug.
12.
Again, start the pump unit and let it run for at least one
minute. This will make sure that any trapped air will
evacuate through the filter and into the tank.
13.
Manually move the rudder by using the red and green
Steering Gear handles as illustrated. If any noise or
steering problems present, follow the venting
procedure.
14.
Mark the bottle with AQM type and number, date, oil
type, sample taken by and how long used.
15.
Repeat steps 1-14 for the opposite pump system.
16.
Compare the oil sample with new oil. If color or smell has significantly changed or there are
impurities in the oil, change the oil.
17.
Send the oil samples to be examined immediately.