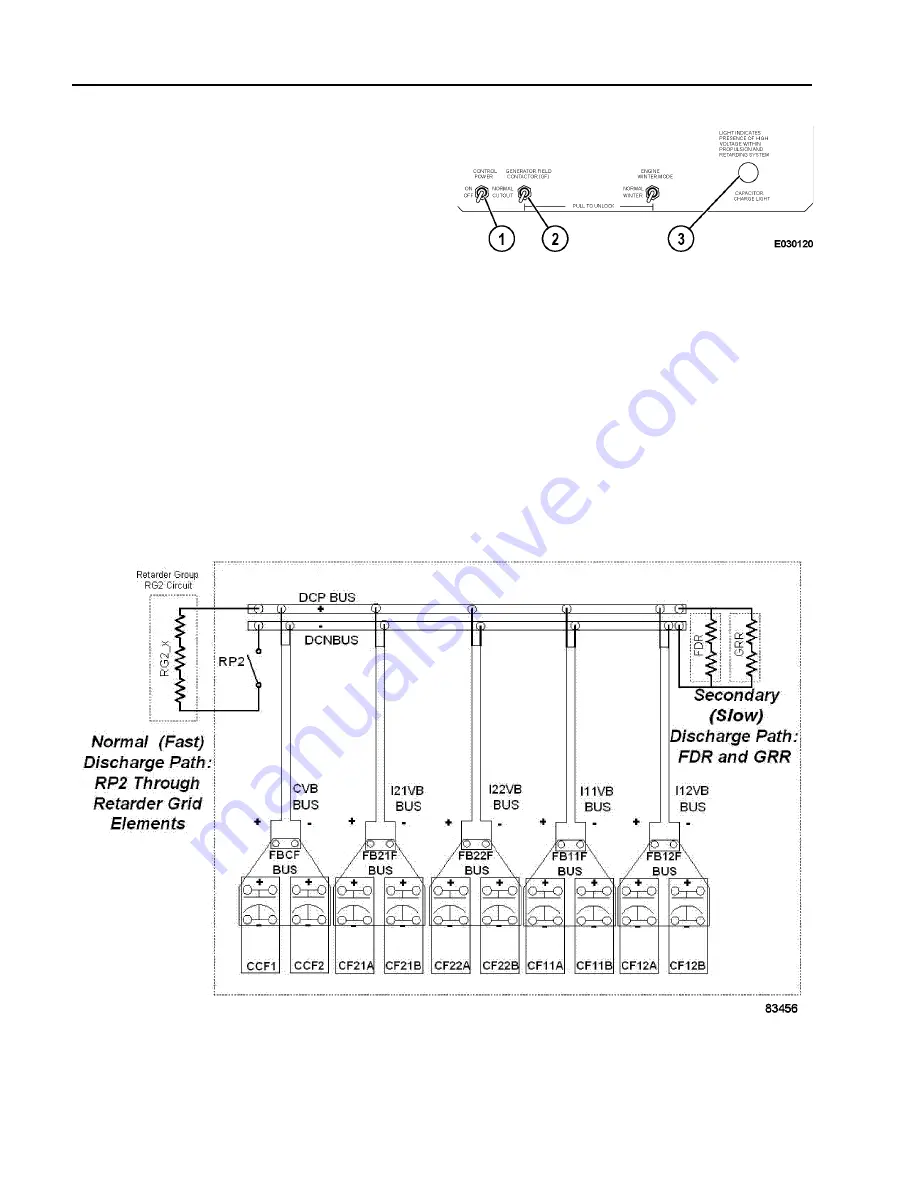
CEN00002-05
00 Index and foreword
26
Manual DC link capacitor discharge procedure
Follow any and all local and site specific procedures
and requirements for working on off-highway mining
equipment.
Verify that:
• The engine is off and the parking brake is on.
• The generator field is cut out via GF cutout switch
(2, Figure 00-4) in the low voltage area of the
control cabinet.
1. Apply control power for a minimum of 30 sec-
onds. Then, turn off control power using control
power switch (1) on the switch panel.
With control power on, an RP contactor closes
and discharges the DC link through the
retarding grids in less than 10 seconds.
In most control cabinets, RP2 is the normal discharge
path. In groups containing an RP3 contactor, RP2
and RP3 are alternated as the normal discharge
path. Refer to Figure 00-5.
FIGURE 00-4. INFORMATION DISPLAY PANEL
1. Control Power Switch
2. GF Cutout Switch
3. Capacitor Charge
Light
FIGURE 00-5. DISCHARGE PATHS
Summary of Contents for 960E-1 -
Page 1: ...CEBM023802 Shop Manual DUMP TRUCK SERIAL NUMBERS A30025 A30026 ...
Page 2: ...Find manuals at https best manuals com ...
Page 17: ...00 Index and foreword CEN00011 02 15 NOTES ...
Page 51: ...This as a preview PDF file from best manuals com Download full PDF manual at best manuals com ...