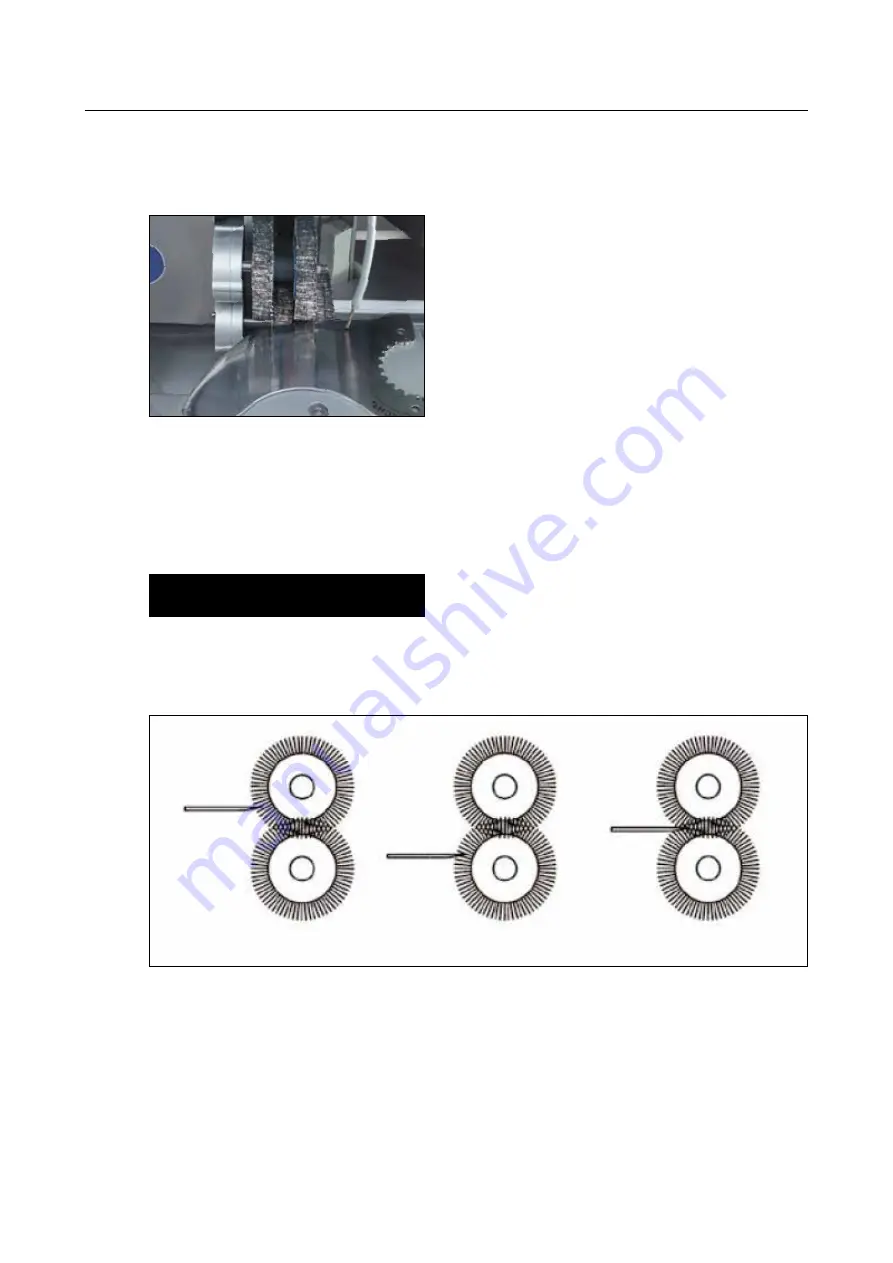
41
7.4 Adjusting the deburring unit
Because the upper and lower brushes of the
deburring unit wear in very different ways, the
position of the deburring unit must be readjusted
at regular intervals.
When deburring in automatic mode, stop and
press “Vacuum On” (7-9/2) button.
Using the touchscreen button “Deburring Unit
Forward / Backward” (8-8/2) in manual functions,
swivel the deburring unit to the knife.
When using the hand wheel to adjust the height
of the “Deburring Unit” (3-2/3), adjust the deburr-
ing unit so that the cutting edge is at the point of
intersection with the finned brush.
ATTENTION
The height of the deburring unit must be
adjusted so that the point of intersection of
the polishing brushes lies on the knife edge.
7. Operation
Figure 7-11
Adjusting the deburring unit
Figure 7-12
Adjusting the deburring unit
Wrong
Wrong
Right