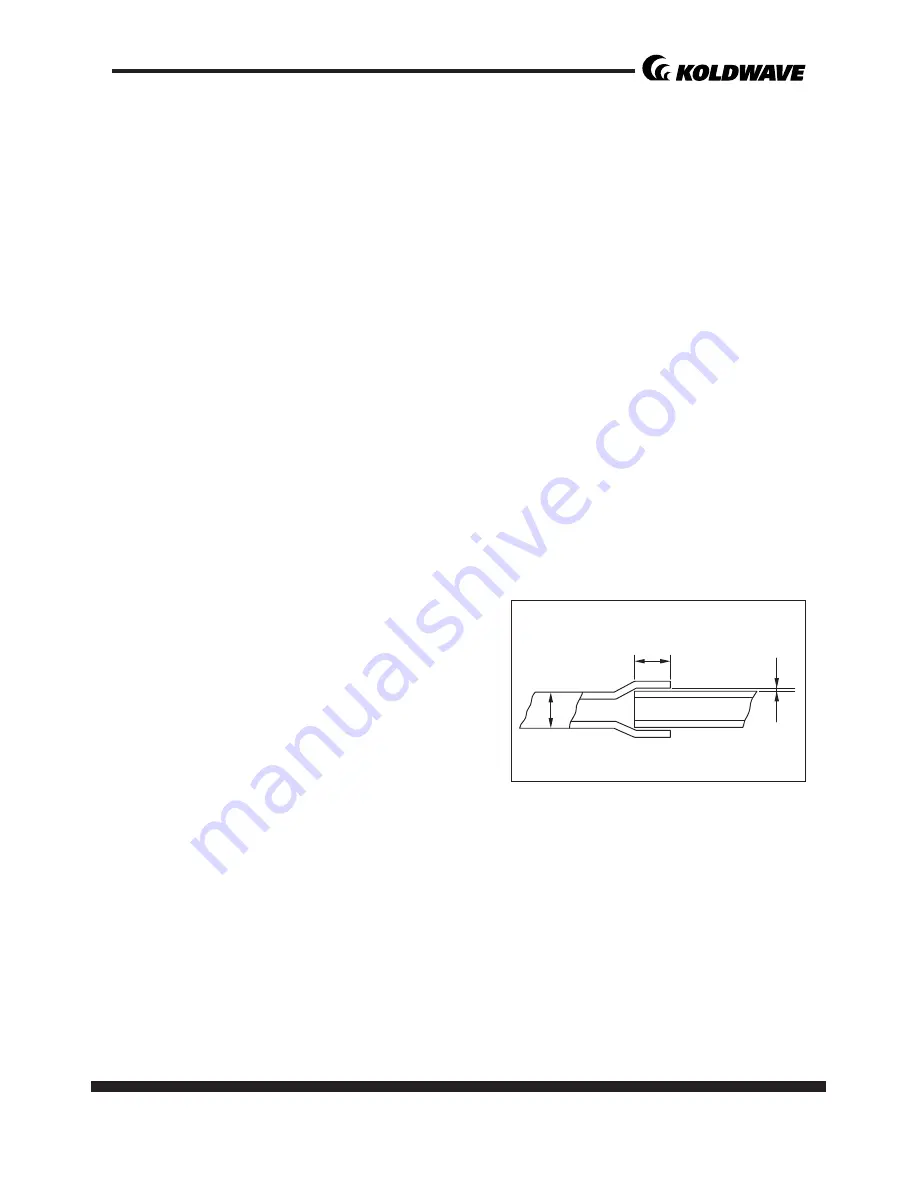
page
59
Service Manual
5KK14BEA2AA00 / 5KK21BGA2AA00 / 5KK30BGA2AA00
REFRIGERANT SYSTEM REPAIR
Brazing
• In the event of a leak, obstruc on, or trouble in the refrigerant system of the unit,
replace or repair the defec ve component. A er replacing defec ve component,
braze all connec ons.
1) Proper brazing techniques
• When brazing, use a slightly reduced fl ame. Oxyacetylene is commonly used since
the fl ame condi on can be easily judged and adjusted. Unlike gas welding, a sec-
ondary fl ame is used for brazing. Properly preheat the base metal according to the
shape, size and thermal conduc vity of the brazed fi
ng.
• The most important point in fl ame brazing is to bring the en re brazed fi
ng to
a proper brazing temperature. Care should be taken not to cause overfl ow of the
brazing fi ller metal, oxida on of the brazing fi ller metal, or fi ller metal deteriora-
on due to overhea ng the fl ux.
2) Brazed fi
ngs and fi
ng clearance
• In general, the strength of the brazing fi ller metal is lower than that of the base
metal. As such, the shape and clearance of
brazed fi
ngs are very important. Concern-
ing the shape of brazed fi
ngs, adhesive
area must be maximized. In addi on, the
clearance of the brazed fi
ng must be mini-
mized so that the brazing fi ller metal will
fl ow into the fi
ng via capillary ac on.
Clearance
Clearance From The Pipe Fing and Tubing.
0.001~0.003 in
(0.025~0.075 mm)
a
a