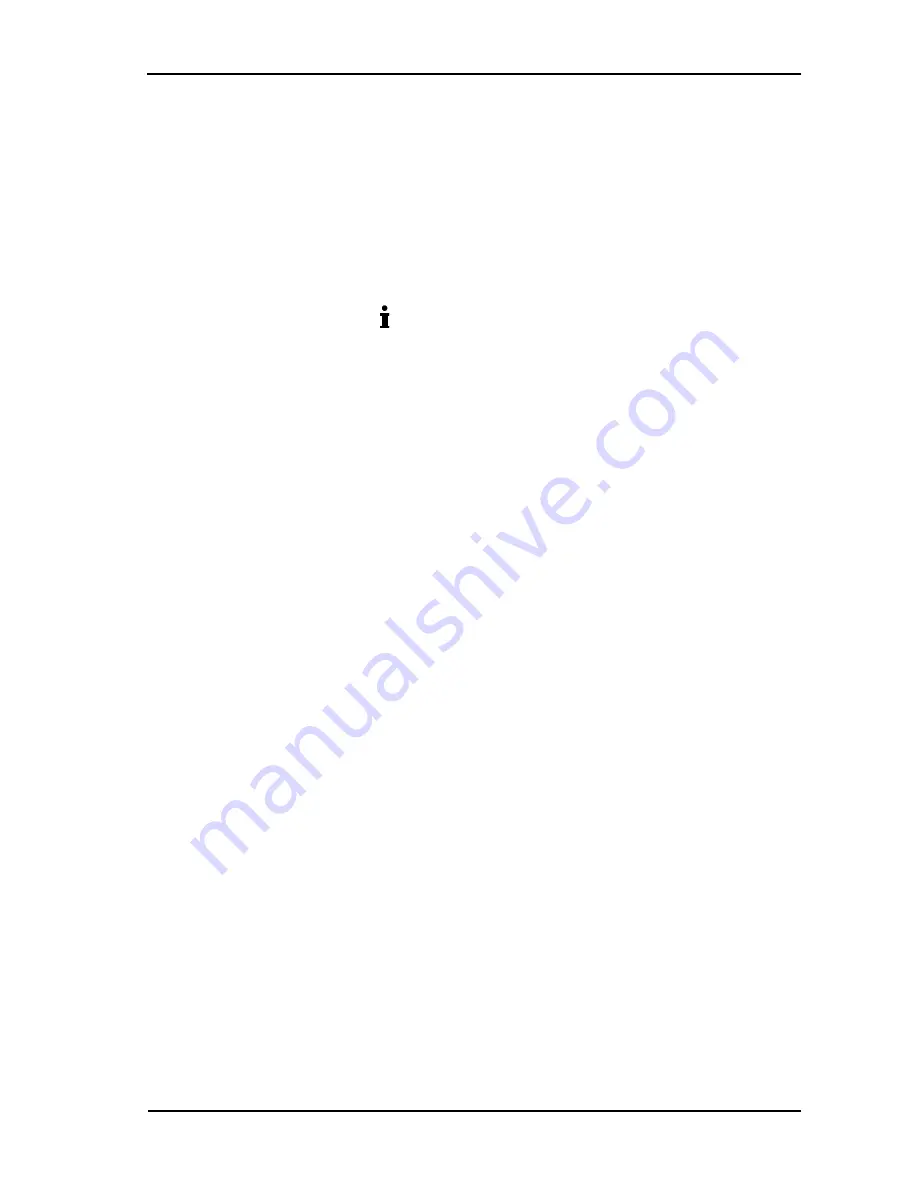
Swing Piston Compressor NPK03
Assembly and function
KNF Micro BA314221-314224 NPK03-EN-1217
Translation of original Operating and Installation Instructions, English
9
5.3. Pneumatic connection
Only connect components to the pump that are designed to
handle the pneumatic data of the pump (see Chapter 4, Tech-
nical data)
Only use hoses that are suitable for the maximum operating
pressure of the pump (see Chapter 4)
Only use hoses that are chemically resistant to the media be-
ing pumped
5.3.1. Connecting the pump
Arrows on the pump head indicate the flow direction.
1. Remove the protective caps from the hose
connections.
2. Connect the suction and pressure lines.
3. If the pump is used to build up pressure, make sure that all
transition joints between hose and pump are secure in order to
ensure that the hoses cannot come off.
4. Check that the hoses and transition joints (hose connect-
or/hose) are fitted correctly and securely.
5. Check that the system is leak-tight.
Connected
components
Hoses