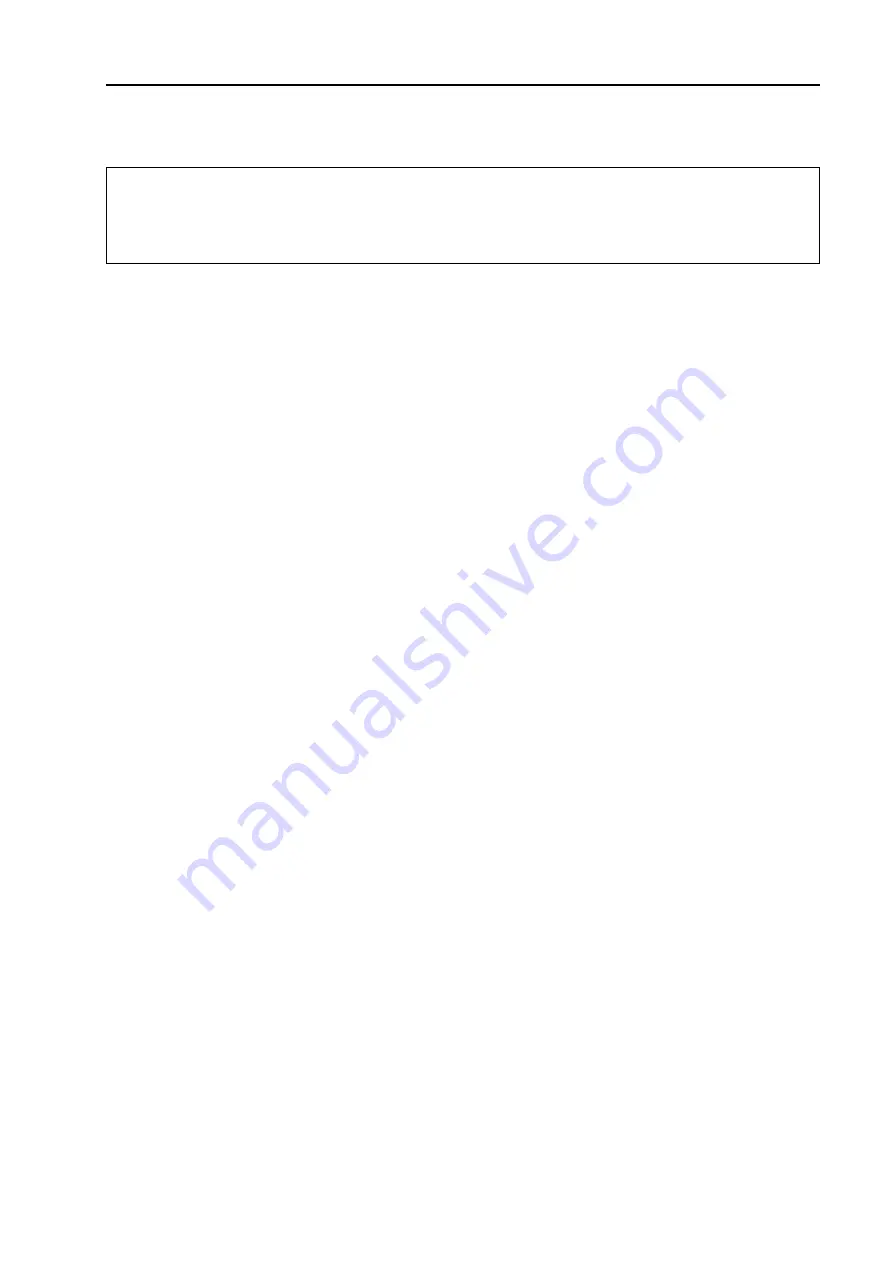
SEN04569-01
PC160LC-8
00-200
7
200 Foreword and general information
How to read the shop manual
How to read the shop manual
1
1.
Composition of shop manual
This shop manual contains the necessary technical information for services performed in a workshop.
For ease of understanding, the manual is divided into the following sections.
00. Index and foreword
This section explains the shop manuals list, table of contents, safety, and basic information.
01. Specification
This section explains the specifications of the machine.
10. Structure, function and maintenance standard
This section explains the structure, function, and maintenance standard values of each component.
The structure and function sub-section explains the structure and function of each component. It
serves not only to give an understanding of the structure, but also serves as reference material for
troubleshooting. The maintenance standard sub-section explains the criteria and remedies for dis-
assembly and service.
20. Standard value table
This section explains the standard values for new machine and judgement criteria for testing,
adjusting, and troubleshooting. This standard value table is used to check the standard values in
testing and adjusting and to judge parts in troubleshooting.
30. Testing and adjusting
This section explains measuring instruments and measuring methods for testing and adjusting, and
method of adjusting each part. The standard values and judgement criteria for testing and adjusting
are explained in Testing and adjusting.
40. Troubleshooting
This section explains how to find out failed parts and how to repair them. The troubleshooting is
divided by failure modes. The “S mode” of the troubleshooting related to the engine may be also
explained in the Chassis volume and Engine volume. In this case, see the Chassis volume.
50. Disassembly and assembly
This section explains the special tools and procedures for removing, installing, disassembling, and
assembling each component, as well as precautions for them. In addition, tightening torque and
quantity and weight of coating material, oil, grease, and coolant necessary for the work are also
explained.
90. Diagrams and drawings (chassis volume)/Repair and replacement of parts (engine volume)
q
Chassis volume
This section gives hydraulic circuit diagrams and electrical circuit diagrams.
q
Engine volume
This section explains the method of reproducing, repairing, and replacing parts.
2.
Revision and distribution
Any additions, revisions, or other change of notices will be sent to KOMATSU distributors. Get the most
up-to-date information before you start any work.
q
Some attachments and optional parts in this shop manual may not be delivered to certain areas. If one
of them is required, consult KOMATSU distributors.
q
Materials and specifications are subject to change without notice.
q
Shop manuals are divided into the “Chassis volume” and “Engine volume”. For the engine unit, see the
engine volume of the engine model mounted on the machine.
Summary of Contents for ecot3 PC160LC-8
Page 1: ...HYDRAULIC EXCAVATOR SEN04566 13 PC160LC 8 SERIAL NUMBERS 25001 and up ...
Page 2: ...Find manuals at https best manuals com ...
Page 13: ...SEN04568 13 PC160LC 8 00 100 11 100 Index Table of contents ...
Page 51: ...This as a preview PDF file from best manuals com Download full PDF manual at best manuals com ...