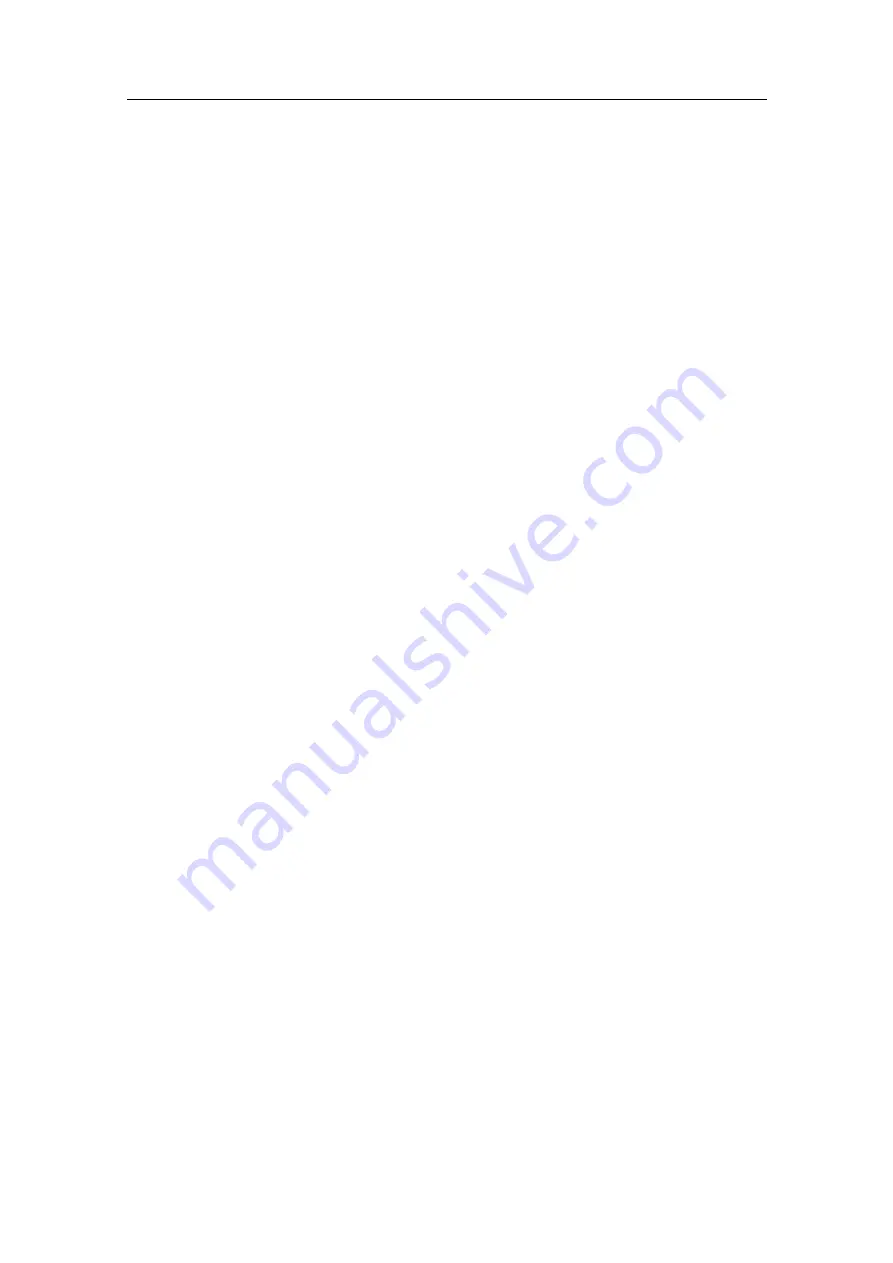
System test
• If a cable terminates in a plug at the unit, the test will be
more easily conducted if the plug is disconnected.
3
Select one pair of cable cores, and check that the cores are
connected to the correct terminals in the unit.
4
Connect your continuity tester to the two terminals in
question and check the continuity.
• If a low resistance exists between the two cores, this may
indicate the cores are connected to circuits or units with
low internal resistance. If this is the case, disconnect the
cores from the terminal block and test again.
• The resistance should be nearing ∞ ohms.
5
Tell your assistant to short the two cores together. Repeat
the previous test.
• The resistance should be 0 (zero) ohms.
6
Tell your assistant to remove the shorting strap.
• Check that the resistance reaches ∞ ohms again.
7
Check each core’s resistance to ground, and each core’s
resistance to all the other cores in the cable.
• All results should be close to ∞ ohms.
8
Assuming the test results are correct, the cores must
be reconnected to the terminal block (if they had been
removed), and the terminals checked to ensure they are tight.
9
On completion, move on to the next pair of cores and repeat
the tests until the entire cable has been checked.
9.2.3 Operational voltages
Check that the operational voltages on the equipment match the
power available on the vessel.
9.3 Final installation checks
After installation - but before un-docking - a number of
verification must be done to check that the mechanical end
electrical installation has been performed correctly.
Procedure
1
Check that the measured positions of the transducers, motion
sensor and positioning system antenna are reasonable by
comparing them with those estimated from the vessel
drawings.
2
Check that the measured installation angles of the
transducers is reasonable by comparing them with
measurements done with a simple inclinometer.
164851/C
107
Summary of Contents for EM 710
Page 1: ...Installation Manual EM 710 Multibeam echo sounder ...
Page 2: ......
Page 44: ...Kongsberg EM 710 Figure 10 Transducer mounting principles 42 164851 C ...
Page 63: ...Cable layout Figure 20 Transceiver Unit front view 0 5 x 1 degree 164851 C 61 ...
Page 88: ...Kongsberg EM 710 Figure 42 Cable clamp Transceiver Unit cable clamp on page 133 86 164851 C ...
Page 113: ...Installation drawings 164851 C 111 ...
Page 114: ...Kongsberg EM 710 10 1 2 1 mounting frame assembly RX module 112 164851 C ...
Page 115: ...Installation drawings 164851 C 113 ...
Page 116: ...Kongsberg EM 710 10 1 3 2 mounting frame assembly TX RX module 114 164851 C ...
Page 117: ...Installation drawings 164851 C 115 ...
Page 118: ...Kongsberg EM 710 10 1 4 0 5 x 1 gondola 116 164851 C ...
Page 119: ...Installation drawings 164851 C 117 ...
Page 120: ...Kongsberg EM 710 10 1 5 Transducer TX1 Outline dimensions 118 164851 C ...
Page 121: ...Installation drawings 164851 C 119 ...
Page 122: ...Kongsberg EM 710 10 1 6 Transducer TX2 Outline dimensions 120 164851 C ...
Page 123: ...Installation drawings 164851 C 121 ...
Page 124: ...Kongsberg EM 710 10 1 7 Transducer RX1 Outline dimensions 122 164851 C ...
Page 125: ...Installation drawings 164851 C 123 ...
Page 126: ...Kongsberg EM 710 10 1 8 Transducer RX2 Outline dimensions 124 164851 C ...
Page 127: ...Installation drawings 164851 C 125 ...
Page 128: ...Kongsberg EM 710 10 1 9 HWS Operator Station Outline dimensions 126 164851 C ...
Page 129: ...Installation drawings 10 1 10 Transceiver Unit Outline dimensions 164851 C 127 ...
Page 130: ...Kongsberg EM 710 128 164851 C ...
Page 132: ...Kongsberg EM 710 130 164851 C ...
Page 133: ...Installation drawings 10 1 12 Transceiver Unit mounting bracket 164851 C 131 ...
Page 134: ...Kongsberg EM 710 10 1 13 Junction Box outline dimensions 132 164851 C ...
Page 135: ...Installation drawings 10 1 14 Transceiver Unit cable clamp 164851 C 133 ...