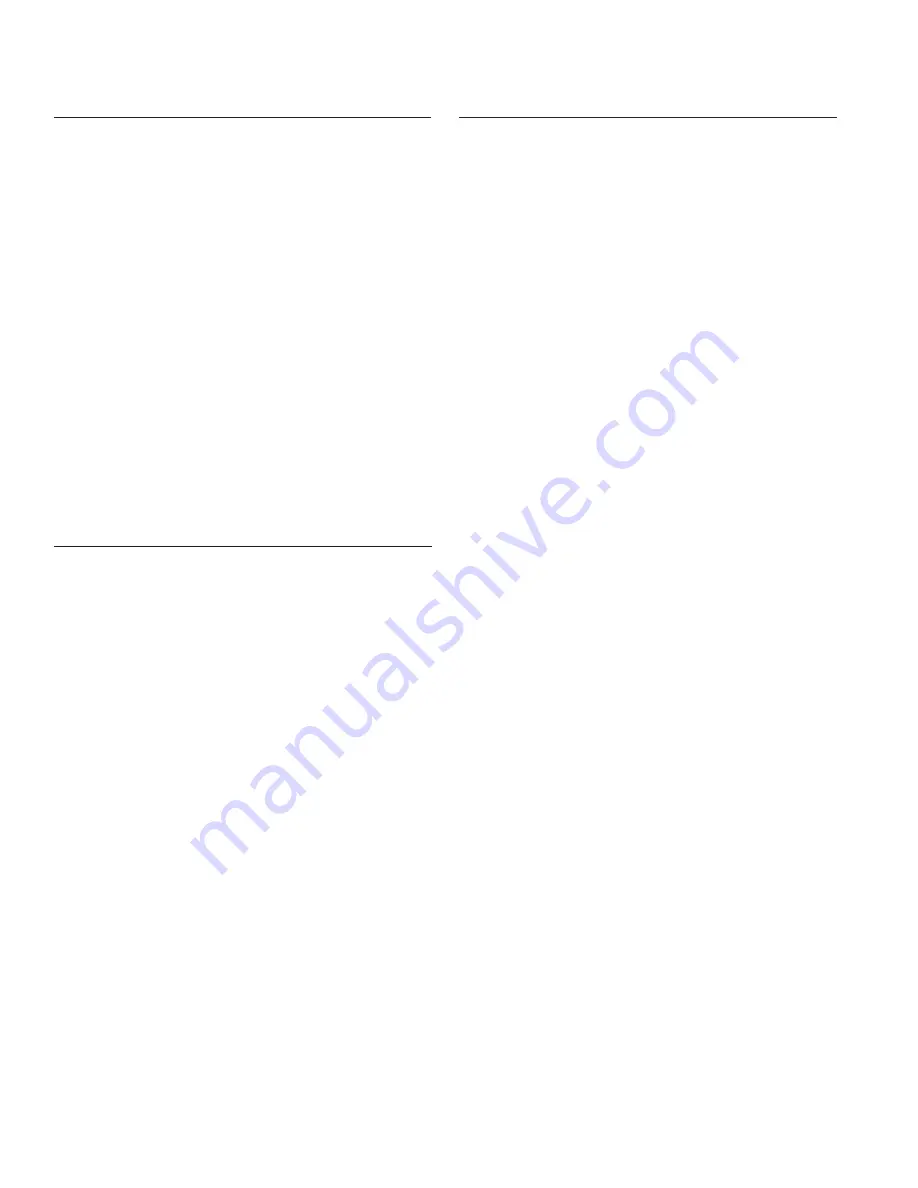
Fuel Shut-Off Solenoid
Carburetors are equipped with a fuel shut-off solenoid.
Solenoid is attached to fuel bowl. Solenoid has a spring-
loaded pin that retracts when 12 volts is applied to lead,
allowing fuel
fl
ow to main jet. When current is removed,
pin extends blocking fuel
fl
ow.
Below is a simple test, performed with engine off, that
can determine if solenoid is functioning properly.
1. Shut off fuel and remove solenoid from carburetor.
When solenoid is loosened and removed, gas will
leak out of carburetor. Have a container ready to
catch fuel.
2. Wipe tip of solenoid with a shop towel or blow with
compressed air to remove any remaining fuel. Take
solenoid to a location with good ventilation and no
fuel vapors present. You will also need a 12 volt
power source that can be switched on and off.
3. Be sure power source is switched OFF. Connect
positive power source lead to red lead of solenoid.
Connect negative power source lead to solenoid
body.
4. Turn power source ON and observe pin in center of
solenoid. Pin should retract with power ON and
return to its original position with power OFF. Test
several times to verify operation.
Carburetor Circuits
Float
Fuel level in bowl is maintained by
fl
oat and fuel inlet
needle. Buoyant force of
fl
oat stops fuel
fl
ow when
engine is at rest. When fuel is being consumed,
fl
oat will
drop and fuel pressure will push inlet needle away from
seat, allowing more fuel to enter bowl. When demand
ceases, buoyant force of
fl
oat will again overcome fuel
pressure, rising to predetermined setting and stop
fl
ow.
Slow and Mid-Range
At low speeds engine operates only on slow circuit.
As a metered amount of air is drawn through slow air
bleed jets, fuel is drawn through 2 main jets and further
metered through slow jets. Air and fuel are mixed in body
of slow jet and exit to transfer port. From transfer port,
air fuel mixture is delivered to idle progression chamber.
From idle progression chamber, air fuel mixture is
metered through idle port passages. At low idle when
vacuum signal is weak, air/fuel mixture is controlled by
setting of idle fuel adjusting screws. This mixture is then
mixed with main body of air and delivered to engine.
As throttle plate opening increases, greater amounts of
air/fuel mixture are drawn in through
fi
xed and metered
idle progression holes. As throttle plate opens further,
vacuum signal becomes great enough so main circuit
begins to work.
Main (high-speed)
At high speeds/loads engine operates on main circuit.
As a metered amount of air is drawn through 4 air jets,
fuel is drawn through main jets. Air and fuel are mixed
in main nozzles then enters main body of air
fl
ow where
further mixing of fuel and air occurs. This mixture is then
delivered to combustion chamber. Carburetor has a
fi
xed
main circuit; no adjustment is possible.
Carburetor Adjustments
NOTE: Carburetor adjustments should be made only
after engine has warmed up.
Carburetor is designed to deliver correct fuel-to-air
mixture to engine under all operating conditions. Main
fuel jet is calibrated at factory and is not adjustable.
Idle fuel adjusting needles are also set at factory and
normally do not need adjustment.
Low Idle Speed (RPM) Adjustment
NOTE: Actual low idle speed depends on application.
Refer to equipment manufacturer’s
recommendations. Low idle speed for basic
engines is 1200 RPM.
Place throttle control into idle or slow position. Turn low
idle speed adjusting screw in or out to obtain allow idle
speed of 1200 RPM (± 75 RPM).
Governed Idle Speed Adjustment (If equipped)
1. Hold governor lever away from carburetor so throttle
lever is against idle speed (RPM) adjustment screw
of carburetor. Start engine and allow to warm up,
then adjust screw to set approximately 1200 RPM.
Check speed using a tachometer. Turn adjustment
screw (inner) clockwise (in) to increase or
counterclockwise (out) to decrease speed.
2. Release governor lever and check that throttle lever
is in idle position. Turn governed idle adjustment
screw to obtain equipment manufacturer’s
recommended idle speed (1500-1800 RPM). Some
engines have a bendable tab that is used to set this
speed. A pliers should be used to bend this tab to
achieve recommended speed. Governed idle speed
(RPM) is typically 300 RPM (approximate) higher
than low idle speed.
3. Move throttle lever to wide-open/full throttle position
and hold in this position. Turn high speed screw to
obtain intended high speed no-load RPM. Governed
idle speed must be set before making this
adjustment.
High Speed (RPM) Adjustment
1. With engine running, move throttle control to fast.
2. Turn inner adjustment screw outward to decrease, or
inward to increase RPM speed.
3. Stop when desired RPM speed is obtained.
Fuel System
24
24 690 34 Rev. D
KohlerEngines.com