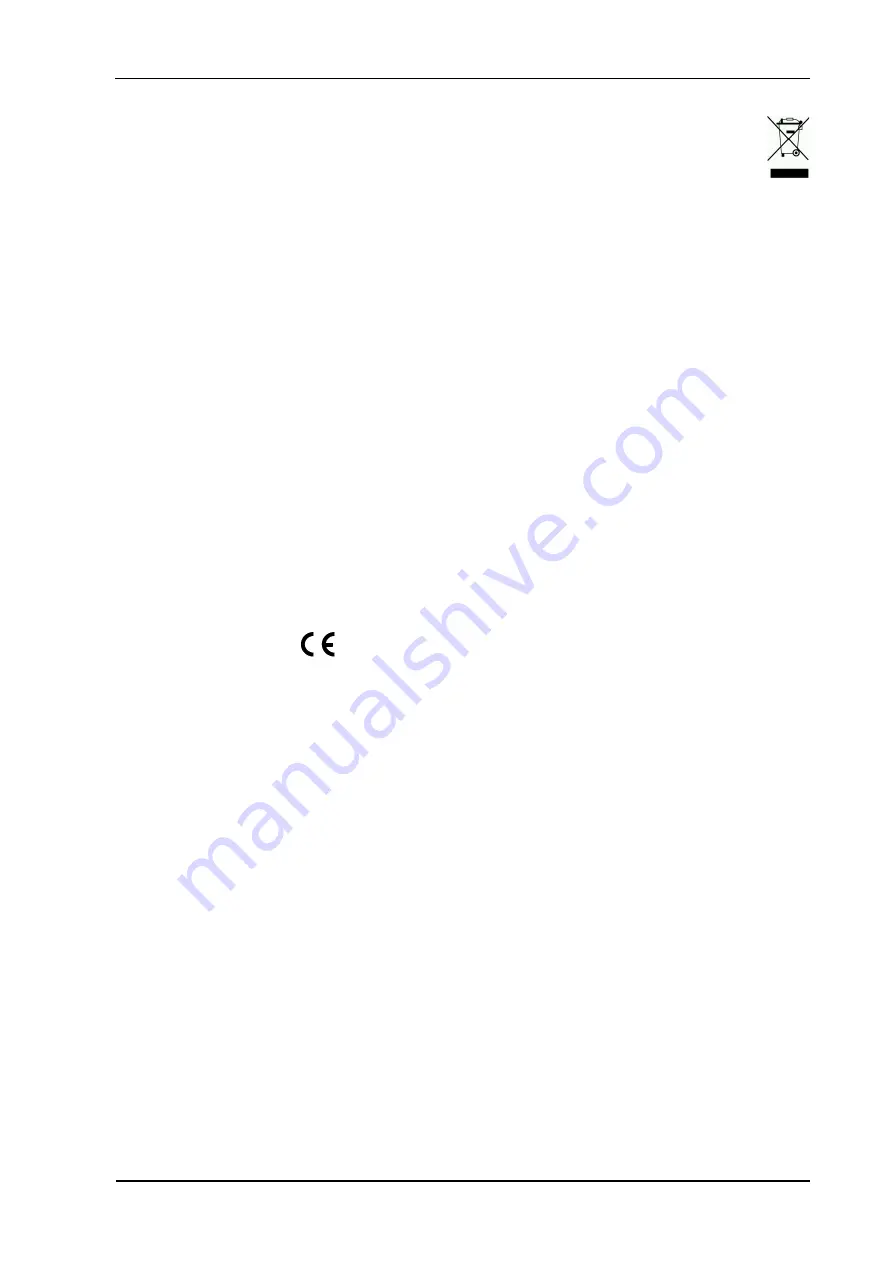
Diaphragm Pumps NMP830 HP
Safety
KNF Micro BA317001-316999 NMP830_HP-EN 0221.docx
Translation of original Operating and Installation Instructions, English
5
Dispose of end-of-life equipment in an environmentally
friendly manner. Use appropriate waste collection systems
for the disposal of end-of-life equipment. Used pumps con-
tain valuable recyclable materials.
For the purposes of the Machinery Directive 2006/42/EC, pumps
are “partly completed machinery", and are therefore to be regarded
as not ready for use. Partly completed machinery may not be com-
missioned until such time as it has been determined that the ma-
chine in which the partly completed machinery is to be assembled
conforms to the provisions of the Machinery Directive 2006/42/EC.
The essential requirements of Annex I of Directive 2006/42/EC
(general principles) are applied and observed.
-
General Principles No. 1
-
No. 1.1.2. / 1.1.3. / 1.3.1. / 1.3.3. / 1.3.4. / 1.4.1. / 1.5.8. /
1.5.9. / 1.7.4. / 1.7.4.1. / 1.7.4.3.
As these partly completed machinery are OEM-models the power
supplies and the equipment for disconnecting and switching-off the
partly completed machinery respectively have to be considered
when mounting as well as over-current and overload protective
gear.
In addition a protection against mechanical parts in motion, hot
parts, if existing, has to be provided when mounting.
The pumps comply with the fundamental requirements of Directive
2011/65/EU (RoHS2).
All repairs to the pump(s) must be carried out by the relevant KNF
customer service team.
Exception service interval: see chapter 7.3.
EU directives/standards
Customer service and repairs