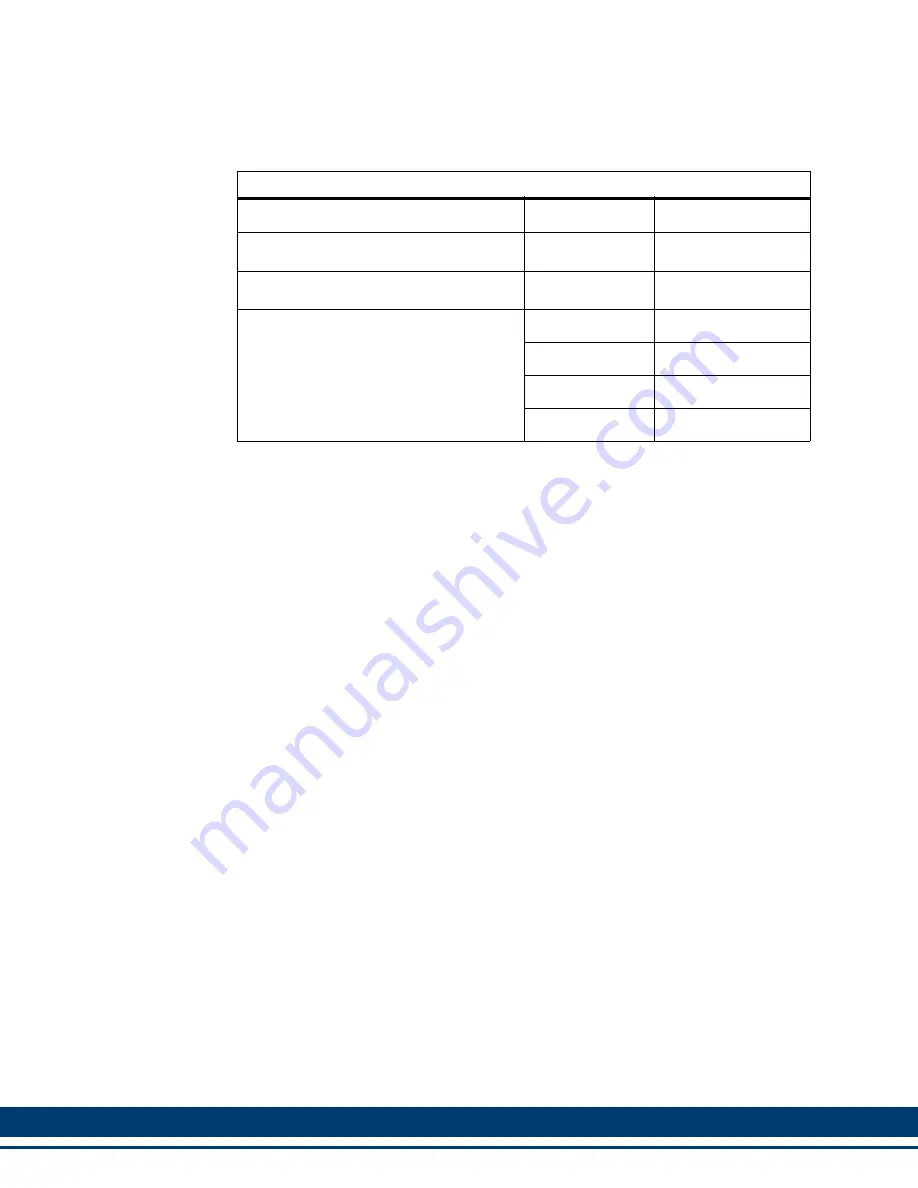
Kollmorgen - December 2011
223
MMC Smart Drive Hardware Manual
-
S200-DLS DRIVE
Table 8-8: Aux Feedback Port Breakout Box and Cables
Description
Length
Part Number
Aux Feedback Port Breakout Board
a
a. The Breakout Board (see
) is mounted directly to the Aux
Feedback connector, and provides screw terminals wire termination.
N/A
M.1302.6970
Aux Feedback Port Breakout Box
b
) is DIN-rail mounted, and pro-
vides screw terminal wire termination. Use one of the cables listed in the table to
connect between the Aux Feedback connector and the Breakout Box.
N/A
M.1302.6972
Aux Feedback Port to Breakout Box Ca-
ble
1 M (3.3 ft)
M.3000.0801
3 M (9.8 ft)
M.3000.0802
6 M (19.7 ft)
M.3000.0803
9 M (29.7ft)
M.3000.0804
Summary of Contents for Digital MMC Control
Page 2: ......
Page 10: ...8 Kollmorgen Decamber 2011 MMC Smart Drive Hardware Manual TABLE OF CONTENTS...
Page 128: ...126 Kollmorgen December 2011 MMC Smart Drive Hardware Manual 230V 1 3 PHASE MMC SMART DRIVE...
Page 214: ...212 Kollmorgen December 2011 MMC Smart Drive Hardware Manual 460V 3 PHASE MMC SMART DRIVE...
Page 246: ...244 Kollmorgen December 2011 MMC Smart Drive Hardware Manual MOTOR CABLES CONNECTORS...
Page 298: ...296 Kollmorgen December 2011 MMC Smart Drive Hardware Manual DECLARATIONS OF CONFORMITY...
Page 299: ...Kollmorgen December 2011 297 MMC Smart Drive Hardware Manual DECLARATIONS OF CONFORMITY...
Page 300: ...298 Kollmorgen December 2011 MMC Smart Drive Hardware Manual DECLARATIONS OF CONFORMITY...
Page 301: ...Kollmorgen December 2011 299 MMC Smart Drive Hardware Manual DECLARATIONS OF CONFORMITY...
Page 302: ...300 Kollmorgen December 2011 MMC Smart Drive Hardware Manual DECLARATIONS OF CONFORMITY...
Page 320: ...MMC Smart Drive Hardware Manual INDEX 318 Kollmorgen March 2011...
Page 322: ...320 Kollmorgen December 2011 MMC Smart Drive Hardware Manual SALES AND SERVICE...