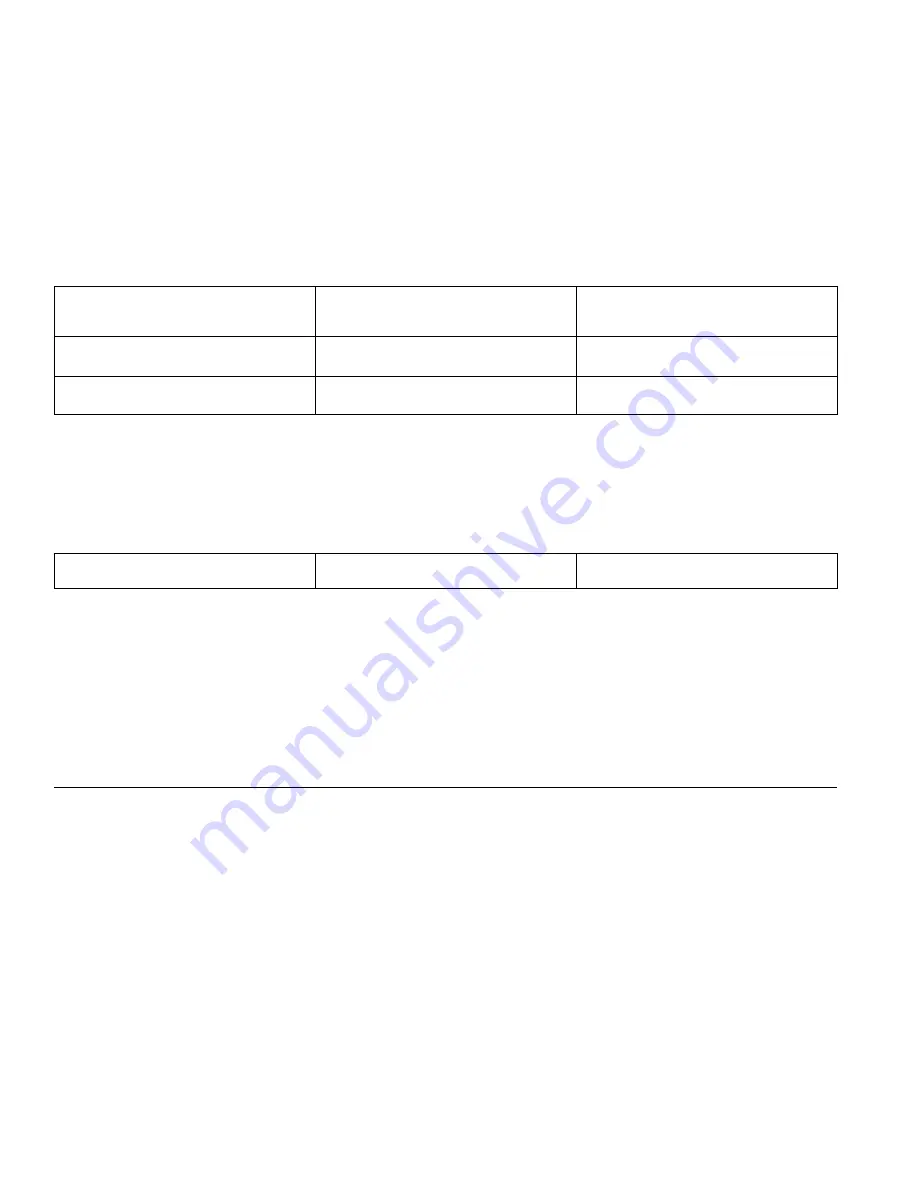
Electrical System
34
24 690 37 Rev. B
KohlerEngines.com
Test for Spark
NOTE: If 2 testers are available, testing can be performed simultaneously for both cylinders. However, if only 1 tester
is available, 2 individual tests must be performed. Side not being tested must have spark plug lead connected
or grounded. Do not crank engine or perform tests with 1 spark plug lead disconnected and not grounded, or
permanent system damage may occur.
1. With engine stopped, disconnect 1 spark plug lead. Connect spark plug lead to post terminal of spark tester and
attach tester clip to a good engine ground.
2. Crank engine over, establishing a minimum of 550-600 RPM, and observe tester(s) for spark.
3. Repeat spark test on opposite cylinder if cylinders are being tested individually.
Condition
Possible Cause
Conclusion
Both cylinders have good spark but
engine runs poorly or existing plug
condition is questionable.
Spark Plug(s)
Install new spark plug(s) and retest
engine performance.
1 cylinder has good spark and other
cylinder has no or intermittent spark.
Ignition
Test ignition modules and
connections.
Spark on both cylinders but power is
suspect.
Sheared Flywheel Key
Check for broken key.
Check Ignition Modules and Connections
1. Remove blower housing from engine. Inspect kill wire for any damage, cuts, or shorts to engine or ignition module
body. Check that connections are oriented properly on terminals of modules.
2. On MDI adjustable timing engines, ensure that both modules are correctly installed with flat side of module
out/towards you.
Condition
Possible Cause
Conclusion
All checks are OK but module has no
spark or fails to advance.
Ignition Module
Replace affected module.
BATTERY CHARGING SYSTEM
NOTE: Observe following guidelines to avoid damage to electrical system and components:
● Make sure battery polarity is correct. A negative (–) ground system is used.
● Disconnect rectifier-regulator plug and/or wiring harness plug before doing any electric welding on equipment
powered by engine. Disconnect all other electrical accessories in common ground with engine.
● Prevent stator (AC) leads from touching or shorting while engine is running. This could damage stator.
Most engines are equipped with a 15 or 20 amp regulated charging system. Some have a 25 amp regulated charging
system.
15/20/25 Amp Regulated Charging System
Stator
Stator is mounted on crankcase behind flywheel. Follow procedures in Disassembly and Reassembly if stator
replacement is necessary.
Rectifier-Regulator
NOTE: When installing rectifier-regulator, take note of terminal markings and install plug(s) accordingly.
NOTE: Disconnect all electrical connections attached to rectifier-regulator. Testing may be performed with rectifier-
regulator mounted or loose. Repeat applicable test procedure 2 or 3 times to determine condition of part.
Rectifier-regulator is mounted on blower housing. To replace it, disconnect plug(s), remove two mounting screws, and
ground wire or metal grounding strap.
Testing of rectifier-regulator may be performed as follows, using appropriate Rectifier-Regulator Tester.
To test 15 amp rectifier-regulators:
1. Connect tester ground lead (with spring clamp) to body of rectifier-regulator being tested.
2. Connect tester red lead to B+ terminal of rectifier-regulator and 2 black tester leads to 2 AC terminals.
3. Plug tester into proper AC outlet/power for tester being used. Turn on power switch. POWER light should be
illuminated and 1 of 4 status lights may be on as well. This does not represent condition of part.
4. Press TEST button until a click is heard and then release. Momentarily 1 of 4 status lights will illuminate, indicating
condition of part.