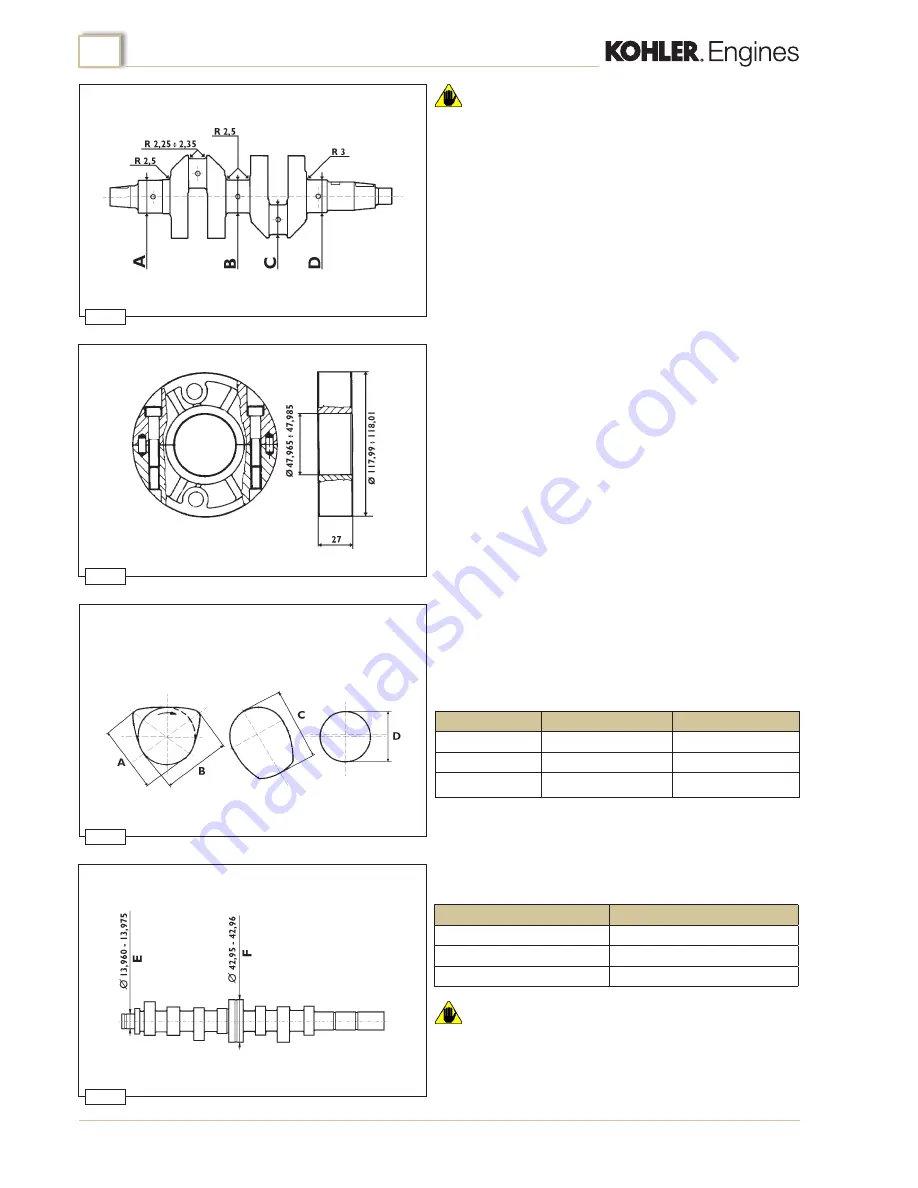
- 30 -
30
28
29
31
4
A
-
B
34,69
÷
34,74
C
34,98
÷
35,02
D
25,50
÷
25,70
0,025
÷
0,065
0,07
÷
0,105
0,04
÷
0,075
Checks and overhaul
Warning
•
During grinding take care not to remove the shim adjustment
material from the main journal thrust face to avoid changing the
crankshaft end float; also ensure that the grinding wheel radii
are as specified in figure 28 so as not to create crack initiation
sections on the crankshaft.
Oil seal rings
Check that the rings have not hardened around the internal
contact edge and that they show no signs of cracks or wear.
Warning
•
Renew the camshaft if the cams or journals show wear in excess
of 0.1mm.
Camshaft
Check the cams and bearing journals for scoring and wear.
Measure the dimensions and compare them to the values in the
table below and shown if figures 30-31.
Camshaft dimensions fig.30.
Assembly clearance between the journals and their housings
should be (fig.31):
Measurement
E
F
aluminium crankcase
F
cast iron crankcase
Measurement
Dimensions mm
Cam
Timing
Injection
Fuel pump
inlet/exhaust
injection
feeding pump
KD425-2 Workshop Manual_cod. ED0053031750_
1° ed
_ rev.
00
inlet/exhaust
injection
feeding pump
Central main bearings
In order to facilitate assembly the central main bearings are of
different external diameters (fig.29) and are machined with a
bevelled edge to assist their insertion into the crankcase.
Check the dimensions of the shells and renew them if they are
worn or deformed.
Also check the condition of the oil passages, if necessary, clean
them with paraffin or petrol and dry with compressed air.
Summary of Contents for KD425-2
Page 1: ...KD 425 2 WORKSHOP MANUAL...
Page 6: ...6 KD425 2 Workshop Manual_cod ED0053031750_1 ed_ rev 00...
Page 7: ...7 KD425 2 Workshop Manual_cod ED0053031750_1 ed_ rev 00...
Page 54: ...54 KD425 2 Workshop Manual_cod ED0053031750_1 ed_ rev 00...
Page 55: ...55 KD425 2 Workshop Manual_cod ED0053031750_1 ed_ rev 00...