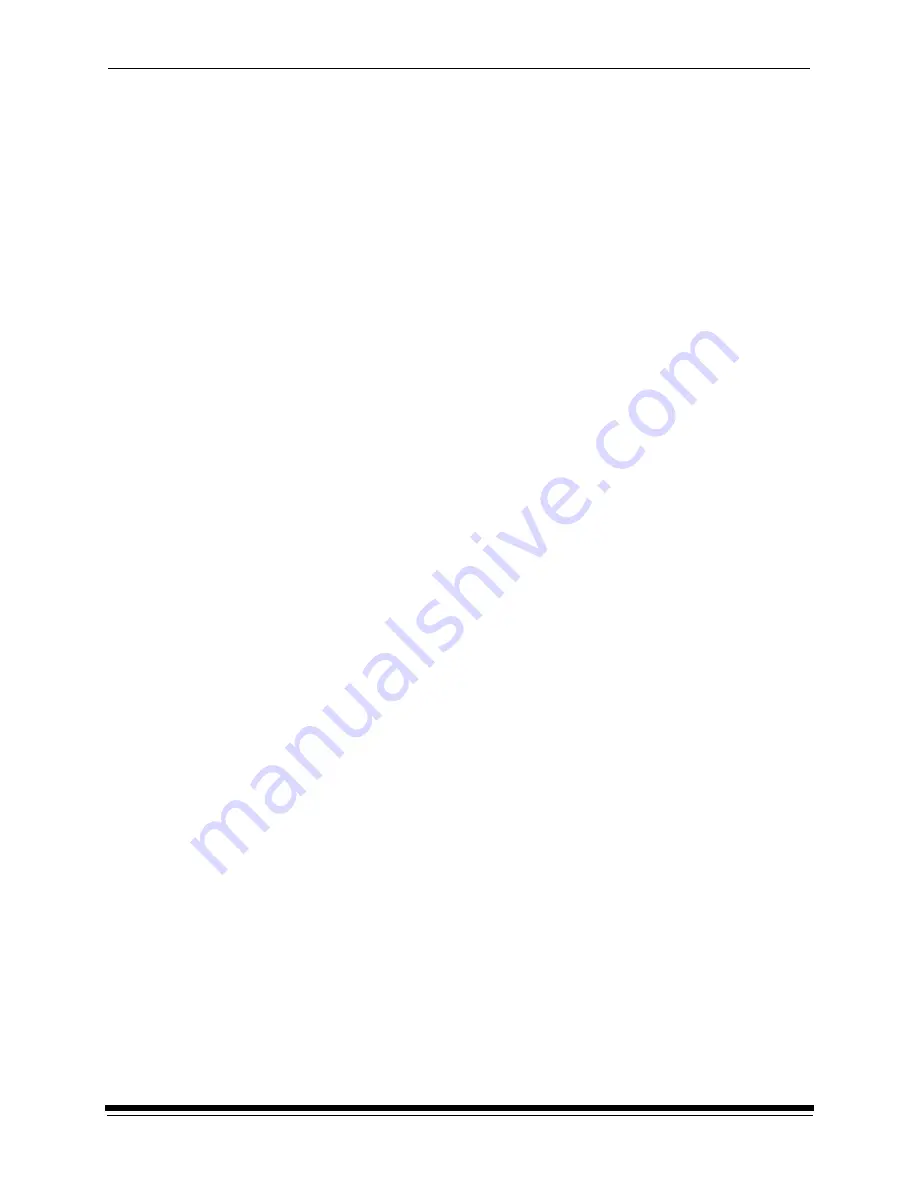
September 2000
ix
Viewing/Setting Replenishment Settings ...................................................................... 3-36
Viewing the Replenishment Rate ...........................................................................3-36
Setting the Chemical Replenishment Rate ............................................................3-36
Setting the Wash Replenishment Rate ..................................................................3-36
Calibrating the Replenishment Flow Rate .................................................................... 3-36
Measuring the Flow Rate .......................................................................................3-36
Entering the Flow Rate ...........................................................................................3-37
Managing the Development Time................................................................................. 3-37
Viewing the Development Time .............................................................................3-37
Setting the Development Time ...............................................................................3-37
Calibrating the Development Time .........................................................................3-37
Displaying the Min Max Development Time ...........................................................3-38
Managing the Material Sensors .................................................................................... 3-38
Viewing the Material ...............................................................................................3-38
Viewing the Processor Setup .................................................................................3-38
Selecting the Processor Setup ...............................................................................3-38
Controlling the Processor Drive .................................................................................... 3-39
Turning the Drive On ..............................................................................................3-39
Returning the Drive to Normal Operation ...............................................................3-39
Computer Reset ........................................................................................................... 3-39
Resetting the Processor .........................................................................................3-39
Loading the Defaults and Changing the Configuration ..........................................3-39
Changing the Wash/Stabilizer Setup ............................................................................ 3-40
Changing the Metric/Fahrenheit Mode ......................................................................... 3-40
Setting the Development Time Tolerance .................................................................... 3-41
Setting the Chemical Temperature Tolerance .............................................................. 3-41
Clearing Error Conditions ............................................................................................. 3-41
4 Maintaining the Equipment ................................................................................................................... 4-1
Maintaining the Printer .......................................................................................................... 4-2
Daily Maintenance .......................................................................................................... 4-2
Removing the Chad .................................................................................................4-2
Calibrating the Printer ..............................................................................................4-2
Periodic Maintenance ..................................................................................................... 4-3
Replacing the Air Filter .............................................................................................4-3
Maintaining the Processor..................................................................................................... 4-4
Daily Maintenance .......................................................................................................... 4-4
Chemistry Levels ......................................................................................................4-4
Replenishment and Effluent Chemical Levels ..........................................................4-4
Cleaning the Crossover Assemblies ........................................................................4-5
Operational Checks ..................................................................................................4-6
Testing .....................................................................................................................4-6
Weekly Maintenance ...................................................................................................... 4-7
Checking the Tension of the Main Drive Chain ........................................................4-7
Checking the Circulation ..........................................................................................4-7
Preventing Algae (for Wash Configuration) ..............................................................4-8
Cleaning the Crossover Assemblies and Transport Racks ......................................4-8
Cleaning the Feed Table and the Processor Entrance Sensors ..............................4-9
Replacing Chemical and Wash Filters ...................................................................4-10
Checking the Fittings for Leaks ..............................................................................4-10
Summary of Contents for PROFESSIONAL LED II 20P
Page 16: ......
Page 20: ......
Page 74: ......
Page 90: ......
Page 118: ......
Page 122: ......
Page 146: ...Additional Calibration Information C 12 September 2000 Value Graph ...
Page 147: ...Additional Calibration Information September 2000 C 13 Difference Graph ...
Page 168: ......
Page 190: ......
Page 197: ......