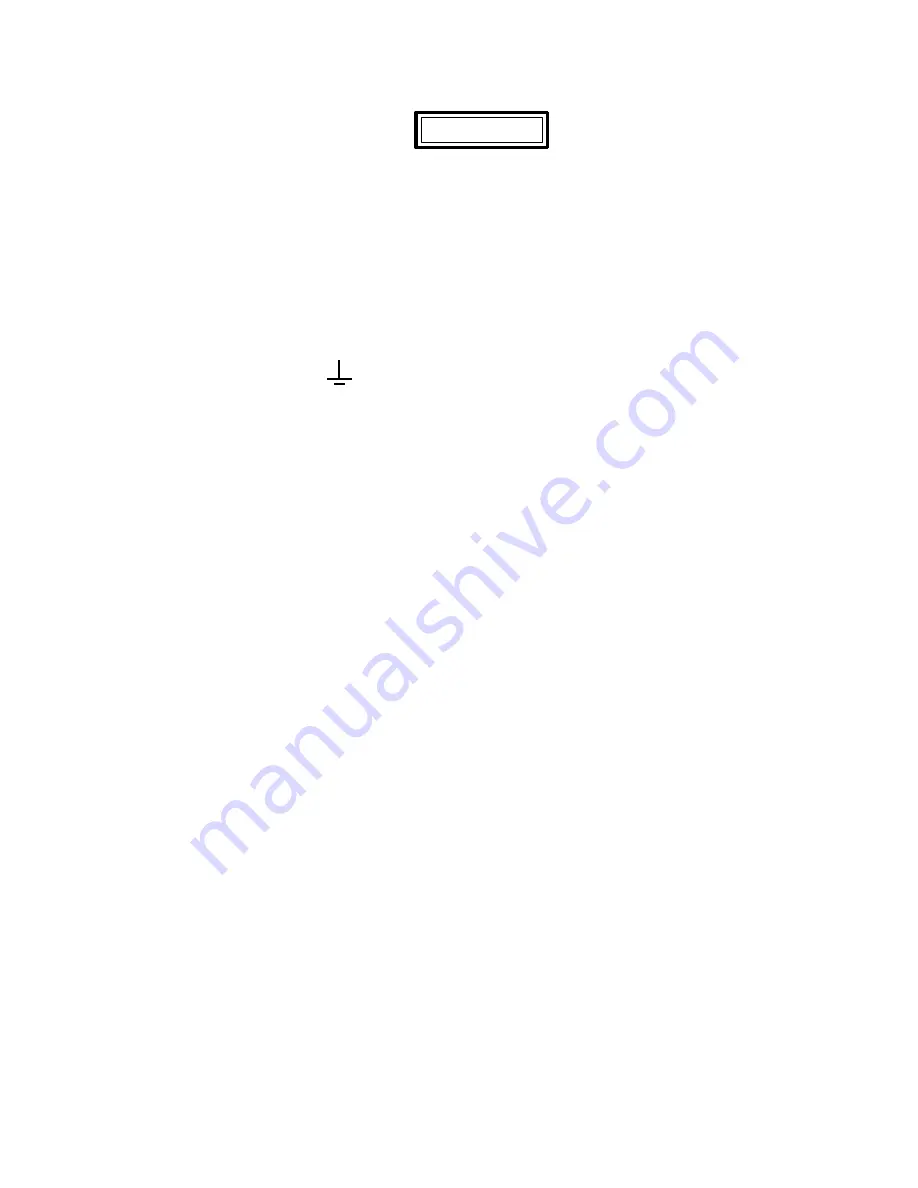
INSTALLATION INSTRUCTIONS
II 3239
© Kodak Ltd.
Page II-23
December 1992
2.
Connect power to the MINILOADER.
IMPORTANT
The wires in this mains lead are coloured in accordance with the following code:
GREEN AND YELLOW - EARTH
BLUE
- NEUTRAL
BROWN
- LIVE
As the colours of the wires in the mains lead of this appliance may not correspond with the coloured
markings identifying the terminals in your plug proceed as follows:
The wire coloured green and yellow must be connected to the terminal on the plug marked with the letter
E or by the earth symbol
or coloured green or green-and-yellow.
The wire coloured brown must be connected to the terminal marked with the letter L or coloured red.
The wire coloured blue must be connected to the terminal marked with the letter N or coloured black.
Put one of the SERVICE KEYS into the KEY-SWITCH and turn the SWITCH on. Turn the
MINILOADER MAIN SWITCH on.
The DISPLAY should read "PLEASE WAIT-RESET OPERATING" and the ORANGE LIGHT should
be on. The CAM MOTOR should run until the "home" position is reached, then the ALARM will sound,
the RED LIGHT will come on and the message "MAGAZINE 18*24 NOT IN CORRECT POSITION"
will be displayed.
Press the RESET BUTTON twice (the first press silences the ALARM and the second press cancels the
message). The GREEN LAMP should come on and the DISPLAY should read "MINILOADER READY
FOR FORMAT 18*24".
If the MINILOADER does not operate correctly, consult the SERVICE MANUAL.
Open the FRONT DOOR and install the 24 x 30 cm MAGAZINE, loaded with TEST FILM, into the
lower MAGAZINE TRAY.
Press the SIZE CHANGE BUTTON once. The DISPLAY will read "CHANGING FORMAT", the
ORANGE LIGHT will come on, and the MAGAZINE CARRIAGE will take the 24 x 30 MAGAZINE to
the rear position. The GREEN LIGHT will come on, and the DISPLAY will read "MINILOADER
READY FOR FORMAT 24*30".
Install the 18 x 24 cm MAGAZINE, loaded with TEST FILM into the upper MAGAZINE TRAY. Close
the FRONT DOOR. The MINILOADER is now ready for testing.
Check the PUSH RODS etc. for tightness.
Clean the SUCKERS by rubbing them with grade 200 EMERY CLOTH, or a similar material, and dust
them with NATURAL TALCUM POWDER. If the surface of the SUCKERS is subsequently touched,
this procedure must be repeated.
Vacuum out the MINILOADER 2 PLUS to remove any dust.
3.
4.
5.
6.
7.